難加工を制するオーエスジー 航空機産業への取り組みとは
最先端技術を活用した製品を提供し、対面型販売組織をグローバルで拡充しているオーエスジー(社長=石川則男氏)は、昨年度、日本の切削工具メーカーとして初めて連結売上高1000億円を達成するという快挙を遂げた。
中でも航空機関連産業が先進国にて活況だったことを受け、航空機関連産業からの旺盛なニーズに対応すべく競争力の高い製品を生み出していることに注目したい。成長分野のひとつである航空機産業への取り組みについて、開発グループ 航空宇宙担当Ph.D 滝川義博 氏、同Aerospaceチームリーダー 辻村桂司 氏にお話しを伺った。
(写真=開発グループ 航空宇宙担当Ph.D 滝川義博 氏)
航空機は難削材の塊
高い寸法精度が要求される航空機―――。
最先端の民間機では徹底して軽量化を追求している。それは機体の薄肉構造にも表れており、強度や剛性も要求されるため、最先端の民間機では重量比50%近くにCFRP(炭素繊維強化プラスチック)が使われている。注目したいのは、材料を結合する部位にはCFRPと親和性の悪い金属が腐食する現象を避けるため、チタン合金を多用している点だ。いわば航空機は加工しづらい難削材の塊といっていい。
航空機の機体はCFRPを使うが、この材料のやっかいなところは、能率を高めるための高速切削は熱を発生させ、材料を構成している樹脂を劣化させる問題や、穴まわりの繊維がほつれるデラミネーションを発生させる点であろう。滝川氏は、「材料の難削性はもちろん、形状からくる難しさもある。航空機の場合、薄くて長くて面的に大きく保持がしにくい。材料からくる工具の摩耗の速さ、形状からくる加工のしにくさ、これらが加工中に振動を起こしたり、工具の寿命を短くする」と話す。
航空機に適用されている異種材組合せの穴開けも難削性を高めている。その理由について、
「困難なのは大きな径の剛性のない薄くて大きいパーツ同士を繋ぐ場合、保持が難しいうえ、切削油が使えない。この表面に化学成分が残っていると、2~30年、飛行機が飛んでいる間に化学変化を起こす可能性があるので、大抵はドライで加工する。もし使ったとしてもミストで、化学的安定性を認定されたものだけを使う。大物はマシニングセンタの上には乗らないので、特殊な機械を使用し、主翼と胴体を付き合わせて穴をあけて組み立てていく。非常に制約が多く、機械のパワーや剛性が乏しい中で位置精度、穴精度、結合精度を確保しなければならない難しさがある」という。
CFRPのメリットは機体軽量化と耐腐食性だが、素材コストが高い、加工性が悪く工具摩耗が激しいなどのデメリットもある。高価な材料を確実な方法で加工しなければならず、精度の高い解析も要求される。昔はCFRPの穴開けというと、1本の工具で10穴ほどしか開かなかったが、現在、オーエスジーのチャンピオンデータでは厚さ6.3mmで6800穴ほどあくという。ここでオーエスジーの開発努力を知ることができる。
昔は困難だったCFRPの穴あけも今ではスピーディかつ品質のよい加工ができるようになった。工具のポイントは、“コーティングと形状”だという。「ダイヤモンドコーティングを最適な厚さで最適な粒度でしっかり付けること。そこに焦点を当てて研究開発をしている」と滝川氏。開発についての思い出を尋ねると、「当初は良いダイヤモンド工具を開発したもののアプリケーションがなかった。マーケットも知れていた。電着工具のほうが安いし、それでいいという風潮もあってダイヤモンドコートは鳴かず飛ばずの状態。稼働率も低くて不人気だった。ところが1990年代、コンポジットを航空機に使い始めてからダイヤモンドコートが注目され、量産されるようになった。ちょうど自衛隊がF-2戦闘機を生産した時代の話です。あの時は全然穴があかなくて、工具メーカー各社を集めて開発が始まった。あの時代はコンポジットに5穴しか開かなかったけれど、昔は5穴でも許されたんですね」と笑った。
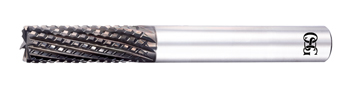
「顧客の要望に沿ったものを経験から想定してテスト加工をする。設備も購入してでもやりますよ。トコトンやるんです」(滝川氏)
材料を制する切削工具の数々――最新高能率マシンに対応する工具の開発に注力
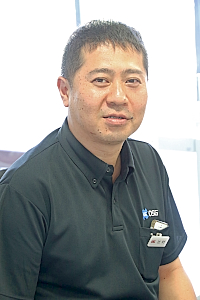
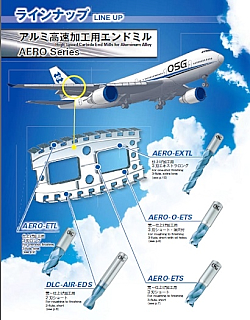
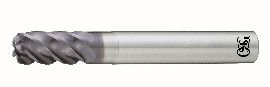

最後に滝川氏は「航空機関系にどっぷり浸かるチャンスに恵まれ、お客様のところへ通い詰めて色々教えていただいた。精一杯集中してやれるのは、オーエスジーに“トコトンやる”という風土・文化が根付いるからだと思っている。工場があり、試作部門があり、営業がある、というバックボーンがある。1人では切り込んでいけないけれど、後ろに支えてくれる組織があるから、迷わずどんなことでもトライできる」と意気込みを示し、しめくくった。
オーエスジーの強みはなんといってもフットワークが軽いこと。
2020年に売上高1500億円を達成するために、世界中に対面型販売組織を拡充し、柔軟に、そして迅速に、ユーザーニーズに対応し変化できる企業を目指すとしている。