不二越 工具事業部 「もっと加工に革命(Revolution)を!」 ~最新工具の強みとは~
多彩な事業と技術で世界のものづくりに貢献している不二越の強みといえば、なんといっても“総合機械メーカー”だということだろう。1928年の創立より培われた生産ノウハウを有する強みのもと、世界中の製造現場に独自性の高い商品やシステムを提供し、生産ラインの高能率化に貢献している。
「もっと加工に革命を!」のスローガンを掲げている同社工具事業部。切削加工条件の多様化から、超硬工具の需要が拡大する中で、2015年には超硬材料開発プロジェクトを立ち上げ、2018年に超硬素材を内製化した。材料開発、製造設計技術開発に注力し、現在、1本の工具でなんでも加工できる汎用工具、用途に合わせてダントツの性能を誇る専用工具を有する『アクアREVO』ブランド工具を次々と進化させてラインナップを拡充しており、その勢いは止まらない。工具の生産拠点である富山事業所(富山市不二越本町)にある工具事業部を訪ね、お話を伺うとともに、新商品群のデモ加工や優位性を取材した。
切削工具は材料や部品の変化がキモ
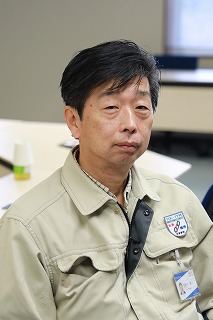
不二越の超硬ドリルは、1999年に初代『アクアドリル』、2008年に二代目『アクアドリルEX』、そして2018年に10年ぶりに三代目『アクアREVOドリル』が発売しました。材料・形状・コーティングを全て一新した、アクアREVOドリルの第二弾として昨年8月に登場した『アクアREVOドリルオイルホール』は、画期的なオイルホール形状により切屑排出性が向上したとして展示会でも注目を浴びた。一方、超硬エンドミルでは、2002年『GSミル』、2008年『GSXミル』に続き、昨年12月に市場投入した『アクアREVOミル』も評判は上々だ。このように超硬ドリル、超硬エンドミルともに着々とモデルチェンジを図りつつ、現在、「もっと加工に革命(Revolution)を!」をスローガンに工具事業部では、『アクアREVO』ブランドに注力し、製造現場にさらなる高精度と高能率をもたらす工具を開発している。
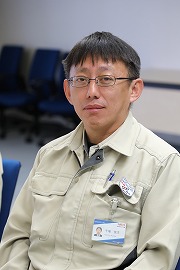
同社では、アクアREVOシリーズの他にも現在タップにも注力している。中でも最も注力をしているのは、『Hyper Z(ハイパーゼット)タップシリーズ』。干場俊洋 同 副部長は、「被削材、加工機械を問わず、安定した加工で長寿命を実現する工具です。社内でもホブやブローチ、転造工具などを扱うメンバーとコミュニケーションをとって、新しい発想のもと、別技術を活用しながら新しい商品づくりをしています。」とのことで、不二越ならではの特長を生かしたタップの拡充を図るとしている。
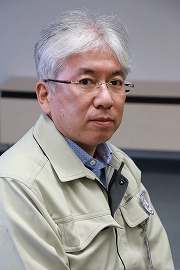
加工現場からの要望に挙げられる代表例といえば、①消耗品である切削工具の寿命を延ばしたい、②より早く加工したい(高能率化)、③様々なワークを同じ機械で加工するので、より幅広い材質でも使用ができる工具が欲しい、④精度向上――といったところだろう。圧倒的な工具性能を提供するために同社工具事業部が渾身の力を込めて開発した最新工具による加工実演を見学した。
最新工具によるデモ加工をレポート
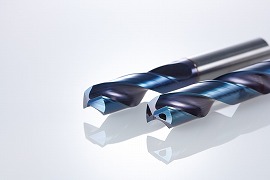
切削工具の重要要素といえば、材料、コーティング、そして形状だが、このアクアREVOドリルは、“直線刃形”を採用。切削時の応力を分散し、あらゆる加工条件で切りくず形状が安定している。
なぜ直線刃形なのか――というと、「直線刃形を採用することで、フック刃形では集中しやすいコーナーの応力を分散している。」とのことだった。
さぁ、実際の加工を見てみよう!
「アクアREVOシリーズ」、「Hyper Zロースパイラルタップ」のここに注目!
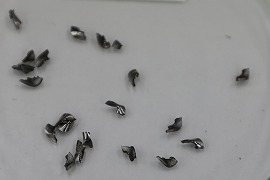
写真でもお分かりのとおり、アクアREVOドリルを使用した切りくずは、クルンとこぢんまりとしたカール状のものだった。
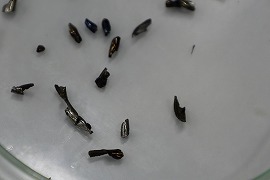
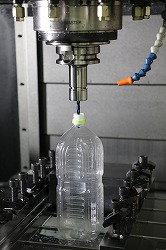
その2倍がどんなものなのかを実際に知るため、従来品とクーラント吐出量の比較を行った。使用工具はアクアREVOドリルオイルホール5D φ8.0、回転数は4800min⁻¹、内部給油圧力は1.5MPa。REVO Power Coolerは、ペットボトル1本分のクーラントを吐出するのに何秒かかるか、そして従来のオイルホール形状で同じ秒数ではどれだけ吐出できるのか―――。
ペットボトルにクーラントが勢いよく注がれた。そして出た結果が写真の通り、REVO Power Coolerはペットボトルが満タンになるまで11秒で1.0ℓ。一方、従来品は0.5ℓだった。
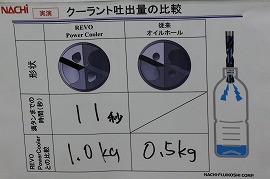
アクアREVOドリルオイルホールの注目点は、圧倒的な流量を確保しているとともに、切れ刃に近い位置から吐出させて切削点に供給できること。流体解析で最適なオイルホール形状を導き出した結果、熱を持ちやすいコーナーとシンニングすくい面をクーラントで狙い撃ちしている。これにより、刃先の冷却性、潤滑性、切りくず排出性も向上したのだ。
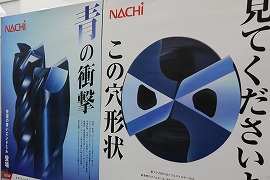
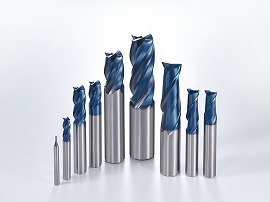
ゴゴゴゴ音と甲高いキィィイイイイイ音がする。機械の前に立っていると加工振動が足にも伝わってくる。おそらく加工現場で働いている方が、このような音を聞いたら不安になるだろう。
次にアクアREVOミルで加工。足に感じた振動もなく、音も静かだ。出来上がった面品位の比較は写真の通り、一目瞭然だ。
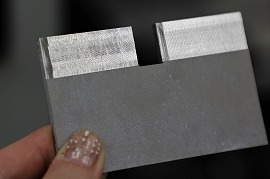
続いて、『Hyper Zロースパイラルタップ』の加工を拝見。ここでは切りくず形態を他社品と比較した。炭素鋼(26HRC)、ねじ深さは12㎜、水溶性切削油(Wet)、横形M/C(BT40)。切削速度は5m/min、回転速度265min⁻¹、送り速度265㎜/min。
他社品はモジャモジャした切りくずが発生! 重力による切りくずの重みの影響も心配だ。
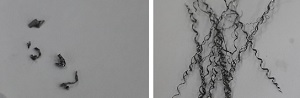
先端設備で工具を生産! そして工具を魅せるアイディアも豊富!

そして―――。
不二越独自のノウハウがびっしり詰まった工具が市場に披露される時、忘れてはならないのが、ここで活躍する同 工具企画部 営業企画室の存在だ。
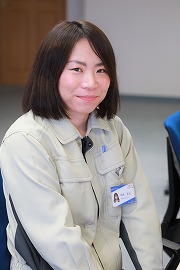
「このツルツル感を知ってもらいたいのですが、工具そのものを触るとケガのおそれがありますので、棒状のままにして、安全で安心して触れるサンプルを企画しました。」と柿島さん。
また、以前開催された展示会ではなにを訴えたいか、一目で訴求できる筆文字を利用したブース展開が話題を呼んだが、この筆文字も柿島さんが描いたものだ。こうしたブース内の装飾を社内で展開しているとは思わなかったので驚いた。自動化、IoTなど製造業界の最新トレンドの中にあって、人が描く筆文字の力強さから工具の“剛性”をイメージさせるという手法に思わず唸ってしまう。さすがだ!
最先端をゆく一方で、社内の人間がひとつひとつ丁寧に製品づくりと向き合っている印象を受ける不二越。今後も「ものづくりの世界に革命を起こす。」として、アクアREVOシリーズの拡充をしていく方針。
PRに使用されている筆文字は柿島さんが描いている。