【最新加工技術】三菱マテリアル 自動盤加工向け工具『MS9025』が満を持して登場! その舞台裏を拝見!
耐摩耗性も耐欠損性も向上させた皮膜 ~Al有量をアップした世界初の〝アルミリッチテクノロジー〟~
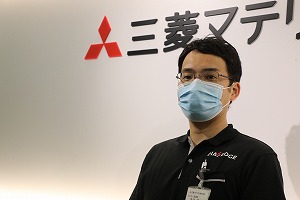
営業企画部の要望を受け、開発本部 材料・コーティング開発センターの淺沼英利センター長補佐(博士〈工学〉:以下淺沼センター長補佐)が、「今回、耐摩耗性小物高精度加工用PVD材種『MS9025』を開発しました」と発表した。淺沼センター長補佐によると、「耐摩耗性向上と耐欠損性向上を同時に求めることは、材料学的には相反することだ」という。
「実際、今回の開発ではそこが非常に苦労したポイントになります」と開発の苦労を滲ませた。開発の取り組み内容は、次の通り。
(1) 耐摩耗性の向上(皮膜開発)
皮膜開発を行い、競合他社品に対して1.5倍以上の刃具寿命の向上と寸法変化の抑制を行った。
(2) 耐欠損性の向上(母材開発)
競合他社品に対して耐欠損性能の向上を実現した。(バリが残った加工面、材料ボスの除去時の安定化を図った)。
(3) 加工精度対策(研磨技術開発)
・刃先品位の向上〈シャープエッジ〉。
・溶着を抑制した。
・コーティングの平滑さを実現した。
(4)新加工技術の適用(実地改良)
・振動切削加工環境下での優位性を高めた。
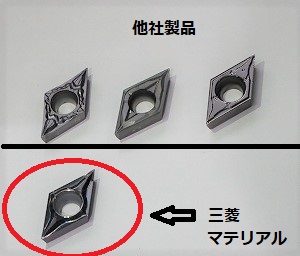
淺沼センター長補佐は上記の取り組みについて、「耐摩耗性と耐欠損性の向上を両立させるために皮膜開発には耐摩耗性の効果を付与し、超硬合金の母材には耐欠損性の効果を付与しました。切削工具は母材と皮膜の組み合わせになるので、それぞれに特性を持たせることによって耐摩耗性も耐欠損性も向上させる手段です。お客さまは高い精度を求めており、対応するためにもシャープエッジにする必要があるのですが、シャープエッジだと刃先の強度面からすると不利であり、すぐ欠けてしまうというような点があります。この課題に対して、今回は超硬合金の母材を開発することによって、シャープエッジでも欠けにくい材料を開発しました。また、溶着の抑制につながりますが、コーティングの平滑さという点では皮膜開発で取り組みました。」と説明をした。
さて、この新製品『MS9025』のコーティング技術に注目したい。今回はアルミ含有量をアップした〝アルミリッチテクノロジー〟が採用されている。ここが今回のキモでもある。
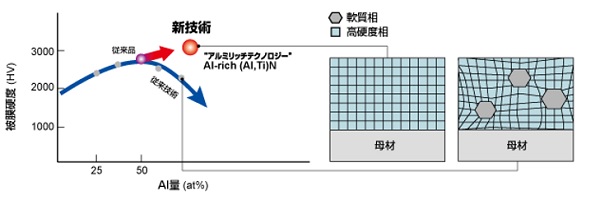
アルミ量を増加させていくと硬さが向上していくが、あるポイントを超えると硬さが低下してしまい、切削工具には向かなくなる、という従来の技術を超えるべく、今回は、全く新しい手法を用いてアルミ含有量をアップした皮膜を作り上げたという。
淺沼センター長補佐は、「新皮膜は、PVDコーティングのプラズマを最適化することによって、従来達成できなかったアルミ量を増加させつつ硬さも上げるという技術を開発したもので、これがアルミリッチテクノロジーとなりました。従来品と比較しても大幅にアルミ量が高いアルミチタンナイトライドになっています。これによって、高い硬さかつ耐熱性に優れたコーティングが実現できました」とアピールした。
母材で熱伝導性を良くし、刃先もシャープで欠けにくく!
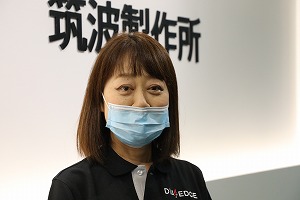
自動盤の加工では、一般的に使用するインサートはノーズRも小さめでスクイ角が大きくなっている、つまり刃先がとがっている部分に熱がこもり、欠けてしまうという問題があった。更に追い打ちをかけるのは、自動盤では油性クーラントを使用していて冷却性能でも一般的なNC旋盤加工よりも不利である。これが加工現場を悩ませていたが、それを回避するためには、母材の開発も重要である。
「今回、新開発した『MS9025』では、WC(タングステンカーバイド)を粗粒にすることで、熱の伝導性を良くして、刃先に熱がこもりにくく欠けにくい開発を行いました。一般的に市場のトレンドとしては、WCは微粒にしていく流れになっていますが、今回、WCを粗粒にするということに取り組みました」と、開発本部の永山千津子さん。
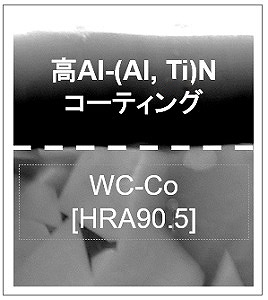
粗粒にした理由はこうだ。
粒径が荒いと熱が大きく拡散していく。永山さんは、実際にWCを熱して熱の拡散を比較したという。永山さんは、「超硬合金はWCやコバルト等から成り立っていますが、熱はWCの中を通っていきます。間にコバルトが入ることによって熱伝導が阻害されるため、WCが荒いと、熱が大きく侵入して熱が拡散しやすくなります。これが微粒だと間に入ったコバルトで熱が拡散しにくくなってしまう。WCを粗粒にすることで熱の拡散がスムーズに行われるようになり、刃先の熱伝導性が良くなるのです。」と説明した。
WCを粗粒にすることで熱の拡散がスムーズに行われるようになり、刃先の熱伝導性が良くなった―――とのことで、次は、刃先である。続いて、同じく開発本部より江畑大輝さんが説明に立った。
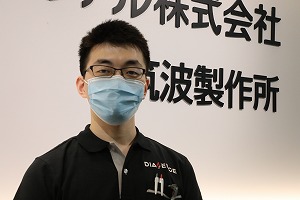
「熱をしっかり伝達するために粗粒のWCを採用しましたが、その一方で、粗粒にすると、エッジの部分がガタガタになってしまうという新たな問題点が浮上してきました。そこでわれわれは、母材の表面を研磨する技術を改良し、試行錯誤した結果、粗粒でありながら、刃先がシャープで綺麗な状態を達成することに成功しました」と自信を示した。
実際の工具を見せてもらったが、ツルツルのピカピカだ。江畑さんは、スクリーンに『MS9025』、他社品のA、Bと比較した刃先を映した。
「例えばこの他社品のほうを見ると、エッジの稜線部分に、膜が剥離してしまっている部分があるのですが、今回開発したMS9025材種では、シャープなエッジの部分にも皮膜がしっかり付いています」(江畑さん)
また、営業企画部から要望にあった振動切削への対応の結果だが、実際に加工テストを見せて貰い、その評価をスクリーンで拝見した。
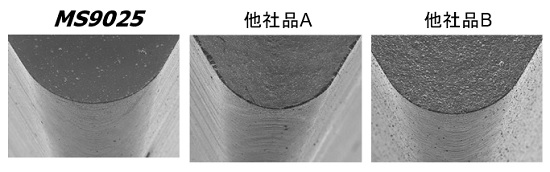
これが強くて美しい『MS9025』の実力だ!
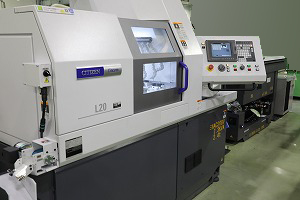
振動数なしの慣用切削では、被削材SUS304に対し、他社品2社の製品と比較したところ、他社品2社では、切り込みの境界部分で境界損傷が起きてしまい、工具摩耗の幅が非常に大きくなっているのに対して、『MS9025』は、摩耗の幅も小さく、境界の損傷がなかった。
次は振動切削だ――ー。
工具を切削方向に振動させることで、切りくずを細かく分断しながら加工することで、切りくず絡みがなくなることにより、加工コストの削減や生産性アップに貢献する最新の加工である。一般的な切削加工と違い、加工中に振動が生じることによる刃先負荷や性質上加工硬化を起こした部位への衝撃で刃先にダメージが生じやすいという切削工具にとっては、過酷な加工でもある。
機械を触るとブブブブブブブブブブブブブ~と振動が伝わってくる。今回は、振動数D1.25 per revolution(ワークが1回転するまでに何回振動するかを示す数値)。
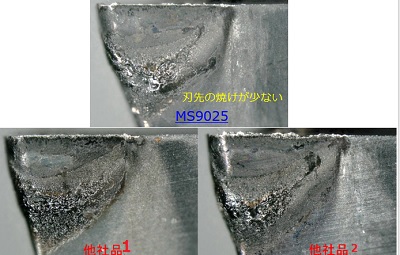
つまり、1回転するまでに1回以上刃先がワークから離れて切りくずが分断される仕組みとなっている。この条件では他社品のものは刃先全体の損傷が大きいものや、特に最外径部に境界摩耗が進行しているものが見られたが、同社の『MS9025』では、非常にきれいな刃先の状態を保っていた。
今回、新たに市場投入される次世代工具『MS9025』は、次世代の安定した加工を求める加工現場のために作られた工具であり、それぞれの部署がタッグを組み、様々な工夫と検証によって出来上がった工具だった。なお、同社では、まだまだ隠し球があるとのことで、今後の展開に目が離せない!
なお、今回取材をおこなったMS9025は、7月20日にプレスリリースされ発売が開始される。新製品としての情報も下記リンク先にアップされるので、今回の取材記事で興味がある方は是非チェックを!