アマダマシナリー 厚板シャーリング市場、鉄骨FAB向けに開発した「LC-VALSTER」-AJシリーズで鋼材・鉄骨市場に新風!
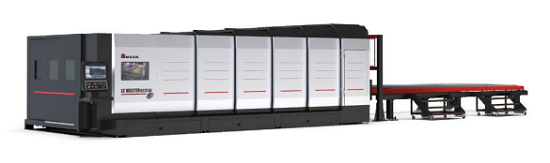
アマダマシナリー(社長=田所雅彦氏)が中厚板大板材の高速ピアス加工と高品位切断加工を実現するファイバーレーザマシン「LC-VALSTER-AJシリーズ」のリリースに伴い、11月18日、アマダ富士宮事業所で会見を開いた。
中厚板大板材を扱う鋼材の加工現場では人手不足や短納期化だけでなく材料特性によるマシンへの負担や粉塵環境の改善などが課題となっている。2018年12月にはJASSによる建築工事標準仕様が改訂され、レーザによる穴開けが可能になったことに加え、2021年4月にはプラズマ切断などで発生する金属粉塵が法規制の対象となり、構機・鋼材業界ではファイバーレーザマシンによる中厚板大板材の切断加工に大きな期待が寄せられている。今回、リリースした「LC-VALSTER-AJシリーズ」は、フルパーテーションや新集塵システムを搭載することで、切断時に発生する有害物質を外部に飛散させず、加工現場の環境面や安全性を飛躍的に向上させている。
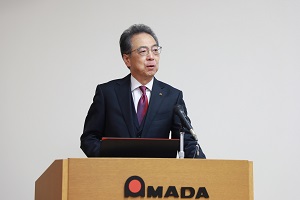
会見の冒頭で、磯部 任アマダ社長が、「グループ会社のアマダマシナリーが担う鉄骨・FAB業界にもともとアマダの商品であったレーザを投入できる運びになった。レーザビジネスを支えているのがファイバーレーザであり、第三世代、第四世代と進化してきた。出力も大出力になり、新たな市場がみえている。これはアマダとしても非常に期待をする心意気も含んでいる」と述べ、「受注は半年で過去最高の数字を出した」と好調な受注環境と、今回の新製品投入が幅広い業界のニーズに応えるものとして期待を滲ませた。
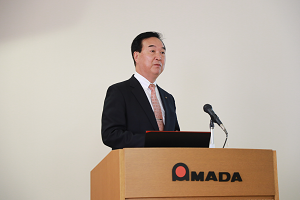
アマダマシナリーが市場に見合った新たなレーザ商品ラインナップで市場に貢献するとした理由に、ファイバーレーザによる技術革新が挙げられた。アマダマシナリーの田所社長は、「従来はプラズママシンで切断していた板厚の領域も、ファイバーレーザマシンによって加工範囲が拡大している。また、2018年、法規制の改訂によりレーザ加工での穴開けが可能になり、本年4月からは法規制の強化によってプラズマ溶断が制約対象になった」ことを説明した。また、レーザ切断のほか、中・厚板市場向けに、曲げ、穴あけ、開先加工、溶接などの二次提案の可能性を示唆した。今後は、鋼材・鉄骨市場に向け、レーザマシンの拡販に注力し、顧客のニーズに応えることでアマダブランドのシェア拡大を図っていく方針。
「LC-VALSTER-AJシリーズ」のココが凄い!
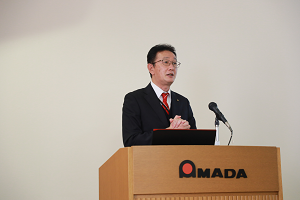
中厚板大板材の高速ピアス加工と高品位切断加工を実現するファイバーレーザマシン「LC-VALSTER-AJシリーズ」は、加工サイズ3.0×1.5×および6.2m×2.5m、発信器出力3kW、6kW、10kWをラインナップ。アマダの山梨貴昭常務は、このマシンのコンセプトについて、(1)鋼材業の中厚板加工をレーザ加工へ、(2)高生産性を実現する機能と自動化周辺装置の拡充(3)作業者に配慮した機械設計、の3つを挙げた。
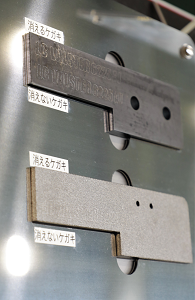
また生産能力についても、プラズマ、自走式ファイバーレーザと「LC-VALSTER-AJ」を板厚別(6.0mm~25.0mm)で製品300個を加工して比較した場合、12.0mmではLC-VALSTER-AJシリーズが2倍の生産能力があることを示した。これは、アマダが保有する加工技術・フライングオプティクス技術による生産能力の向上によるもので、この技術により、工程統合による省人化、消耗品のコスト低減による加工コストの削減に貢献する。
具体的には、プラズマ加工機では①外径加工→②穴開け加工の2工程作業が必要でもLC-VALSTER-AJシリーズでは、穴・外径ともに1台の加工で済む。また長尺製品を加工した場合、LC-VALSTER-AJシリーズは歪量が93%も減少し、ひずみを抑えた高品位加工が実現する。さらに、プラズマに比べて熱影響が少なく、さん巾を挟めるうえ、アマダ独自の加工技術により安定加工が可能になり、歩留まりの高い自由な配置が実現する。
〈主な特長〉
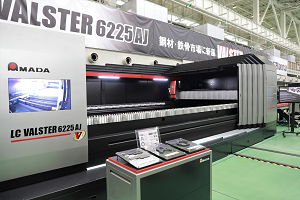
(1)中厚板大板切断用大型ファイバーレーザマシンによる高速・高品位加工を実現
10kWの高出力発信器と「モードコンバーター」を組み合わせることで、高速ピアス加工と高品位加工を併せて実現する。発信器の高出力化に伴い、アマダグループは中厚板加工向け長焦点レンズ用の加工ヘッドを新たに開発している。また、大板材のパレット上でも、機敏に軸移動が行えるフライングオプティクス方式(光走査式)を採用することで加工時間を短縮し、生産性の向上を実現する。
(2)自動化ソリューションで長時間連続運転を実現
材料搬出は自由度の高いレーザパレットトランスファー(パレット自動交換装置)の他に、オートストレージシステム(材料棚)などを組み合わせることで、レーザ加工を止めることなく次の材料の搬入から搬出までを長時間自動運転を行う。ノズルチェンジャーを標準装備することで、段取り時間を大幅に削減。さらに加工中でも素材段取りや印字・マーキングを自動化するなど、様々な加工ソリューションの組み合わせが可能。
(3)フルパーテーションによる作業環境の改善、安全性の向上を実現
材料の搬入を行うパレットに、ロバストデザインを採用することで、粉塵の飛散を防止すると共に、エリア分割集塵により集塵効率を最大化。騒音低減にも効果があり、クリーンな作業環境を確保する。また、自動印字・マーキングは人為的なミスの軽減だけでなく、作業者の安全性を飛躍的に高めることができる。
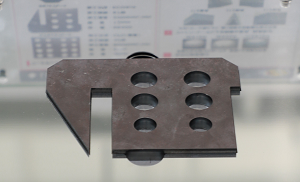
(4)止めない加工支援と最先端のインテリジェント機能
最新のNC装置「AMNC 3i Plus」を搭載し、さらなる安定加工を追求するための最先端の支援機能「レーザ・インテグレーションシステム」により止めない加工を支援する。工数がかかる始業前点検の自動化や加工不良による自動復旧を実現し、ダウンタイムゼロを目指す。これにより生産性が大幅に向上し、作業練度によるバラツキを提言する。また、アマダのIoT「V-factory」により、加工マシンの稼働・保守の状態をリアルタイムに見える化し、顧客のマシンとアマダをつなぐことでマシンの稼働率向上をサポートでき、工場における課題の顕在化にもつながり、経営に役立つ。