技術者に聞く―――経済効果を高める“工具力”はここにあり! 高性能工具でトータルコストの大幅削減に寄与する日立ツール
われわれの生活に溢れるカタチあるもの全てに切削工具は深く関わっている。
最先端の切削を提案し続けている日立ツール(社長=田中啓一氏)の強みといえばユニークな発想と高度な開発技術であろう。ベースの素材から形状、コーティング技術まで切削工具にかかわる全ての技術が一体となり、“価値ある工具づくり”をモットーとしている。
同社が提唱する「加工費半減運動」は、高速加工を可能とする最新工具でユーザーのトータル加工コストを削減するとともに、CO2の発生を削減し、加工現場に高い経済効果を提供しようという願いが込められている。同社では、新製品が売上高の1/3以上を占めており、開発技術にかける情熱が詰まった積極的な商品展開を行っているのも魅力的な特長である。
今回、“開発の日立ツール”の底力である技術者3人に、新製品に対しての思い入れや開発秘話などを取材した。
“アルファ ボールプレシジョンF ABPF形”に“SC,STタイプインサート”が加わり、これで全ての仕上げ加工が可能になった!
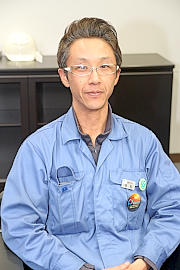
昨年12月に、『アルファ ボールプレシジョンF ABPF形』に『SC,STタイプインサート』を追加し発売した同社。この開発を牽引していたのは、成田工場開発センター長 赤松猛史氏(工学博士)、同主任技師 小林由幸氏、同主任技師 木内康博氏。
「もともと刃先交換式のアルファ ボールプレシジョンF ABPF形は、金型の仕上げ加工用途向けに販売をしていた。このABPF形用インサートとして先般発売した“強ねじれ刃形 ”のSFタイプは、金型の三次元形状部の仕上げ精度の向上と長寿命化が図れると評価も高く、プラ金型用のSCタイプと高硬度材用STタイプのインサートを新たに追加発売するに至った」(赤松氏)とのこと。既に発売済みのSFタイプと合わせると、なんと、“プレス金型”、“プラスチック金型”、“高硬度材分野”の全ての仕上げ加工に対応が可能になる。
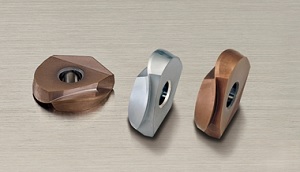
特に今回、形状にこだわったという赤松氏。「従来とは明らかに形状が違います」と話す。
製品をみると、確かに女性らしい丸みを帯びたカタチをしていた。
20年前とは明らかに違う加工ニーズと飛躍的に精度が向上した加工現場
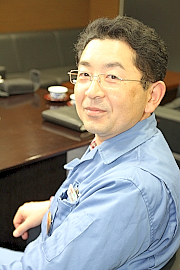
技術者といえども現場の声をリサーチすることは忘れない。この開発部隊は営業担当者になったこともある。当然のごとくユーザーの加工の悩みは製品開発のモトとなるので、徹底的にリサーチした。
「それこそ20年前の加工と今の加工方法はだいぶ変わってきました。当時のインサートは交換式なのでどうしても剛性がいる。だから工具に厚みを持たせなければならず、切れ刃の制限がかなり出てくる。そうすると刃形は当然、剛性重視になっていく。高能率加工が当たり前となった今では、高速機が増加し、精度もすこぶる向上しました。加工現場が要求する精度は20年前と比べ、極端に上がったのです。従来通りの工具では、切削抵抗そのものが高く、途中で叩かれるような振動もおきてくる」(木内氏)
そこで開発部隊は考えた―――。従来のインサートは直線だった。そこを曲線にすれば、ねじれている分、徐々にアタリが変わってくる。切り屑が薄くなって切り屑が流れる方向も変わってくる―――。
場所を移して比較のための加工を行った。
被削材は、S50C(H)―220HB。
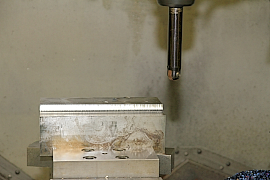
写真にあるワークを比較すると一目瞭然である。従来のものは、直線刃形でありダイレクトに振動があたってびびりが発生している。反対側は新製品を使った面であり、ツルピカである。
剛性重視だと、どうしても振動がおきてしまう。断続加工になると加工そのものが苦しくなってエッジが欠ける。高能率工具を使用する現場の要望に応えるためには最適な形状を考えなければならなかった。工具メーカーとしての意地もある。
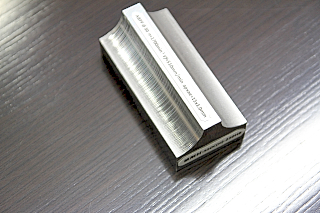
ということで現在、プレシジョンシリーズの最小径はなんと8φ!
S字にすると精度の観点から製造する側も難しいはずだが、その難しさを開発部隊はどのようにして乗り切ったのか。
「従来のプログラムではこのような形状の加工は困難でした。そこでプログラムを自社で開発したのです。インサート用のS字ができるよう自社ソフトをつくりました。例えば最近の研削する機械はほとんどソフトが付いていますが、ほとんどがブラックボックス化されており、あまりいじれない。裏を返せばある意味、優秀な機械を買えば同じようなものがどこの工具メーカーでも出来てしまうのです。ところが自社でソフトをつくればブラックボックス化が解消されるので、自分たちでいろんなことができます。パッとみてどのメーカーがつくったものでも単純に同じような形状の工具に見えるかもしれませんが、実は色々と違うことがたくさんあります。切削工具とは実に奥が深いものです」(赤松氏)
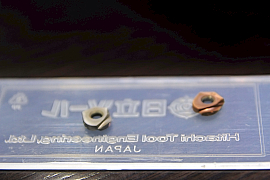
「刃先交換式もどんどん小径化していく」との見解を示す赤松氏。
日立ツールが出した新製品の良さは、ユーザーの都合で選択の幅が広がることだろう。
業界初! 製造現場を驚かせたインサート式ボールエンドミルの4枚刃。
技術者が開発をし続けるということ―――
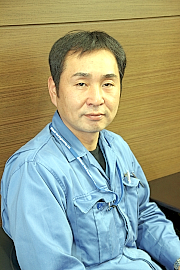
さて、実はこれ以外にも日立ツールには注目の工具がある。
業界初の仕上げ用刃先交換式工具の4枚刃化を実現したこの開発に携わったのが小林氏だった。
最近勢いが良い自動車業界をはじめとした大物金型加工の技術動向は、リードタイムの短縮や高品質化のための磨きレス・砥石レス化を目的とした現行の工作機械による高精度高速切削の取組に関心が高まっている一方、工具費や工具寿命が大きな障壁となり広がりに欠けているのが問題だった。
「このようなユーザー動向を踏まえた結果、独自のインサート固定方法を考案し、インサート式ボールエンドミルの多刃(4枚刃)化が実現しました。CBNインサート工具の領域をカバーする高能率、長寿命、かつ良好な加工面を得るための刃先交換式仕上げ用ボールエンドミルは好評で、われわれも非常に嬉しく思っています」(小林氏)
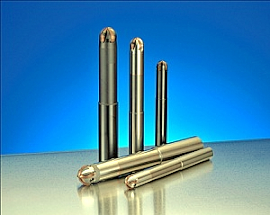
最後に開発センターの責任者である赤松氏は言った。
「われわれは開発技術の日立ツールということを掲げているので新製品をどんどん出し続けていかなければならない使命感がある。でもその中にはニッチな製品もある。売上げにすごく貢献する製品ではないかもしれないけれど、それを必要としているユーザーがいるわけで、このようなニーズに応えるためには、核となる商品で売上げを確保しなければ、ニッチな製品にも力を入れることが難しくなる。お客様の満足する商品がつくれなくなってしまうのはメーカーとして避けなければならない。現場で愛されているロングセラーだからこそ今回、核となるプレシジョンをテコ入れし、さらにパワーアップさせたのは、そんな思い入れがあったからなんですよ」
次はどんな新製品が出てくるか。今年の日立ツールに注目である。