【技術】ケナメタルとユーザーの挑戦! ~ソリッドセラミックエンドミル 航空宇宙関連の注文製作工場において納期対応を可能に~
ケナメタルは、マテリアルサイエンス、工具ソリューション、耐磨耗ソリューションを通じ、航空宇宙、土木、エネルギー、ジェネラルエンジニアリング、および輸送の分野にわたる顧客に愛されているが、このほどソリッドセラミックエンドミルが航空宇宙関連の納期対応を可能にした。冒頭の写真にあるセラミックエンドミルは、手で触れるとプラスチックのように感じるかもしれないが、ニッケル基合金の切削では超硬工具の20倍の性能を発揮するという。
今回、この工具にまつわるケナメタルと顧客の挑戦を掲載する。
扉を開く
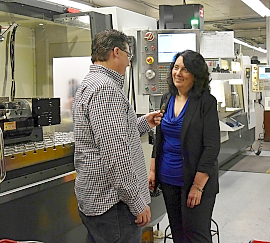
自身で事業を立ち上げる機会に出会ったのは、40年前Mike Vucish Sr.氏が海軍の核構成部品の製造元で働いていたときだった。備品を購入し、夜間に教鞭をとっていた技術学校から数名の生徒を招き入れ、1978年にStellar Precisionを設立した。Vucish氏は、自身が立ち上げたばかりの会社がしっかりと根付くまでの間、日中の仕事を続けていたが、その間、家族も仕事を助けていた。
「当社は地域の他の大型注文製作工場からあふれた大量の仕事を引き受けることから始まったのですが、父が核開発分野の経験者であったため、数の核開発プログラムを直接支援するようになっていきました」と話すのは、Stellar Precisionの現オーナー兼社長である娘のLori Albright氏。以来、同社は、Boeing社、Lockheed社、Raytheon社など、多くの主要な航空宇宙産業と防衛産業の請負業者、さらにはさまざまな原子力関連と医療関連の顧客の主要サプライヤーとして成長し、従業員は70名を超え、1,000万米ドル近い売上高を上げるまでになっている。
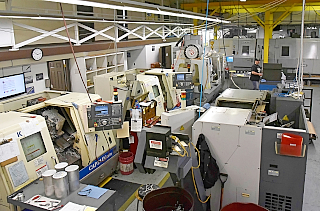
主要な機器の中には、オークマ製の36インチ径の部品を最大120インチ長(91 mm × 305 cm)に加工可能なLB-45旋盤、Haas製のX軸移動量10フィート(305 cm)とテーブル耐荷重4000 lb(1814 kg)のVF-11 5軸マシニングセンターがある。またStellarは、ワイヤ放電加工機数台、12または3・4・5軸マシニングセンターとミルターン旋盤も備え、非破壊試験、溶接、熱処理、テフロン加工などの付加価値サービスを提供している。
強靱すぎない
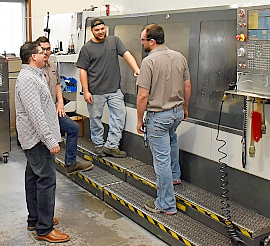
Frieze氏によれば、Stellarは少量のインコネル625試作品の受注を得たばかりだった。原材料ブランクの加工は、18平方インチ × 3インチ厚(457 × 457 × 76 mm)で、重さそれぞれ約300 lb(134 kg)。プロジェクトチームは、高靱性の被削材の被削性向上にも問題なく対応した。Stellarでは、インコネルおよびその他のニッケル基超合金、タングステン、マルエージング鋼、RC 60 4340(300M)、工具鋼の加工を日常的に行っていた。
公差も問題ではなかった。Frieze氏は、長さ12インチ(304 mm)に対して0.005インチ(0.127 mm)の輪郭度公差を求めた最近よくあるチタン製部品を挙げた。これは、加工前の状態で1個あたり5,000ドル以上する部品の「数十分の1」を保持することに相当する。インコネル部品の比較的柔軟な公差を満たすことは問題ではなかった。
課題だったのは、ある基材の除去。仕上り状態のインコネルプレートは薄型で重さ30 lb(13.6 kg)となり、最初の重さから90%の軽量だ。納期に間に合わなかったとしても、現状の超硬工具でそれだけの被削材を除去するには時間がないことがわかっていたので、何か他の解決策が必要だと考えていた。
その年の初め、Frieze氏と同僚数名は全米機器・機械協会(NTMA)の地方支部による主催で、ラトローブ近郊にあるケナメタルのテクニカルセンターで開催された研修イベントに参加した。Frieze氏は、そこで製品マネージャーのMatthieu Guillon氏と出会い、切削工具の紹介を受けたが、Frieze氏は当初懐疑的だった。「まるでプラスチックのおもちゃのエンドミルのように見え、触った感じもそのようでした」と、笑う。
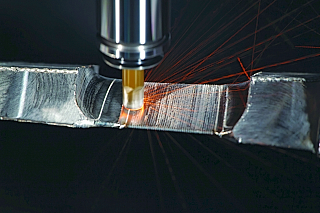
Stellarでは、すぐにはセラミック工具を使用しなかったが、送り量と速度の簡易な計算後、適切なアプリケーションであれば効果的なソリューションとなるとFrieze氏は見込んでいた。数カ月後、そのアプリケーションがインコネルプレートと共に到着した。Frieze氏はGuillon氏に電話をし、以前彼らの話題にしていたセラミックカッターをうまく利用できるかもしれないと伝え、どれくらいの時間で入手可能か問い合わせをした。
課題を解決
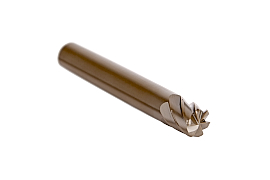
「結果が予測できなかったので、試験材のブロックで試してみたのです」とFrieze氏は言う。「セラミックでは切削液は使いません。使うのはエアブラストだけです。注文製作工場の全員が機械の周りに集まって、『おい、見ろよ!』と言うのです。火花があちこちに飛んでいましたよ。あんな光景を見たのは初めてでした。でも、始まって1時間のうちに、これならいけると確信できたのです」。
「工具は安くはなかったですよ」とFrieze氏。「一時、Lori氏のオフィスには約20,000ドル分の価値のあるエンドミルがあって、この投資が正解だったのか疑問に思い始めていたのです。でも、機械コストとサイクルタイムの短縮を算出すると、この方法で3、4倍コスト効率が向上することが分かりました。磨耗の有無にかかわらず30分ごとに交換することで、エンドミル1個あたり30分の加工時間となったのです。この工程は予測が簡単で、完全自動での作業が可能でした。本当に劇的な削減でした」。
Stellarが何よりも喜んだことは、廃棄品を出さずに部品を予定どおりに納品し、現在ではさらに二度目の大量受注を見積もっているということだ。オーナーのLori Albright氏は、成果に高い満足を示した。「今回のような状況は、当社のビジネスでよくあることです。お客様のニーズに応え、必要な最高の技術を確保しなくてはなりません。それが、当社がケナメタルとの関係を大切にしている理由の1つです。ひとつのチームとなって、課題を解決していくのです」と大喜びした。
すでにStellarの既存の設備を6倍に拡大したAlbright氏だが、今や近隣にビルを新築しようかと考えているとのことだ。また、機械加工の取引にもっと多くの若い人材を投入する予定でもある。「当社は地域の複数の学校と師弟プログラムを締結しており、その1つが父の教えた学校なのです」と、Albright氏。
「若手の人材が当社のイノベーションをたびたび牽引していることに気付きました。旧来の方法で作業を続けたり、工具や設備の投資を怠ったり、新技術を求めないということは非常に簡単なことです。大量生産、24時間体制でフェンダークリップを製造する時代は終わり、企業が今後成功し成長していくには、継続的に製造工程を向上させていくしかありません。当社にとって、ケナメタルはその成功の一部なのです」。