大澤科学技術振興財団が「平成24年度助成費贈呈式」を開く 助成課題①(研究開発助成)
大澤科学技術振興財団(理事長=大澤輝秀オーエスジー会長)が、9月28日オーエスジー グローバルテクノロジーセンター(愛知県豊川市一宮町)で、「平成24年度助成費贈呈式」を開いた。大澤科学技術振興財団は、平成3年7月18日に設立され、日本のものづくりを支える科学技術の振興に寄与したいという趣旨のもと、国内の大学や研究所等、非営利の研究機関に所属する研究者にその研究に対する助成を行うとして設立されたものである。
ここに、2012年(平成24)年度、助成課題の詳細を一挙紹介する。
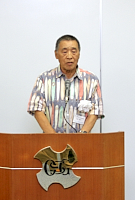
本年度は、13件の研究開発助成および11件の国際交流助成を行い、助成金の合計は2,131万円となった。なお、設立以来22年間の助成金の累計は4億8237万9千円。
贈呈式の中で、大澤理事長は、「新素材の分野も発展してきたが、それに伴い新しい切削工具も必要になりNC機も発展してきた。開発抜きで世界では戦えません。様々な研究課題を成功させていただきたい」と述べ、日本の最先端技術を求めている世界中の顧客にオーエスジーの工具で貢献したいとした。
1.ハイブリッド組織型Mo酸窒化物を利用した耐摩擦・耐摩耗性硬質コーティングに関する研究
・須藤祐司 東北大学・大学院 准教授
TiNは硬く、密着性に優れ、また良好な耐酸化性を有するため切削工具や摺動部品の汎用被覆材として幅広く利用されている。近年、更なる切削加工の短縮化および工具の長寿命化が求められており、コーティングの更新来夏、高機能化が要求されている。それ故、第三元素添加による諸特性の改善が国内外含め多数研究されており、TiAlNやTiSiN等が開発されている。TiAlNは耐酸化性に極めて優れ、また、TiSiNは、Si3N4アモルファス+TiN結晶のナノコンポジット組織を呈するため、50GPa超える超高硬度を示す。しかし、それらTi系窒化膜の摩耗係数は高く(0.6~0.8)、耐摩耗特性に劣るという共通の欠点を持っている。
これまでTiNの摩擦係数低減を目指し、Ti-Mo-Nの硬さ、摩擦、摩擦特性に及ぼす組成や結晶組織の影響を調査してきた。その中で、窒素濃度を制御することにより潤滑性に優れるMo酸化物粒子が摩耗酸化により形成され、耐摩耗性が著しく改善されることを突き止めた。さらに、Mo酸化物形成機構や摩耗メカニズムを明らかにするため、Mo-O-N膜について研究を行ったところ、Mo-O-N三元系において、窒素および酸素濃度を適切に制御することにより、アモルファス酸化物相中に結晶酸化物相が分散した二相組織が得られることを見出した。このことは、Mo系酸窒化物において、潤滑相である「アモルファス酸化物相」と硬化相である「結晶窒化物相」の二相ハイブリッド組織を用いた新規低摩擦・耐摩耗コーティングの創製が期待できることを示唆する。本研究では、Moターゲットを用いた窒素ガスおよび酸素ガス反応性スパッタにより、①Arガス/窒素ガス/酸素ガス分圧比、②基板温度、③成膜圧力を制御し、種々のMo-O-N膜を作成する。それら膜の結晶組織および硬さや摩耗特性などの諸特性を評価し、高硬度かつ優れた耐摩耗性を得るための最適なハイブリッド組織を見極める。また、それら知見を基に、ハイブリッド組織コーティングの摩耗メカニズムを明らかにする。
2.超音波加振電極によるPCDの放電加工特性向上に関する研究
・二ノ宮 新一 日本工業大学・工学部 准教授
多結晶ダイヤモンド焼結対(PCD)は、硬質でありながら欠けにくい特徴を有しているため、切削工具等に多様されている。一方、PCD素材自身の加工は極めて困難であり、研削や放電加工時に多くの問題点を抱えている。特に放電成形では焼結助剤であるコバルト等への放電発生により加工が進行するものの、原料ダイヤモンド粒子が非伝導性のため、加工能率は著しく低くなり、加工不能になる場合も多い。PCDの放電加工を安定して行うため、電極極性を「-」としてオンタイムを極めて短くする(te≦1µs)方法や、電極の極性を交互に正逆反転させる方法などが他者より提案されているが、加工能率は依然として低く、電極消耗も著しいのが現状である。
上記PCDに対する放電加工の問題点を解決する新しい方策として、本研究では、電極を超音波振動させる方法に着目した。簡易的な超音波発振器を用いて予備実験を行ったところ、超音波加振銅電極により、加工能率の大幅な向上と、電極消耗率の大幅な低減の可能性が示唆された。また、3種の振動モード(縦、たわみ、複合)で超音波振動させ得る特殊超音波型みがき装置を利用することで、放電特性に対する振動モードの影響を調べることができる。実際に、電極を3種の振動モードで超音波振動できることを確認した。申請する研究では、原料ダイヤモンド粒径の異なる(φ2µm~φ25µm)各種PCDに対して、電極を超音波振動させることによる放電加工特性向上効果を明らかにするとともに、その加工機構を明確にする。さらに、電極消耗率が極めて小さくなることを利用して、微細加工陽PCD製工具(ドリル・エンドミル)のフルート部や刃先部に微細で精密な形状加工を付与することを目的とする。
3.高機能インプラントの創製を目的とした炭素ドープチタン合金の層選択型超精密加工
・杉田 直彦 東京大学・大学院 准教授
近年、軽量・高強度・耐食性・生体適合性を活かして、チタン合金が人工関節に応用されている。しかし、人工関節摺動面に関しては、摩耗粉が発生すると骨融解を誘発してしまうことから耐摩耗性、生体適合性が要求される。そのために、摺動部品に多く用いられているCoCr合金がしようされているが、アレルギーを持つ患者が存在するために摺動面のチタン合金への代替化が期待されている。炭素ドープ酸化チタンと呼ばれる表面改質により、耐摩耗性を向上させたチタン合金も開発され、摺動面への適用が期待されるが、その表面改質層は非常に薄く摺動面に必要な鏡面の達成と表面改質層の維持の両立ができていないのが現状である。
炭素ドープ酸化チタンの組織断面構造をSEM観察した結果、表面改質層は4層存在することが分かっている。3層目には空洞が生じており、表面粗さを向上させるためには、この層を除去する必要がある。4層目は、空洞がないが2µmほどの厚さしかない。これらの観察結果から、空洞のない2層目(Al2O3)および4層目(TiO2)で鏡面を達成できれば目的を達成できる。したがって、このような層を選択的に取り出す加工を行う必要があり、鏡面の達成と層の識別が求められる。そこで、申請者らは、炭素ドープ酸化チタン処理を施したチタン合金の人工関節摺動面への適用を目的とし、熱処理時に生成される複層膜のうち、目的の膜表面のみを選択的に取り出して鏡面に仕上げる超精密加工方法を研究する。層の識別において、TiO2、Al2O3は絶縁性を持つが母材のTi6Al4Vは伝導性を持つことから、各層は伝導性が異なる可能性があり、下降中に導電性を計測しながら、層の識別を行う方法が考えられる。層の認識を行うための物理パラメータとしては、硬度やインピーダンスが考えられる。まずは、インピーダンスを対象として層の識別手法を提案する。この方法では、電流が層を突き抜ける場合と層表面を流れる場合に分け、層厚さにより、抵抗が変化する並列回路を考える。流れる総電流を計算し、そこから合成抵抗値を算出することで各層の抵抗値を算出する。
4.自己き裂治癒能力の応用によるセラミック工具の信頼性向上に向けた基礎研究
・高橋 宏治 横浜国立大学・大学院 教授
セラミックスは、耐摩耗性および耐熱性に優れ、化学的に安定であるため、切削工具等の加工用耐摩耗部材として利用拡大が期待されている。これらの工具は、製品の製造工程の高速化、高能率化の必要性から、高不可下での長寿命化が求められている。しかし、セラミックスは破壊靱性値が金属に比べ低いため、使用中にき裂が発生した場合には、信頼性が大幅に低下する恐れがある。当研究質では、各種セラミックスに、炭化ケイ素(SiC)の微粒子等を複合することにより、自己き裂治癒能力と機械的特性が優れた材料の開発に成功した。き裂治癒はSiCの高温酸化で生成するSiO2が、き裂面間を強固に接合することにより生じる。さらに、ショットピーニングと自己き裂治癒を併用した新しい高強度化手法を提案した。これらの結果を活用して、セラミック工具の信頼性向上と長寿命化を達成したいと考えている。切削工具において重要な機械的特性として、破壊靱性値、接触強度、耐摩耗特性や耐熱性が挙げられる。しかし、これらの機械的性質に対するショットピーニングおよび自己き裂治癒の硬化は十分に解明されていない。そこで本研究では、申請者らが開発した自己き裂治癒能力を有するセラミックスの破壊靱性値、接触強度、耐摩耗性や高温での曲げ強度に対するショットピーニングおよび自己き裂治癒の効果を解明することを目的とする。まず、自己き裂治癒能力が優れた各種セラミックスを焼結する。続いて、機械的性質評価用の試験片を作製し、種々の条件でき裂治癒およびショットピーニングを実施する。その後、破壊靱性値、残留応力、硬さ、接触および転動疲労強度、高温曲げ強度等を測定する。これらの結果をもとに、最適なショットピーニングおよび自己き裂治癒の条件を明らかにする。
5.高トルク・軽量なマグネシウム合金ねじを製造する ねじり調整転造プロセスの開発
・古井 光明 富山大学・工学部 准教授
工業的に実用化されているシンプルな塑性加工のひとつにねじり加工がある。ねじり加工は被加工材のねじり中心から表面に向けて、導入されるせん断ひずみの量が増加する原理的な特徴がある。このねじり加工をねじ転造の前工程に組み込み、転造に先立って丸棒素材にねじり加工を施すと、多量のせん断ひずみの導入に伴い丸棒表面部の結晶が局部的に微細化、方位ランダム化を生じる。最密六方格子構造に起因して加工性に乏しいマグネシウムは本質的に結晶粒径依存性が高い材料であり、結晶粒を微細化することによって粒界すべりが活発化し、加工性が著しく改善される。また、結晶方位のランダム化は非底面すべりの活動を促進し、延性を高める。すなわち、ねじり調製による微細・ランダム結晶組織の形成にともなう加工性の向上によって、ねじ転造の低温・高速化や加工度の増加をはじめとする転造性の改善が図れる。また、本助成研究に先立って行った予備実験において、室温でわずか270°ねじったAZ31Bマグネシウム合金では、ねじり調製なしの場合に比べて、2倍以上のねじりトルクを有することを明らかにしている。ねじり調製は、マグネシウムの加工性向上のみならず、強度やねじりトルクを高めることが分かってきた。
以上のような知見をベースとして考案されたのが本助成研究である。本助成研究では、ねじ転造の低温化をもたらす微細・ランダムなミクロ組織を形成するための最適ななじり調製の条件を導出すると共に、良好な形材特性を有するねじを製造するためのねじ転造の条件を設定する。ねじり加工条件の設定では、試料の表層部に多量のひずみ蓄積をもたらし、結晶微細化・ランダム化に大きく影響するねじり加工のパラメーターの中で最も重要な加工速度および回転角度を変化させ、AZ31BおよびAZ91Dマグネシウム合金丸棒に対してパラメーターを組み合わせたねじり加工を実施し、最適なねじり加工条件を決定する。続いて、転造ねじの機械的特性や表面状態に大きく影響する転造加工のパラメーターの中で最も重要なダイスの回転速度、ダイスの押付圧力および加工モードを変化させ、ねじり加工によって微細・ランダム結晶組織を呈した2種類の供試材に対して、パラメーターの組み合わせによる温室転造加工を実施する。その後、種々の条件でねじり調製転造したマグネシウム合金ねじのミクロ組織を光学顕微鏡、走査型電子顕微鏡/EBSPおよび透過型電子顕微鏡を用いて観察する。これらにより、微細なミクロ組織を有する形材が得られ、しかも室温での加工が可能な臨界の転造条件を確率する。なお、最適な条件の下でねじり調製転造したマグネシウム合金ねじの微細組織や形材特性は、平成25年度に評価する予定である。これら2年間の系統的な研究により、ねじり調製の結晶微細化・ランダム化を応用したマグネシウム合金ねじの室温転造加工技術を確立する。併せて、ねじり調製をコアとする新しい塑性加工プロセスの研究を通して、生産性向上・省エネルギーをもたらすハイパフォーマンスな素形材製造プロセスの設計開発と共に、微細結晶粒から成り良好な機械的性質を有する素形材のメゾスコピック組織制御技術が確立できることを確信している。
6.水ガイドレーザによるCVDダイヤモンド被覆工具の表面仕上げ
・岩井 学 富山県立大学・工学部 講師
Ⅰ.研究目的
難削材として知られる高シリコンアルミニウム合金や炭素繊維複合材(CFRP)の加工にはPCD工具やCVDダイヤモンド被覆工具が使用されている。特にCFRPの加工においてはバリ(炭素繊維による毛羽立ち)発生やデラミネーションが問題となるため、切刃寿命は当然として複雑な切刃形状が要求される。ダイヤモンド被覆工具は超硬合金製工具素材の表面にダイヤモンドをCVD法により被覆するため、複雑な工具形状に対応しやすい特徴を持っている。現在、市販されているCVDダイヤモンド被覆工具の表面粗さは最高品質のものでRz=1~2µmと言われているが、加工面品位を向上させるにはダイヤモンド被覆の表面粗さをより向上させる必要がある。本研究では数10mmに及び同一のビーム形状やエネルギー密度を持ち、照射面に発生する熱を瞬間的に除去できる特徴を有する水ガイドレーザを用いてCVDダイヤモンド膜の結晶凸部のみを選択的に除去し、結果として面性状を向上させることを目的としている。また、当該手法を用いて複雑形状を有するCVDダイヤモンド被覆切削工具(ドリル、エンドミル)等に適用し、より優れた切削特性を示す工具とすることにある。
Ⅱ.研究内容
水ガイドレーザの照射条件とCVDダイヤモンド膜の表面粗さ改善効果の関係を調べる。実験には、水ガイドレーザ加工機およびYAGレーザ加工機を用いて行う。ダイヤモンド膜表面の観察はコンフォーカル3次元顕微鏡およびSEMを用い、精密形状測定器により形状精度の評価を行う。具体的には、以下の実験研究を行う。
(1) 加工条件の影響
(a) 照射角度の影響、(b)レーザ出力、(c)掃引速度、(d)掃引回数、(e)被加工材初期面粗さ
(2) 複雑形状への適用
(a) エンドミル等の複雑曲面への適用、(b)実加工における当該工具の加工性能の調査
(3) 表面粗さ改善機構の解明
加工機構を既存のレーザとの比較や有限要素熱解析で明らかにする。
(4) 結果まとめ
7.超難加工性硬脆材の電界・スラリー流れ場制御型高能率研磨加工技術の開発
・畝田 道雄 金沢工業大学・工学部 准教授
近年における低消費電力化や環境指向の高まりを背景に、LED、半導体レーザ、パワーデバイス用材料として、サファイヤ、炭化珪素、窒化ガリウムの適用が検討されている。一般的に、これら材料には高い平坦性が求められることから、製造プロセスには「研磨加工」が用いられている。しかしながら、これらは非常に高い硬脆性、並びに高い化学的安定性という「超難加工特性」を有し、研磨加工におけるスループット低さ(低加工レートに起因する加工プロセスの長時間化)が問題視されている。
ところで、研磨加工は工作物と定盤相互間に専用研磨液(以下、スラリー)を介在させ、工作物と定盤を相対運動させることで工作物を平坦化する方式であり、スラリーの流れ場は研磨加工特性に大きな影響を及ぼすことが指摘されている。一方、加工条件は経験則によって決められているのみであり、加工レート向上によるプロセス時間の短縮を図るためには、加工現象を定量的に評価した上で、新たな研磨加工技術を設計することが重要である。このような現状にあり、スラリーの流れ場を評価することの重要性は国内外を問わず世界的に認識され、実験的にスラリー流れ場を観察し定性的に評価される諸研究や、熱流体解析的に同流れ場を定量的に評価される諸研究が見受けられる。しかしながら、それに基づく研磨加工特性と各種条件の関係解明には至っていない。本研究では、申請者が提案するスラリー流れ場の定量評価法に基づき、それによる超難加工材料の各種条件下における研磨加工特性との相関関係を明らかにするとともに、超難加工性硬脆材料の研磨特性に関する体系化を図る。さらに、その結果に基づいて電界を研磨部位に印加することによるスラリー流れ場のコントロールと最適化を実現し、新しい「電界・スラリー流れ場制御型高能率研磨加工技術」の開発研究を実施する。
8.CFRP(炭素繊維強化樹脂)積層体の高精度・長寿命スパイラル穴あけ加工装置の開発
・柳下 福蔵 沼津工業高等専門学校 学校長
CFRP(炭素繊維強化樹脂)積層体が燃費向上のため航空機機体や輸送用機器の構造材料として使用されるようになったが、航空機の機体組み立てには極めて多数の締結用穴あけ加工に多額の経費と時間を要しているのが現状である。特にCFRP積層体と機体骨組み材TiAl6V4合金の重ね板の穴あけ加工に対しては現状のドリル加工に変わる高精度・長寿命の穴あけ加工技術が切望されている。本研究の目的は、二重偏心機構により一つの駆動源の回転運動から超硬エンドミルに時計回り高速時点と反時計回りに低速公転を可能とし、断続切削により(超硬エンドミル径+2×(偏心量))の直径の穴あけ加工用の実用機を開発することである。当研究室ではこれまでに、二重偏心機構により設計製造したエアーモータ駆動のスパイラル穴あけ加工装置を使用して、ダイヤモンドコーテッド超硬エンドミルによるCFRP積層体とTiAl6V4合金の重ね板をドライで穴あけ加工試験を実施し、以下の結果を明らかにしている。
(1) 航空機メーカが用中するCFRP積層体とTiAl6V4合金の穴加工精度および工具寿命の目的値をほぼ満たしている。
(2) 断続切削のため発熱が少なく、TiAl6V4合金の穴出口のバリが微小である。
(3) CFRP積層体とTiAl6V4合金の切りくずがすべてエアーで吸引回収できる、環境対応の穴あけ加工技術である。
本装置の実用化を考えると、現状のエアーモータ駆動スパイラル穴あけ加工装置は重量が17kgfであり、現場作業者の作業性・安全性を満たす12kgf以下への軽量化が必須の課題であることが明確となった。そこで駆動源を電動モータに変える等の設計改善を適用して、航空機機体組み立て現場で実用可能な電動モータ駆動スパイラル穴あけ加工装置を設計製造して性能評価試験を行う。
9.ブラスト研磨処理を用いた超硬合金基材の研磨機構に関する研究
・福本 昌宏 豊橋技術科学大学・工学部 教授
近年、切削工具には、形状以外の付加価値として長寿命性や低切削抵抗性などが求められており、その実現に表面改質技術の導入が検討されている。その代表が、簡便さを特徴とするブラスト研磨処理である。ただし本処理法は、簡便さとは裏腹に処理機構が十分に解明されておらず、処理条件の最適化も未だ経験則の域を出ない。本研究は、ブラスト研磨法における特殊粉体の砥射による超硬材料研磨機構を解明し、制御性を確立した同法を用い、市販研磨材では未だ困難とされる工具形状極細部への本件間処理法適用の実現を目的とする。加工対象を工具用超硬合金とし、ブラスト研磨処理に影響を及ぼす主因子として、研磨材の大きさ、核体密度、粘度、研磨材砥射速度、砥射角度、砥射密度を採り上げ、これら因子と得られる超硬材表面粗さとの関係の系統把握を通し、本法研磨処理における支配因子を特定するとともに、プロセス因子の適正な組み合わせを可能とするデータベースを整える。また、超高速ビデオを駆使し、加工物表面への研磨材衝突状態のその場観察および加工物同一箇所に注目した研磨加工状態経時変化の断続観察により、本法による超硬材料表面研磨機構の実像を明らかにする。以上により得られた知見を基に、従来ブラスト研磨法では困難とされる超硬工具極細部への研磨処理を可能とする新たな手法を探求する。特に、通常市販されるブラスト研磨材・核体の平均サイズは0.5~2.0mmであり、この粒径が構内部等への研磨加工の下限を与えている。粒径における制限は、本研磨加工を成立させる最低限の研磨材質量を補償する上で決定されるものと推定されるが、本研究では上述の研磨機構に関する基礎的知見を基に、核体材質の選定により極微細な研磨加工を実現可能な新規研磨材を新たに設計・提案し、他のプロセス因子との組み合わせにおける最適条件の下に、実プロセスとして採用し得る極細部研磨加工技術の確立を目指す。
10.成形・せん断・大工園地を1ショットかした超高強度鋼部品のスマートホットスタンピングの開発
・森 謙一郎 豊橋技術科学大学・工学部 教授
自動車の軽量化と衝突安全性向上を目的として、引張強さが1GPaを越える超高張力鋼板の適応が望まれているが、成形荷重やスプリングバックの増大、成形性や金型寿命の低下によって1.2GPa以上の鋼板の冷間プレス成形は困難であるとされている。そこで、鋼板を加熱して成形を行うホットスタンピングが注目されており、低い成形荷重、スプリングバック防止、高い成形性、ダイクエンチによる成形品の高強度化(1.5GPa級)などの利点がある。しかしながら、自動車ボディ骨格材に限定された適用範囲、後加工レーザ切断、低い生産性、高温炉を用いた大型設備などの問題点があり、ホットスタンピングはまだ多く使用されていない。複雑形状部品が板鍛造で成形されているが、板材を厚さ方向に圧縮するため摩擦の拘束が大きくなって荷重が増加し、変形抵抗が小さいアルミ合金、低炭素鋼板しか加工されていない。このため、強度が必要な部品には成形後浸炭、窒化焼入れが必要になり、工程数も多い。
本研究では、ホットスタンピングと板鍛造の問題点を改善するために、急速通電加熱と成形・せん断・焼入れの1ショット化を用いた超高張力鋼部品のスマートホットスタンピングを開発する。通電加熱によって、鋼板を焼入れ可能な900°に数秒で加熱し、加熱効率を高めて酸化スケールの発生を防止し、サイクルタイムを短縮して設備もコンパクトにする。板材では温度が急速に低下するため、成形・せん断・焼入れを1ショット化して焼入れ直前までの温度低下を防止し、通電加熱が適応できる矩形板材が使用できるようにする。1ショット中にせん断加工を含み、プレスの下死点保持によってダイクエンチをして焼入れを行い、後工程であるレーザ切断と焼入れ工程を省略し、製造コストを大幅に低減する。加熱によって延性が向上して切口面がほとんどせん断面になり、下死点保持によってスプリングバック、焼入れひずみを防止し、遅れ破壊を生じる引張残留応力をなくし、高品質な部品を成形する。
11.プラズマ援用研磨によるワイドギャップ半導体基板および単結晶切削工具のナノ精度表面仕上げ
・山村 和也 大阪大学・大学院 准教授
高精度ガラスモールド用の超硬金型材料、シリコンカーバイドに代表される次世代パワーデバイス用高硬度ワイドギャップ半導体基板材料、あるいは超精密加工陽のダイヤモンド、単結晶シリコンカーバイド工具は、高硬度かつ化学的に不活性なため、既存の加工技術では加工能率が低い。工具損耗が大きい、さらには電子物性や工具寿命に影響を与えるスクラッチ、マイクロクラック、加工変質掃が生成されやすいといった問題点を有する。本研究では、大気圧プラズマの照射による材料表面の軟質化と、軟質砥粒を用いたラッピング・ポリシングを複合させることにより、硬脆難加工材料に対するプラズマ援用研磨(PAP)技術を開発する。これまでの研究では、単結晶4H-SiC(Si面)に対してプラズマ援用研磨を行った結果、ステップ/テラス構造が観察される原子レベルで平滑な表面が得られ、断面TEM観察では格子歪みが全くみられない、結晶学的に完全な表面であることを確認している。PAPプロセスでは、大気圧プラズマの照射による研磨対象材料の表面改質、並びに改質層の除去家庭の理解と高能率化が重要である。本研究では、1)大気圧下において安定なグロー放電プラズマを発生させるため、3次元有限要素電場シミュレーションをもちいて電極構造を最適化する、2)プラズマで生成した活性種と表面改質の相関を、表面組成と改質速度に関してはX線光電子分光(XPS)と断面透過電子顕微鏡(XTEM)により、表面硬度に関してはナノインデンテーションテストにより評価し、最適な改質プロセス条件(ガス種、電力)を探索する、3)原子間力顕微鏡(AFM)と走査型白色顕微干渉計(SWLI)を用いた表面粗さ解析により、改質層の研磨家庭におけるプロセスパラメータ(砥粒材質、粒径、圧力、線速度、運動軌跡)を最適化する、4)XTEMと角度分析XPS(ARXPS)を用いた酸化膜界面の原子構造解析により、ラジカル酸化による原子レベルでの表面平滑化メカニズムの解明とPAPプロセスへのフィードバック、を実施する。
12.CAM-CNC統合によるNC指令方式の改革と工作機械の知能化
・白瀬 敬一 神戸大学・大学院 教授
NC工作機械は機械加工の自動化・高精度化に貢献してきたが、NCプログラムを事前に用意する現行方式は、英文字と数字で指令するGコードやMコードの陳腐化とともに、柔軟な機械加工の実現や工作機械の知能化を阻害している。そこでCAMをCNCに統合して、工程設計、工具経路生成、工具モーション制御の各機能を階層的、分散的に処理する新しいNC指令方式を提案すると共に、それによる工作機械の知能化を実現する。本研究では、申請者が過去に開発した仮想倣い加工の機能に、工程設計の機能や種々の加工シミュレーション結果を参照して加工戦略を決めながら工具モーションを自立的に制御する機能を統合し、既存のNC工作機械では実現できない革新的な知能化の機能を提供することを目的としている。本研究は『NC工作機械はNCプログラムで指令するもの』という常識を打ち破る非常に独創的な研究で、当該分野では類似の研究は見当たらず、世界初の新しい成果が示せると自負している。
本研究の特色・独創的な点は、以下のようにまとめられる。
1. プリプロセスあるいは印プロセスの核シミュレーション結果を参照しながら、工具モーションを自律的に制御するという構想がこれまでになく独創的である。市販のNC工作機械でその効果が実証できればその波及効果は大きい。
2. 自律的な工程設計や作業設計と柔軟な工具モーションの制御により、加工対象のCADデータから人手を介さずに機械加工が実現できる。これにより製造リードタイムは短縮され、生産変動に対する柔軟性が向上するなど、生産システム全体のコスト低減、生産効率改善に貢献できる。
本研究の成果は機械加工の概念を一新し、わが国の工作機械産業の技術力を一層堅固なものにできる。また、単純な機械加工は工作機械任せにして、作業者はより硬度な機械加工に専念できる環境が提供できることから、製造業の競争力のある“モノづくり”に大きく貢献できる。
13.原子スケールで平滑なダイヤモンド表面の創成とそのメカニズムの解明
・久保田 章亀 熊本大学・大学院 准教授
高硬度、高伝導率、絶縁特性、耐環境性に優れた特性を持つダイヤモンドは、次世代エレクトロニクス用基板や切削工具、超硬合金金型の代替型などの様々な分野への応用展開が機体されている。しかしながら、ダイヤモンドは物質中で最高の硬度を有し、かつ化学的に安定で加工が最も難しい材料の一つであり、ダイヤモンドの高能率・高精度加工技術の開発が技術的課題となっている。申請者は、高硬度かつ化学的に安定な難加工材料の加工を実現するために、過酸化水素水溶液中において鉄触媒表面上で生成される化学的に活性なOHラジカル(Hydroxyl radical)を利用した新しい研磨法を提案し、これまでに本手法を用いて、難加工材料であるSiC基板やGaN基板の高精度加工を実現している。現在、基礎実験段階ではあるが、この提案手法を単結晶ダイヤモンドの加工に適用し、加工前後の表面粗さを大幅に改善させることに成功している。本申請研究では、申請者が提案する手法によってダイヤモンド表面の原子レベル平坦化を試み、ウエット環境下でもダイヤモンドを高精度かつ安定的に加工できることを実証するとともに、その加工メカニズムを解明することを目的とし、以下の項目について取り組みたいと考えている。
(1) ダイヤモンドの安定加工の実現とその除去メカニズムの解明
ダイヤモンド基盤全面を安定に超平滑化・平坦化できるように試作した加工装置を改良する。そのうえで、加工前後の表面の化学結合状態や結晶性の評価、加工でしようした鉄定盤表面上の元素分析を行い、溶液中でのダイヤモンド表面除去機構を科学的観点から明らかにする。
(2) 加工特性の評価と有効な固相反応の実験的検討
ダイヤモンド加工における最適加工条件(加重や回転数、溶媒濃度など)の選定や結晶面方位の異なるダイヤモンドの加工実験を通して、提案手法の加工特性を把握する。また、鉄以外の遷移金属とダイヤモンドとの二固体間の化学反応性を調査し、高能率・高精度でダイヤモンドを加工できる可能性について追求する。