「AMADA INNOVATION FAIR2016」をレポート! ~来場者を魅了した新加工技術の数々~
近年、IoTやインダストリー4.0などが出現により、繋がる社会の構築が急務とされ、世界規模でネットワークの高度化が進められている。また、変種変量生産、労働人口の減少などますます顕著になってきており、製造現場においては、より効率的に経済効果を高める努力がされているようだ。そういった時流を背景に、アマダ(社長=磯部 任氏、本社:神奈川県伊勢原市)は、いち早く、工場も事務所もあらゆる作業者が発信する情報を有機的につなげ、経営者、工場長、作業者にとっても価値ある情報がリアルタイムに確かめられる「V-factory」を構築している。
同社は、5月20日から6月25日までの金・土曜日の10日間、本社アマダ・ソリューションセンターで、「V-factory2016新加工技術によるモノづくり革新」をテーマに、グループ各社と共同で業界最大規模のプライベートイベント「AMADA INNOVATION FAIR2016(通称:AIF2016)」にて最新ソリューションと加工技術をテクニカルデータや導入事例を披露した。
「AMADA INNOVATION FAIR2016」をレポートする。
業界に先駆けて「VPSS(バーチャル試作システム)」を推進
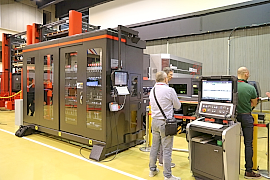
今回の「AIF2016」では、この「V-factory」を単なる情報連携のIoT技術としてだけでなく、さらに進化をさせている。顧客のものづくり改革、QCD(Quality〈品質 〉、Cost〈費用〉、Delivery〈納期〉)の向上を支援する仕組みを、同社が金属加工機械の総合メーカーとして培ってきた全行程での新加工技術・加工ノウハウを中心に提案していた。
製造現場につきものの急な計画変更や工場内トラブルに対しても迅速に対応し、高品質、低コストな製品を確実な納期で取引先に出荷することができれば、仕事の信頼性も増すだろう。まさに鬼に金棒、製造現場に「V-factory」なのだ。
この「V-factory」は、顧客とアマダも繋がっている。新しいサービスメニューや計画的なメンテナンスを実現するとともに、価値ある情報を発信、提案を行うというビジネスモデルでもある。狙いは工場経営の効率化を実行していくこと。ここで培った仕組みとソリューションは継続的に顧客に提供するという。なお、本年12月には「V-factory」のコンセプトモデル工場が、本社ソリューションセンター内にオープンする予定。進化し続けるアマダの技術に期待したい。
さて、「AIF」はこれまでアマダグループが毎年開催している最重要イベントでもある。筆者が訪れた日も、国内外から多くの来場者が見えた。「AIF」では、1日に4回、ツアーが開始され、しっかり見学することができた。
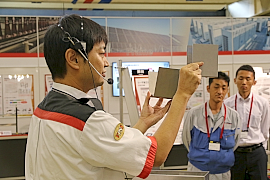
業種別では、配線板BOX、建材、機械カバー、厨房、精密医療、架台――の6つの業種、30のアッセンブリーを展示しており非常に分かりやすいアプローチだった。なお、この新加工技術全体での提案は、業種別と工程別の両面から、今回は約70種類のサンプル製品を展示している。展示サンプルは2パターンあり、ひとつは“加工技術提案サンプル”で、加工課題を加工技術で提案するというもの。もうひとつは“モノづくり提案サンプル”で、提案形状は同じでも、作り方を変えて提案するというユニークなものだった。それぞれの加工技術のポイントや機能、効果といったテクニカルデータを、100種類以上のパネルを使用して丁寧に解説していたのが印象的だった。
新加工技術で効率的かつ間違いのないモノづくりへ!
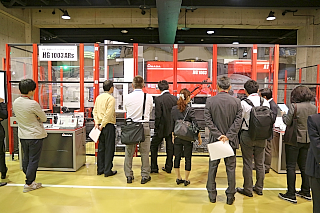
複合機によるパンチ・成形・レーザ高効率加工についても、外周切断後の成形加工では、成形分が変形してしまう、パンチ・成形・レーザを別工程で行っているため工数がかかるといった課題があったが、これについても、成形加工後にレーザ加工を行うことで変形を防止する新加工技術の提案があった。複合機一台に工程を集約することで工数を大幅に軽減できるメリットがある。
レーザ切断後の曲げ反りには思わず頭を抱える方々も多いと聞いた。そうした製造現場の悩みを払拭すべく、曲げ反り改善システムの提案もあった。通常、“反り修整”は、経験や技術が必要であり、精度や品質に不安が残るというやっかいなものである。同社が提案している新加工技術のポイントを挙げると、①反り演算ソフト、②荷重制御、③反りの発生要因になっている残留応力を減らす“反り制御ダイホルダー”にあった。
顧客の工場の“スマートファクトリー化”を進める工程改革ソリューションもさらに進化していた。加工技術や加工ノウハウは、「VPSS」を進化させた新しい板金エンジニアリングシステム「VPSS 3i」に組み込まれた。“職人ワザ”をデジタル化することで、高能率に安定した品質を生み出す。従来は各工程で発見された不具合は、再プログラミングが必要だったが、「VPSS 3i」では製品の完成形から製造工程を遡って可視化することで、手戻りなく加工することができるメリットがある。進化を遂げた「VPSS 3i」は、ブランクから曲げ、溶接まで全行程を通じたものづくりを支援する新しいエンジニアリングシステムなのだ。
変種変量生産でもQCD改善へ!
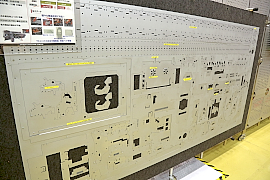
その中で、ファイバーレーザ複合マシンとテイクアウトローダー(TK)でリードタイム短縮を実現させる、という取り組みがあった。少々分かりづらいが、写真にあるワークサンプルは、材質:SECC、板厚:1.0mm、加工速度:F30000、加工時間:39分47秒、板取り数:25種40製品。使用した加工マシンはファイバーレーザ複合マシン「ACIES AJ」だ。この導入効果だが、従来の「ACIES」と比較してみると、従来は加工時間が45分2秒だったものが、「ACIES AJ」は39分47秒で12%も短縮している。ランニングコストに至っては、従来は2652円だったものが、なんと29%のコストダウンに成功。1769円となっていた。
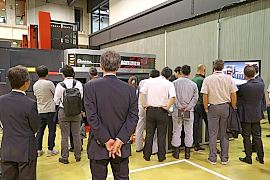
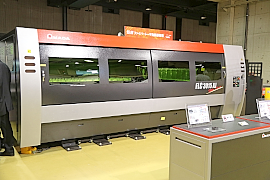
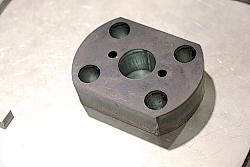