アマダ DXを活用した製造改革により生産能力を増強
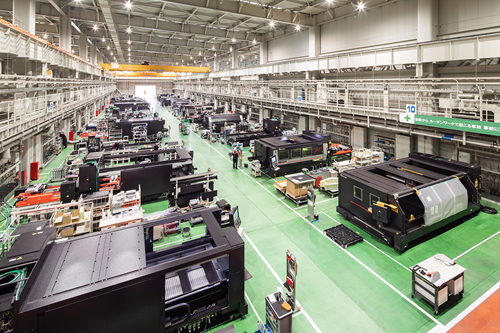
アマダ(社長=山梨貴昭氏)は、このほど、DXを活用した生産方式の改革、間接業務の効率化などにより、板金商品の生産能力を増強したと発表した。
近年、製造業では少子高齢化に伴う労働人口の減少による人手不足が深刻化しているうえ、地政学的なリスクの拡大による一部の部材供給の不足感、短納期化に伴う生産効率への要求の高まりを受け、主力工場の富士宮事業所では、2020年4月に基幹モジュールの生産能力を増強するため、「モジュール工場」を建設。国内外の製造拠点に基幹モジュールを供給してきた。さらに、制御盤や大型部品の組み立てを行う「アマダサテライトパーク」を近郊に建設。これまで分散していたサプライヤーを同パークに集約し連携することで、生産および物流の効率化と生産コストの低減を進めてきた。
従来からの取り組みにくわえて、今回のDXを活用した製造改革により、さらなる生産性の向上、工場全体の効率化、サプライヤーとの連携強化が可能となった。これにより主力ファイバーレーザマシンの生産能力は従来と比較し約30%増強、受注から納入までのリードタイムは20%短縮される見込み。
生産方式の改革
アマダの生産方式は、ブース内で組み立てを行う「屋台ブース生産方式」を基本としている。集中配管が施され、治工具が配置された屋台ブースはその一つひとつがミニファクトリーになっており、組み立てに必要な部品類はキットの形でJIT供給されブース内に配膳される。
屋台ブース生産方式では、組み立て、調整、出荷準備の各チームが順番でブースに入り、10~20日程度のリードタイムでマシンを組み立て出荷する、ブースチーム方式を採用している。この方式は作業習熟度のバラツキをチームとしてカバーし、多能工化が進めやすいメリットがある。一方で、近年マシンの多機能化がより一層進み、仕様、リードタイムの異なる機種の混流生産により、手待ちが発生しやすいという課題があった。また、チームの編成、ブースの割り当てにも多くの管理工数を要していた。
そこで新たな生産方式として、ブースライン方式を主力ファイバーレーザマシンの生産に採用した。これは組立工程を平準化することで工程を1日単位に細分化し、各工程を専門の作業者に任せる生産方式。標準化された作業工程を繰り返すことで、作業習熟度が向上しやすいため、リードタイムが約20%短縮された。
一方で、組み立てに専門的なスキルを多く要する商品や、ブースライン方式の生産計画を超えた商品は、従来のブースチーム方式を併用して生産しているため、フレキシブルな生産体制を維持している。さらに配膳量が多い工程が隣接しないようにブースを割付けることで、配膳エリアを共有し、ブース面積を縮小した。これにより、ファイバーレーザマシンのブース数を1.2倍に増やすことが可能となり、面積生産性は約30%向上した。
間接業務の効率化
アマダは独自の統合生産情報システムとして「AM-HIT’s」を構築してきた。生産座席表を基軸とするこのシステムは、工場の生産能力枠が座席として示されており、受注のあったマシンが登録されシリアルナンバーで管理される。生産座席表から日々の組立日程、加工日程が自動生成され、生産管理システムの「ATS」は生成された日程に基づき、MRPによる生産計画の立案、BOMを参照し部品手配表の作成、発注、在庫管理を行う。
近年、顧客ニーズの高度化により、商品仕様の多様化が進展、生産管理ではマシンの仕様情報や生産計画の確認、修正に多くの管理工数を要していた。調達においても、サプライヤーへの手配情報の修正や納期確認など、双方に大きな負担が生じていた。製造現場でも製造進捗、帳票類の管理が煩雑化していた。
新たな生産管理システム「APEX(AMADA Production Environment Transformation)」は従来のシステムを進化させ、高い生産負荷や多様化する仕様による間接業務の増大に対し、DXを活用することで大幅な効率化を実現した。さらにエンジニアリングチェーンの再構築に向けて、設計BOMに製造BOM、サービスBOMを連携した「統合BOM」を新たに構築した。これにより同一プラットフォームによる技術情報の一元管理と見える化が可能となった。
生産管理では設計情報に基づいた確実な製造手配が可能になった。顧客の要求仕様である確定仕様書の情報から設計仕様情報を経由し、マシンの生産準備に必要な手配情報が生産座席表に自動登録される。さらに実際に製造で使用したシリアルごとのBOMから、顧客のマシンごとに保守用の3Dパーツリストを自動生成することも可能となり、直販・直サービスの同社ならではのSCM、ECMのさらなる連携強化を実現した。
調達においてはサプライヤーとの連携を強化するため、「アマダサプライヤーポータルサイト」を新たに構築した。アマダの生産管理システムから生産計画や発注情報、在庫情報などを、リアルタイムでサプライヤーに共有することができる。さらに技術情報、品質情報、価格情報といった重要な情報も、より一層セキュアな環境での共有が可能となる。サプライヤーが導入している同社製の生産管理ソフトや製造DXソリューションとの連携も予定しており、双方向で生産計画や進捗状況をリアルタイムに共有することで、大幅な間接業務の効率化を見込んでいる。
製造現場ではRFIDタグと組み合わせた電子ペーパーにより、フレームや基幹モジュールなどの内作加工品は、素材の受入れからマシンとして組み立て、出荷されるまで一貫して、所在地、着完情報をリアルタイムに管理している。さらに、マシンのシリアルごとに販売情報、製造情報、品質情報を集約した「シリアルポータル」を構築した。現場作業者はタブレットからアクセスすることで、リアルタイムな生産仕様情報の確認と、管理部門への製造、品質情報の共有が可能となった。
同社では中期経営計画2025における長期成長戦略に向けた活動として、グローバル製造改革による海外への供給体制の強化と、日本、欧州、北米の製造拠点の強化を進めている。
今後も継続的なDXの推進と国内外の工場への水平展開を予定しており、長期ビジョン2030の達成に向け、盤石な製造体制の構築とサプライチェーンのさらなる連携の強化を進めるとともに、人と環境にやさしい次世代のモノづくりを目指していく方針。