大平工具製作所 水谷社長に聞く「未来のために削り続けていく」
大平工具製作所(社長=水谷秀樹氏、本社:三重県松阪市大平尾町)は、今年で創業68年を迎え、長い歴史の中で、工具製作から培われた加工技術・技能で様々な苦難を乗り越えて、常に新しい分野へと挑戦してきた従業員数12名の会社だ。数物部品加工と金型製作技術に高い評価を得ており、信頼も厚い。現在、新型コロナウイルスの悪影響が暗い影を落としているが、3代目にあたる水谷社長は、「私が経営者となって初めての苦難であり、弊社の本質が試される時ですが、導入した新設備が打破してくれるはずです。」と、勢いがいい。
水谷社長に時短に成功した加工事例を含め、会社の歴史や、導入した新設備への思い入れ、現在の様子についてお話を伺った。
衝撃的な創業時の苦労話
―大平工具製作所という社名の由来について教えて下さい。
水谷 弊社の歴史は私の祖父が、丁稚奉公として大阪で鍛冶屋の見習いをしていたことからはじまります。時は流れ戦争が終わり、この松阪市で工具製造を商いとして起業しました。社名は単純に町名である“大平尾町(おおびらおちょう)〟からきておりますが、来る人来る人「たいへいさん!」と呼ぶので「たいへいこうぐせいさくしょ」にフリガナを変更したとのことです。ただ、これが”たいへい“=”太平”と、ほとんどの方がお間違えになります(笑)
―わたしも間違えてしまいました! 申し訳ありません。水谷社長はお祖父様の働いている姿を見ながら育っていったのですね。当時の思い出はありますか。
水谷 起業当初から私が幼少期のころ、社員といえば、言い方は悪いですが常識人は少なく、内職で煙草を巻いていた祖母の着物を盗んでお金に換えた社員、やくざに追われ逃げていった社員、10以上の数字が苦手なおじちゃん、道の側溝がトイレというおばちゃんなど、現代では考えられないほどインパクトの強い社員が在籍し、ショッキングな出来事もあったようですが、思い出の中の皆さんは、小さな私にとても優しかったと記憶しております(笑)。
―なかなか刺激的なお話で時代を感じますね(笑)。金属加工に着手したきっかけは?
水谷 祖父から父親に代が変わり、本格的に工具の製造と並行して旋盤、フライスを使用した金属加工に着手しました。初のNC機を導入したのは、私が小学校3年生(昭和57年)だったと記憶しています。この頃になると社員の様子も変化があり、もくもくと仕事に没頭する働き者の方ばかり。今でもありがたいことに当時入社の方が第一線で働いております。
―従業員の中には、水谷社長の成長を見続けていた方がいらっしゃるのですね。3代目を継承したときの心境はいかがでしたか。
水谷 私が入社した時はバブル崩壊で世間は騒ぎ、地元でも建設中のビルが途中で放置され、その傷跡がつい最近まで残っていました。当時は金属加工業としても弊社は新参で大得意先様もなく、寄せ集めだったからか価格面も大きく値引きされることもありませんでした。ただ、本業の工具関係は、確実に数が出なくなっていきました。この頃から、問屋が中国製に興味を示しており、モノ自体は単純な構造ですので、メイドインジャパンでなくても問題がないという理由があったようです。父は、そのころから「いずれ工具だけでは生きていけなくなるだろう。」と考えていたようですが、かといって大きな投資はせず、耐えに耐えました。私が入社した平成4~5年頃の設備はNC旋盤が3台、立形マシニングセンター4台がすでにありましたが、そこから約10年もの間、一切新規設備を導入することなく、来るものは拒まず、仕事だけを受け続けました。
―厳しい時代を耐え抜き、経営を見直したきっかけは。
水谷 転機が訪れたのは、近所の金型屋さんとの出会いです。cadcamの導入を決めかねていた父が、これについて、「どんなことが可能なのか見学して来い。」との命を下したのです。そこで私は“金型“という職業に魅了されていきました。金型屋さんの仕事を手伝いたいという私の願いもあって、ワイヤーカットを新規導入しました。当時、ワイヤーを所持している加工屋さんは周りにおらず、瞬く間にプレス金型屋さんに噂が広まりました。当時は、金型屋さんと加工屋さんの垣根が少しずつ低くなっており、お互いの長所を生かした関係性が出来つつありました。瞬く間に弊社は金型加工に適した機械、3Dcadcamなどの設備も増え、結果的に工具の需要が減ったその穴埋めになりました。さらに時は流れ、数物部品加工業と二足の草鞋を営むため、工場の増築に加え5軸加工機、3次元測定機、立形マシニングセンター2台を立て続けに発注導入しました。当時私の立場は専務でしたが、情報収集は私の仕事でしたので、好き勝手させていただきました。
「品質の高いものは国内で」 設備が危機を救ってくれた
―リーマンショックの時は苦しかったと思いますが、どうされていましたか。
水谷 バブル崩壊の時とは違い、思い切りその波をかぶり、経理を担当していた母からは毎日のように「金が足らん!」と言われ続け、多額の借金で設備投資を推進した僕も枕を高くして眠れない日々が続きましたが、そんな日々もそう長くはありませんでした。大手が安さを求め海外進出が本格化し、日本の製造業の衰退が危ぶまれましたが、仕事が0になることがなかったのは、「品質の高いものは国内で」という風潮があったからです。弊社のリーマンショック直前に導入した機械がここで活かされることになりました。特に5軸加工機はまだまだ国内で所有している所は少なく、従来からの金型屋さんをはじめ、試作、航空機関連、エネルギー関連から多くのお話をいただきました。
―高い品質へのニーズが現在の経営基盤に繋がったのですね。
水谷 リーマンショックを乗り越え、やっと落ち着いたと思ったら、この度のコロナ禍です。偶然ですが、今回もリーマン時と同じように直前に新規導入した設備があるのです。最高のピッチ精度を誇るマシニングセンターと、弊社初となるミーリング機能付き旋盤の2台。事実上私が経営者となって初めての苦難であり、弊社の本質が試される時ではありますが、この2台がかならず打破してくれると信じております。 ―現在保有している設備と貴社の優位性について教えて下さい。
水谷 弊社は立形マシニングセンターが7台、NCフライスが1台、NC旋盤が5台(Y軸付き1台含む)ワイヤーカットが2台、5軸加工機が1台、平面研削盤が1台、三次元測定機が1台です。数物から単品までお客様の“色“に合わせた適正品質、適正価格にてご提案させていただいております。複雑なものは、2Dcadcam、3Dcadcamを通し、モデル作成、支給からの迅速な対応と、上記機械による一貫したものつくりが可能です。他に焼入れ、メッキ等の外注様も協力してくださり、完品としての納入できることも弊社の優位性といえるでしょう。基本的に弊社設備でできるものであれば業種を問わず請け負っておりますが、大きく分けますと建機部品、自動車ラインなど専用部品や各種金型部品(プレス、樹脂、アルミダイキャスト、ゴム等)が現在の主力となっております。
最新設備はDMGMORIの「NLX2000/500」! お気に入りの切削工具で難易度の高い加工に挑む!
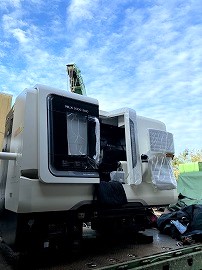
水谷 弊社設備の弱点であったNC旋盤の老朽化をこれで補うことができ、今まで避けていた精度モノに対する不安感が解消されました。また、従来からのワークを工程集約できることによって、マシニングへの負担も解消されることになり、現在大いに活躍しております。今後の期待としては、搭載の制御装置である〝CELOS(セロス)〟を駆使し、難易度の高い、特に単品に力を発揮してもらいたいと思っています。
―加工の難しい点はどういったところでしょうか。
水谷 “見えないところが難しい”点です。金属の特性上、歪が出たりもしますし、機能的な部分というのは地味ですが其処をどれだけつくり込むのかによって寿命が大きく変わりますので、私は展示会などでお会いしたメーカーの技術者に、サンプル加工品について問うのは派手な形状ではなく、「この立方体はどれだけ精密に直角が出ているのか?」、「ピッチ精度は?」、「ここまでの面粗が必要な用途とは?」であり、地味な部分をいかに高精度に仕上げてあるか、というところです。とはいえ、お客様がどれだけ其処を理解してくれるのか・・・もありますが(笑)
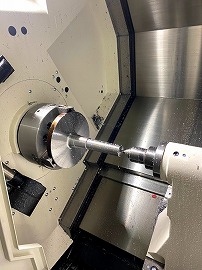
水谷 弊社は二足の草鞋で進めておりますので、その使用用途によって、さまざまな工具を使用しておりますが、主に数物部品加工の分野ではOSGの〝WXLシリーズ〟とフラットドリルの〝ADFシリーズ〟です。理由としては、〝WXL〟はそのコストパフォーマンスもさることながら実に汎用性が高く、さまざまな鋼材に適応できることです。一方の〝ADF〟に関しては、困難だった加工ができるようになった工具の一つであり、傾斜への穴あけ、底面フラットの加工、座繰りのスピード等、従来の穴あけが画期的に変わりました。数物に対する恩恵は素晴らしいものがあります。他にも、金型加工に関しては、MOLDINOの〝RH2P〟とダイジェット工業の〝ミラーボール〟、〝ミラーラジアスシリーズ〟。〝RH2P〟では金型向け高硬度材(HRC60以上)の荒取りがこの工具によって変わりました。弊社の実績ですがΦ32、ワンコーナーでHRC60の材料を約12時間削り続けたことがあり、途中で本当に刃先は大丈夫なのか? と確認するほどでした(笑)そして、〝ミラーボール〟、〝ラジアス〟ですが、この手の一枚チップ仕上げ工具では私が思う最高傑作です。
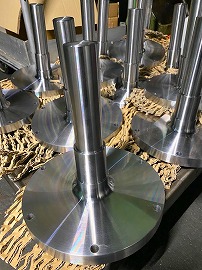
水谷 注目すべきはその装着精度です。他社製では微妙なズレがあり、仕上げ用としての魅力をイマイチ実感できていませんでしたが、このシリーズは誰が装着しても、老眼の私でも繰り返し精度がピカイチです。もちろん、その加工性にも満足しており、同社製の“頑固一徹”との組み合わせは最強ですね。あとチップの厚みもとても研究されたものだと思います。厚いチップはいかにも剛性が強そうですが、それを支えるボデーが貧弱では意味がないですからね。
―大変失礼な質問ですが、加工の失敗談はありますか。
水谷 実は人より多く失敗していると思っています(笑)。その多くは穴加工時に起こります。特に金型の深い冷却穴や、鋭角に交わったクロス穴などは、奥歯がガタガタになるほど(笑)。ただ以前は汎用機での加工が多く、この手の加工でミスは、ほぼなかったのですが不思議とマシニングでは予期せぬ事態に見舞われることがあります(笑)
―仕事で嬉しかったことは?
水谷 製品が出来上がった時は達成感もあり、嬉しいですが、一番は、お客様による評価が高かった時でしょうか。私自身が主に加工の担当をしているのは金型を主とする単品部門ですが、「お客様より良いものをつくらないと仕事なんてない!」の精神でやっていますので、高評価をいただけると、納品帰りの車中は、もう勝利の美酒のことで頭がいっぱいです(笑)
知恵を絞った加工で時短に成功!

水谷 これは特殊ジグですが、材質はS50Cで、交差自体も厳しいものではありません。しかし、加工順、工法を間違えればゆがみが発生し品物にならない難しさがありました。しかも1組16個が4組、5組の注文が来ます。試作では1個3時間。価格的にも納期的にも全く話にならないスタートです。しかし、ある意味こういった数物は、煮詰め甲斐があるというものです。
―これはどうやって加工したのですか。
水谷 加工機は50番主軸の三井精機の「VU65A」と決めていたこともあり、その特性を活かす工法に変更しました。その一つがワーク中心に開くΦ80の穴。とにかくコイツを瞬時に開けることができれば、と考え、このドリル(写真右下)を選定しました。想定以上に50番の能力を遺憾なく発揮し、大幅な時短に成功しました。
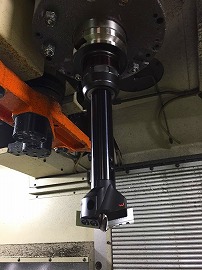
水谷 様々な細かい部分の変更もありましたが、数物ならではの悩みというえば、〝バリ取り作業〟です。とにかく手作業を減らすために機械加工化をいたしました。ここで生きてくるのが各加工箇所の精度。過剰品質は良いものではありませんが、指示なき全ての角部に糸面取りとなると一般公差とはいえ、そこそこの精度でできていないと機械加工では難しい作業になります。より速く、そしてこのような皮一枚の部分も安心できる工法を見つけることが数物の難しさでもあり楽しさでもあると思います。
―水谷社長はSNSの発進にも注力されていますが、メリットはありますか。
水谷 最大のメリットは、情報収集です! と言いたいところですが、実をいうと私にとってSNSは癒しなのです。というのもまだ、ネットでの会話が“掲示板“が主であったころ、夜中一人で加工をしている人間、こんなに苦しんでいる人間は自分だけじゃないんだ、と勇気をもらって以来、やめられなくなりました(笑)。そんなこともあり、SNSを営業的な使い方はしておりませんが、結果的に仕事のつながりができたという事例もありますし、SNSを通さなければ絶対に直接お話しする機会はなかったであろう方たちとメル友になれました。
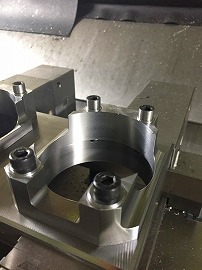
水谷 文字だけのやり取りで、相手の人間性まで決めつけることはできませんが、明らかに妙な方もいます(笑)。私は意味のない議論や難しい言葉でマウントを取るような話題には興味がありませんのでスルーしますが、これも苦い経験があってのこと。偉そうなことは言えませんが、とにかく文字だけというのは0か100で物事が伝わりやすいので、鵜呑みはよくないと感じています。情報がすぐ手に入る時代ではありますが、その得た情報を生かすも殺すも自分次第。結局考える力というのは今の時代、従来以上に必要になってきたのではないかと思っています。
―世界中が新型コロナウイルスの影響で非常事態に直面してしまいました。それでも人が生きている限り、モノは必ずつくられます。現在の仕事に関する感想をお聞かせください。
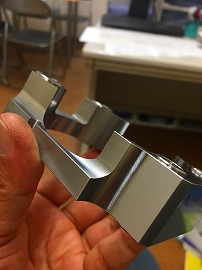
―コロナ禍の影響で、社内で変わったことや、従業員に対して注意していることはありますか。
水谷 コロナ禍とは直接かかわりがないのですが、安全安心面というものに対してより一層強化の心が芽生えました。具体的には、むき出しだったエレベーターを金網で囲い、扉が開いていれば作動しないようにしました。あとは働き方改革も重なり、社則を一から見直し、無理をしないよう健康面に対する事項を重点的に改善いたしました。
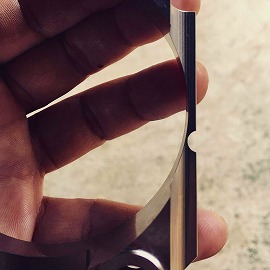
水谷 今のご時世、いい意味で使われなくなってきましたが〝お客様は神様〟という気持ちで接しています。ただ、お客様が〝下請け様は宝です〟と感じていただき、始めて成立する関係とも思っていますので、新しい風潮(ドライな関係)に惑わされぬようにお互いの立場を尊重しながら、関係を維持していければと考えています。
―現在、世界中が厳しい時を過ごしていますが、その中でも期待したいことはありますか。
水谷 個人的には、ずいぶんさまざまなものに挑戦してきたという自負がありますが、今後はわが社の宝である社員がそうした挑戦ができるよう環境を整えていく所存です。それには会社の発展がなくてはあり得ませんし、各個人の意識も必要です。家族経営ではワンマンになりがちですが、お互いの意識、立場を尊重しあえるような意見が出てくると願うばかりです。そのための秘策としてシステムを近いうちに導入します。また、現在1名の有望な人材が入社予定です。
―以前も貴社を取材しましたが、非常にアットホームな雰囲気です。
水谷 弊社は比較的優しく物静かな社員ばかりで、人間関係などで悩む要素はありません。同じ世代の同僚と賑やかに和気あいあいといったことができるほどの社員数もおらず、大手企業とは違いますが、アットホームな居心地の良い社風であると思います。経験者の募集もしておりますので、興味のある方はぜひお声かけください。
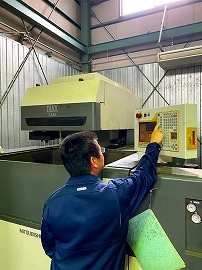
水谷 ちょうど、ドラマ“下町ロケット”の再放送を観たばかりで、影響されやすい私は、あんな風に世紀の一大イベントに少しでも協力できたら、それだけの技術力を身につけられたら・・・など夢を描いております(笑)。ですが、5軸加工機だって、高精度マシニングセンターだって、かつては夢でした。こんな田舎の小さな零細企業が町の誇りとして認知され、地元に愛される会社になれれば、と思い描く未来を想像しながら今後も削りつづけていきます。
―ありがとうございました。