躍進する切削工具! 「2011年“超”ものづくり部品大賞」受賞工具はコレだ!
日本モノづくり日本会議と日刊工業新聞社が共催する「2011年“超”ものづくり部品大賞」。本年大賞に選ばれたのはJX日鉱日石エネルギーの「パラフィン系潜熱蓄熱材エコジュール」。
切削工具業界からは日本力(にっぽんぶらんど)賞に日進工具の「極微細ねじ加工用エンドミル マイクロねじ切り工具 MMTS」が、機械部品賞 に日立ツール/日立製作所の「AVアーバ(防振アーバ)」が、奨励賞にオーエスジーの「超硬油穴付きWDOドリルシリーズ」がそれぞれ受賞した。ハイクオリティな加工に貢献する切削工具メーカーの受賞工具を紹介する。
世界最小の呼び径0.1mm! 日進工具の「マイクロねじ切り工具」(日本力[にっぽんぶらんど]賞)
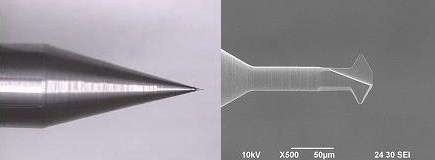
ねじのJIS規格では、メートル並目ねじとしてM1(ねじ呼び径1mm)からM300(ねじ呼び径300mm)があり、その下にミニチュアねじとしてS0.3(ねじ呼び径0.3mm)からS1.4mm(ねじ呼び径1.4mm)の規格がある。ミニチュアねじは、時計や電気機器、測定機などに用いられているが、微小であるため加工が難しい、使用時の作業性が悪い等の理由から、一般的に使用されるのはS0.5以上のサイズである。また、今回同社が製作したS0.1はJIS規格にないため、寸法やピッチなどはS0.3以上の寸法に則して独自に設定している。
よくあるねじの加工法は、おねじの場合は鍛造や旋削加工、めねじの場合はタップを使用した加工だ。切削タップも転造タップも共通している問題点はタップの折損である。タップが折損すると加工中のねじ穴に工具が詰まってしまい再加工するのが容易ではない。
この様な背景から、最近ではマシニングセンタに専用工具を取り付け、切削加工によりねじ加工を行うスレッドミーリング方法も多く採用されている。この方法は、穴径よりも工具が小径なので、①加工中に工具が折損しても容易に取り出せること、②切削抵抗が小さいため高硬度材や難削材への高精度な加工が出来ることを特長としている。
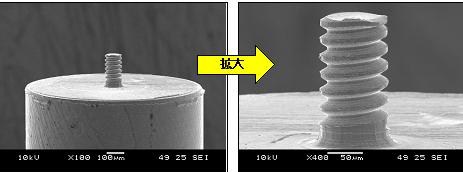
「マイクロねじ切り工具」を使用によって、S0.1(呼び径0.1mm)のおねじ及びめねじの加工が可能なる。被削材は、樹脂やアルミニウム合金に加え、医療機器や宇宙・衛星関係機器で多く使われるステンレスやチタンにも対応しているのが嬉しい。さらに特殊な機器は必要なく、一般的に使用されている高速マシニングセンタで使用することができる利点もある。
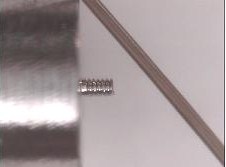
経済効果も高く、加工に際し特殊な機械を新たに導入する必要はない。一般的な高速マシニングセンタとこの工具があれば加工ができるので、設備投資、加工コストの観点からも優位性を誇るといえよう。この加工には、セミドライ加工が用いられているため、特別な溶液や大量の切削油剤を必要としないので環境にも優しく、また、使用部品の微細化が進むことで、組み上がる製品の微小化にも貢献できるということは、近年、価格高騰や埋蔵量の減少で問題視されているレアメタルの使用量も削減することができ、資源確保にも一層期待がかかる。
なお、同社では、小径サイズ、極小径サイズの超硬エンドミル、cBNエンドミル、超硬ドリルを得意としており、最小刃径10μmのエンドミルも世界で初めての量産化に成功している。
L/D=6以上の突き出し長さの加工のビビリ振動を抑制した日立ツール/日立製作所「AVアーバ(防振アーバ)」(機械部品賞)
機械部品賞を受賞した日立ツール/日立製作所の「AVアーバ(防振アーバ)」。
これは大型機械部品加工、大型金型加工及び工作機械製造分野でのL/D=6以上の突き出し長さの加工において問題となるビビリ振動を抑制し、大幅な加工能率向上が図れるとして高い評価を得ている。
ビビリが発生すると、加工面精度が悪化したり、工具寿命を短くしたりと品質や加工能率に悪影響を与える。したがって加工現場は常日頃、防振対策を考えなければならず、頭を痛めているとえいよう。クオリティの高い加工面に仕上げるためにはビビリをいかに回避するかがポイントになる。
ところが、L/D=6以上の突き出し長さの加工の問題点をあげると、ビビリ振動が生じ易いという点が挙げられる。このため切り込み量及び送り速度を小さく設定せざるを得なく、能率の低い加工が当たり前となっていた。同社では、このような現場の悩みを解決すべく、アーバ本体内にダンパー(動吸振器)を内蔵することで、減衰比が通常アーバの約6倍にした大きな特長をもつ。これにより、従来工具ではビビリ振動を発生する切込み量でも切削が可能になり高能率加工が実現し、安定した加工状態のためインサートの寿命が大幅に向上する。
AVアーバーは従来アーバーに比べて加工能率2.5倍、工具寿命10倍(φ50×L400mm時)の性能が得られるのだ。仕様も、φ40xL300mm、φ50xL350,400,450mm、φ63xL350,400,490mmと豊富であり、現在、多くの部品加工ユーザーで高能率加工を実現し、コストダウンに寄与している。 この製品は加工現場の生産性、経済性に大きく寄与するといえよう。
生産性を大幅に向上したオーエスジー「超硬油穴付きWDOドリルシリーズ」(奨励賞)

同製品は、径でφ3~φ20、対応出来る加工深さを径の30倍までと豊富なラインナップを揃え、加工深さ別に刃型の設定を行い、より多くのシチュエーションで工具の性能を安定して最大限発揮できるようにしている。
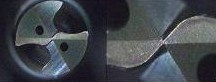
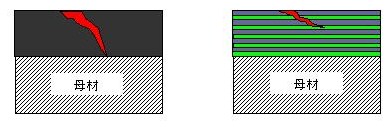