三菱マテリアルの加工テストを密着取材! ~『DLEシリーズ』高精度部品加工市場の拡大とともに新アイテムを開発~
「ご安全に!」
ここは、岐阜県安八郡にある三菱マテリアル 中部テクニカルセンターの一室。開発本部と営業本部から新アイテムの開発における話合いが行われていた。同社は小物高精度部品に関するアプリケーションを増やし、今年はリーディングドリル『DLEシリーズ』からさらに角度違い3パターンのレパートリ拡大を予定するなど、精力的に開発を進めている。
現在、高精度部品加工市場は拡大している。主にトランスミッション関連、エンジン制御系の部品は形状が複雑化し、被削材自体も難削材化が進んでいる。特に燃料制御に用いられるインジェクション部品では、SUS304からSUS420J2や、KM材と言われる電磁ステンレス鋼が主流になり、かなり削りづらい部品がメインになった。同社では、小型自動旋盤を取り巻く市場環境において、「今後ますます部品の加工点数も増え、全世界的に右肩上がりの市場になる。」と予測。加工トレンドを掴んだ新アイテムを発売するにあたり、今回、貴重な加工テストの現場に足を踏み入れ、密着取材を行った。
小型自動旋盤をとりまく市場は拡大
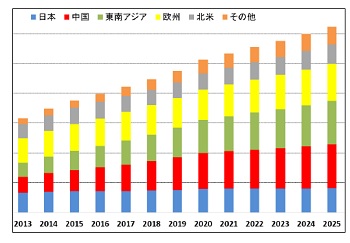
会議の席では、営業本部営業企画部の中山明信さんがDLEシリーズの市場要望について、「小物・高精度加工部品の市場は年々拡大しています。まず、トランスミッション関連では、低燃費化対策に向けたATの多段化・高機能化やCVTの制御の複雑化が進んでおり、それに伴い、ソレノイドの搭載数が増加しております。また、エンジン補器類関連では、ターボチャージャーやEGRバルブの適用車種増加により、排気温度の上昇に耐え得る耐熱鋳鋼やステンレス鋳鋼等、いわゆる難削材と呼ばれる材料の加工がそれらの部品向けに増えています。インジェクション(エンジン制御系関連)においても、これまでのSUS304 から、より切削が難しいSUS420J2や電磁ステンレスに主流が移っています。これらの難削材化により、工具費は従来比3倍増と、加工を取り巻く環境は厳しいものになります。」と説明した。
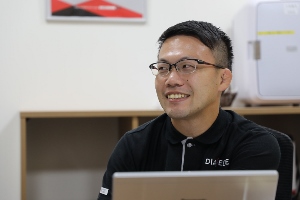
また、バー材の突っ切り加工後のボスが残った端面にセンターもみ付けを行う際には、より鈍角なドリルが必要でもある。つまり一般的な超硬ドリルの先端角140°よりも鈍角である145°が有効なのだ。なお、145°をラインナップするのは、主要メーカーでは三菱マテリアルが初めてとなる。
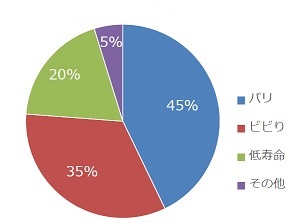
中山さんは、「これら課題に対しての解決策として、今回DLEドリルの開発テーマに決定しました。」と本題に進んだ。さらに、競合するA社2件(うち1件先端角違い)、B社4件(うち2件先端角違い&ハイスドリル)、C社1件の類似製品をターゲットにしてフィールドテストを行った結果を発表し、「他社相当品に対し勝率100%との結果を収めました!」とのこと。モニターには大きく勝率100%の文字があり、製品の強さを堂々アピールした。余談だが、中山さんは4年7カ月インドに駐在し、今年5月に帰国したという経歴の持ち主で、レスリングを愛するスポーツマンだ。
ユーザーの要望に応え、攻める開発魂!
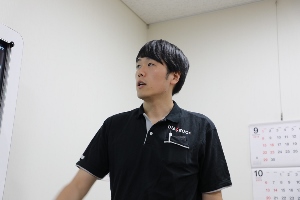
藤澤さんによると、DLEシリーズのラインナップは、90°ではφ3、4、5、6、7、8、10、12、16 。特に自動盤で広く使われているERコレットに適したシャンクサイズを揃えているのは嬉しい。

そこで今回、面取りに使わない中心部のみを鈍角にすることで、中心部の強度を確保してセンタリング加工時の突発欠損を防止したという。この特長的な二段先端角形状はこうした理由から生まれたものだった。さらにはこの二段先端角の範囲を極力小さくすることで面取りに必要である90°範囲を他社品よりも大きくし、使い勝手の向上も図っている。
コーティングに関しても触れ、「汎用材種であるDP1020(Al-Ti-Cr-N系コーティング)を採用しており、長寿命を発揮しています。また、ドリルシンニング形状を採用し、中心部にシンニングポケットを確保することで、中心の切りくずの排出性を促して、切りくずの噛み込みによるドリルの振れ等を防ぎ、良好な穴品位を実現できました。さらに切れ刃は切れ味が良い形状を採用しています。」と説明する表情は、どこか自信に満ちあふれていた。
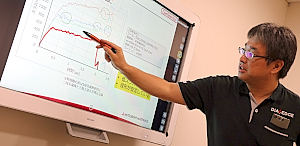
続いて、モニターにはセンタリング加工をしたときのスラスト抵抗を他社品A、Bと新製品DLEを比較したデータが映し出された。切削条件は、ツール:DLE1200S120P090(φ12)、被削材:炭素鋼S45C、Vc=60m/min f =0.1/rev、面取り径の狙い値をφ11 、クーラント:水溶性。
太い赤で書いてあるものがDLEの切削抵抗で、縦軸がスラスト抵抗値で波形が下に行けば行くほど抵抗が低いという意味合いを持っている。他社品と比較して分かるように、かなり抵抗が低くなっているのが分かる。また、他社品は波形が波を打っているが、DLEは波形が安定しているとの結果が得られていた。
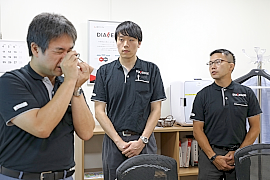
藤澤さんによると、「特にステンレス系については二段先端角形状が効果を発揮します。」とのこと。他社品A、Bにおいては、一律90°の設計だったが、先端部が欠損したという。それに対してDLEはその数倍削っても中心部が壊れることなく継続が可能となっていた。よって、ステンレスには二段先端角形状がかなり効果的であり、その威力は強かったことが証明された。
さらにバリの比較についてのユーザーテスト事例の説明では、他社品はバリが出ていたものの、DLEはほぼバリが無かった。藤澤さんいわく、「シンニング形状と切れ味に優れた刃先形状でバリが抑制できました。また、こちらのテストに関しても安定した寿命が得られました。」とのことだった。
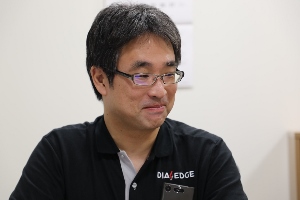
「先ほど、スラスト抵抗における波形の説明がありましたが、突発的に波形の上昇が認められる箇所は、切削抵抗が変動している要因は切りくずの絡み、もしくはバリの巻き込みが予想されるのではないでしょうか。開発の認識もそういう認識ですか。」と、江波部長補佐による若干のツッコミに、「はいっ!」と元気よく答える藤澤さん。(あぁ、こうして組織の中で若者は成長していくのだな。)となんだか微笑ましく和やかな気分になった。さぁ、次は場所を移して実機でテスト加工だ!
加工テストで分かった『DLE』の優位性とは!?
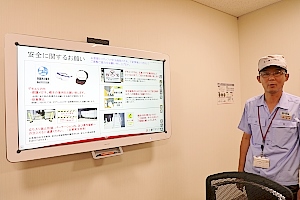
今回テスト加工に使用したマシンは、シチズンの『Cincom L20』 。同マシンは自動盤のベストセラー機であり、日本市場において多くのユーザーが使用しているマシンであるため、ユーザーでの再現性が高いとのこと。切削抵抗が変動しているのでは? という前提を基に、高速度カメラを使って切りくずの流れによる影響を確認するため、DLEと他社2メーカーを比較する。オペレータは中部試験Gの小寺恭介さん。
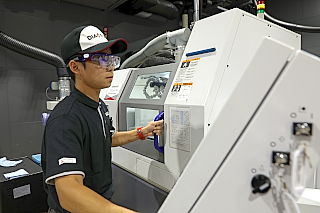
最初にDLEで加工しているモニターを拝見した。ドリルと被削材が接触をした箇所にバリの膨らみが見えず、切りくずがフルートに沿って排出されているのを認めた。このテストでは90°の先端角がついているドリルなので、穴が深くなるにしたがって切りくずの幅が広がっていく状態になりそうだが、最後まで切りくずが詰まることはなかった。
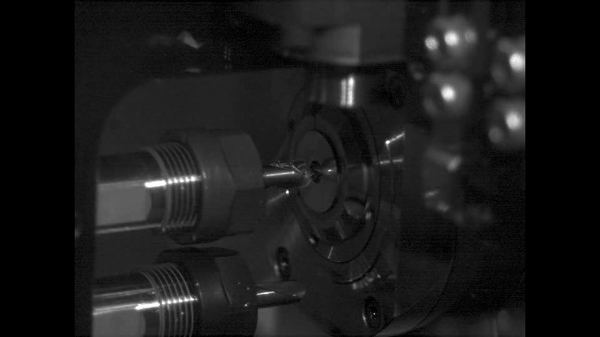
次にB社。切りくずが流れず滞留し、切りくず がグリグリに伸びてきている。フルートの距離が短くなっていることにより切りくず が詰まりやすいようだ。
続いて実際の自動盤ユーザーの加工実演を想定して、バー材を突っ切ったあとに外径インサートにより端面を加工した面にリーディングドリルを入れる加工を実施した。切削条件は以下の通り。
・端面挽き加工:Vc =100m/min, f=0.01mm/rev, ap=0.15mm
・穴あけ加工:Vc =30m/min, f=0.08mm/rev
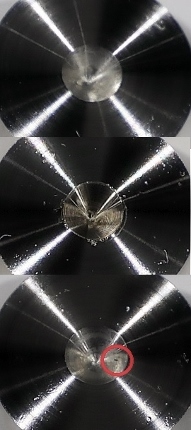
続いてA社。バリを認めた。面取りの中の部分の加工面は綺麗に見えるが、「切削抵抗が高くて切れ味も悪いということがあって、被削材を押し潰しているような加工面になっています。」とのこと。内側の加工面自体は光って綺麗に見えるが結局抵抗が高い分、外側のバリが大きく盛り上がってしまっているのがデメリットだ。
そしてB社。他社品Aと比較しパッと見はバリの盛り上がりは少ないが、触ってみるとうっすらバリが残っていることが分かった。よく見ると、加工面の真ん中付近に黒くなっている筋のようなものを発見! 「今からドリルを外してみますが、おそらくドリルの刃がチッピングしている影響が出ているのかと思われます。」とのことで、ドリルを外して確認をしてみると、あらやだ! 本当にチッピングを起こしているじゃないの!
「他社品Bは、抵抗も高くなく、一瞬切れ味が良いのですが、刃先強度が足りないので欠けてしまった。」という。これでは加工を重ねていけばいくほど、欠けがますます進行し、安定加工は困難になる。
江波部長補佐は、「切削抵抗が高いと塑性変形でどうしても口もとが盛り上がってしまう。これがバリの原因ですが、この厄介なバリがあると部品検査をするときに、どうしてもバリが邪魔をして全長が正しく測れない。もし、バリが剥がれたとしたら、部品同士を組み立てる際に精度が悪化してしまうことから、高精度部品を加工する現場では、バリを非常に気にするのは当然のことなのです。しかも、バリは怪我のもと。バリを取るために工程がさらに加わって加工時間も長くなり、生産性が落ちてしまう。」とバリが如何に加工現場で嫌われているかを丁寧に説明してくれた。バリは百害あって一利無しの厄介ものなのだ。
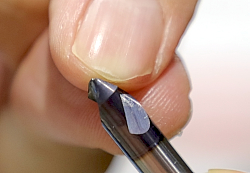
今回のシリーズ拡大の背景について、江波部長補佐は、「将来、部品点数は増え、より複雑になる部品加工には必要な工具だということで、今回はマーケティング主体で開発を進めました。一歩先ゆくお客様の将来に必ず役立つ最先端の工具です。」と話し、笑顔でしめくくった。
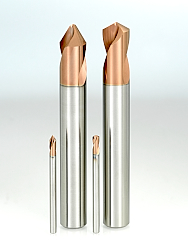