【レポート】「牧野精機の機械を入れて良かったと言われたい!」~牧野フライス精機が新本社工場を完成! 生産能力が36%アップ!~
工具研削盤メーカーとして国内市場トップシェアを誇る牧野フライス精機(社長=清水大介氏)が、このほど新本社工場を完成した。同社は10年前からアジアを中心とした海外市場にも積極的に進出しており、国内外の旺盛な需要を取り込んでいるため、生産能力の限界が近いことに加え、今後の事業拡大を考慮して2015年より旧本社工場を解体しながら三期に分けて工事を進めてきた。総工費は25億円。これにより、生産能力は、旧工場対比で36%増となった。
幅広いラインナップと優位性
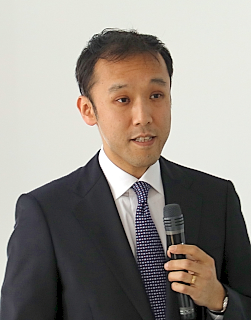
同社が製造している工具研削盤は、ドリルやエンドミル等の切削工具を製造及び再研削するための工作機械だ。航空機からスマートフォンまで世の中にある大半の製品、直接的、間接的にこの切削工具を用いた切削加工を経て生み出されている。切削工具はものをつくるための道具でもあることから、世の中にとっては必要不可欠なものであり、清水社長は、「弊社が製造している工具研削盤も必要不可欠、非常に重要な工作機械だと言えます。」と述べている。
同社の工具研削盤の歴史だが、万能工具研削盤「C-40」から始まる。清水社長はこの研削盤について、「1962年に牧野フライス製作所で開発され、1968年に当社に移管されたものであり、歴史的価値のある工作機械ロングライフ・ベストセラー賞を頂いています。」と説明をしており、50年以上たった今でも、同社ではこの機械を作り続けている。すでに世界で1万3,000台以上を販売しているというから、まさにロングセラー中のロングセラーだろう。
同社のNC化、数値制御化は1982年のこと。日本で初めて、ワンチャック全加工が可能なNC工具研削盤「CNX40」を開発した。これからも同社かなり早い段階でNC化に成功したことが分かる。
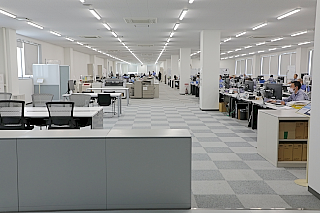
切削工具は通常、ブランク研削、もしくは段研と言われる円筒素材の大まかな形状出しを行って、工具研削で歯を付け、最後に測定をするが、この工具研削の前後工程に同社は2017年から進出をしている。この前後工程までカバーしている企業・メーカーについて清水社長は、「現時点で、世界では当社のみとなっています。」と優位性をアピールした。
これが新工場だ! 特長はダントツの生産能力!
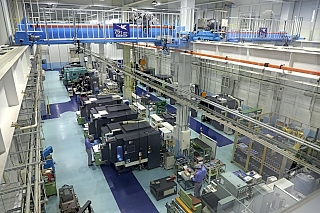
なぜ生産力が断トツでないと駄目なのか――の理由に、「当社のライバルメーカーは、主にドイツ、スイス、オーストラリアになり、その生産拠点は東欧、中国、台湾、タイ等、人件費の安い所に所在をしています。当社がここ日本で今後も製造していこうと考えたときに、人件費の差を跳ね返すためには、生産力がダントツでなければなりません。ダントツの生産力を達成するためには、旧工場では限界があるということを2012年終わりに判断をして、一気に工場建設に動き始めました。」と説明した。
新本社工場は、3つの棟をつなぎ合わせた形で構成されている。それぞれサイト1~3まであり、サイト1は1階、中2階、2階、3階、サイト2とサイト3は1階、中2階、2階という構造だ。
新工場1階は生産スペース機械の組み立てが重量に関係なくできるようになっているうえ、サイト2の2階が丸ごとユニット組み立てエリアとして使用できる。生産スペースの従来比較では、重量級工具研削盤をどこでも作れるようになったことを挙げた。機械の大きさは機種によって違うが、旧工場においては19台設置が可能だったことに対して、新工場ではマックスで30台の機械が設置可能だ。サイト2の2階が丸々ユニット組み立てエリアとして使用することができるので、生産スペースは旧工場と比べるとかなり広がった。
物の整流化については、サイト3をパーツ供給センターに機能特化させることで、整流化を実現した。基本的には、ここで物を受け入れ、サイト1のプロダクションエリアやサイト2の機械組み立てエリアに物を流す。サイト3で物をストックしておいて、サイト2のユニット組み立てエリアのほうに物を流す―――ということで整流化を実現する。
社員が働きやすい環境へ
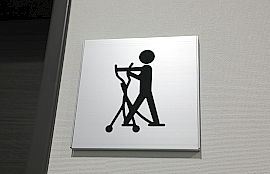
また、価格競争回避についても触れ、「新工場ができてスペースが広がりますので、サイト1の1階部にソリューションセンターを設けます。このセンターでは機械を常設して、テスト加工や加工ノウハウの蓄積、研究開発等を行う計画です。現在機械メーカーは、機械だけ売っていれば良い、という時代はとうに過ぎています。加工ノウハウ等までを提供していかなければ簡単に価格競争に巻き込まれてしまう。今後はIoTを念頭に置いた研究等も実験を通して行う必要があり、ようやくこのソリューションセンターが完成したことでその準備が整いました。」と意気込みを示した。
最後に清水社長は、「新本社工場建設にあたり、思いがありました。それは、社員が誇りを持てる職場環境づくりを目指すということです。従来、中小製造業と言えば、どうしても老朽化した薄暗い工場というイメージがつきまとっていました。私はそうしたイメージを払拭して、社員が清潔で働きやすく、家族を連れて来たくなるような職場環境を目指したかった。様々な意見はあろうと思いますが、私は優れた製品というのは、良い職場環境から生まれると信じております。けっして華美ではなく、社員が気持ちよく働けるようなデザインを心掛けて工場を建設して参りました。」と新工場建設において率直な気持ちを話し、しめくくった。