最先端をゆく! これがマザックの「Mazak iSMART Factory」の全容だ!
ヤマザキマザック(社長=山崎智久氏、本社:愛知県大口町)が、最新のIoT・自動化技術を活用して本社工場である大口製作所をスマート・ファクトリー化し、このほど「Mazak iSMART Factory(マザック・アイスマート・ファクトリー)」として稼動を開始、5月8日に記者団に工場を公開した。
同社は、1980年代よりフレキシブル生産システムを応用した無人化工場に取り組み、1998年にはITを活用して工場内をネットワークするcyber Factory(サイバー・ファクトリー)」を完成させるなど、いち早く工場の自動化・ネットワーク化を推進しているが、このMazak iSMART Factoryは、従来のcyber Factoryのコンセプトをさらに昇華させたもの。最新のIoT技術を活用して工場内の全ての生産活動をデジタルデータ化し、可視化・分析による改善や基幹システムとのデータ連携、AI技術の応用などによって、生産の自律的な最適化を行う“高度なデジタル製造の実現”を目指している。
大注目の「Mazak iSMART Factory」の全容と最先端の大口工場をレポートする。
世界の製造業に貢献していくことを目指して
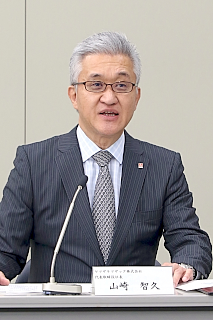
山崎社長は、「ケンタッキー工場は、 iSMART Factory化のプロトタイプ工場としてリニューアルを行った。本社大口工場のiSMART Factory化は、ケンタッキー工場で得たノウハウをベースにさらに高度な数々のテクノロジーを工場全体に融合して作り上げた現時点で最も進化した iSMART Factoryとなっている」と話す。
同社は、創業以来、自社製の工作機械やシステムを実際に自社の生産設備で使用して検証することで顧客に安心して製品やシステムを購入してもらう、という経営方針に基づいて、自動化とネットワーク化による自社工場内での高効率生産の実現を推進してきた。
1980年代では、多品種少量生産に対応したFMSシステムを世界に先駆けて開発し、また1990年代後半にはIoTの先駆けとなるcyber Factoryを開発して、社内に導入した。このように同社ではその時代の先端技術を取り入れて、社内設備の検証を行いながら、オリジナリティ溢れる信頼性の高い製品やシステムを世に送り出してきたのだ。
また、今回の取り組みでは、もともと米国で考案され、現在グローバル規模で採用が拡大している工作機械用オープン通信規格の“MTコネクト”を同社が他社に先駆けて採用したこともひとつの契機となっている。このMTコネクトは、自社製品だけでなく、他メーカーの機械でも製品の新旧を問わずに工場内にある全ての設備機器の稼働データを収集して監視や分析を行うことで工場全体の効率的な運営を実現することを目的として開発されているものだ。
同社ではMTコネクトの全面採用に加えて、iSMART Factoryの実現のために必要なサイバーセキュリティの強化とビッグデータの解析とデータ処理能力の向上を目指して、ネットワーク機器最大手のシスコシステムズと“MAZAK SMART BOX(マザック スマートボックス)”を既に開発済みである。
また、同社の製造ノウハウを見込んで開発した稼動監視分析用ソフトウェアである「SMOOTH MONITOR(スムース モニター)Ax」と組み合わせて国内外10箇所の生産拠点で、MTコネクトやSMART BOXを導入し、生産性のさらなる向上のための取り組みを現在進めている。
山崎社長は、「自社の生産設備で蓄積された機能やノウハウを今後“iSMART Factory ソリューション”として製品化やサービス化を測りながら、お客様に販売・提供することで、工場設備全体の効率的な運営に一層貢献したい」との考えを示し、公開した本社大口工場においては、「こうした取り組みに加え、英国工場で先行導入したERPシステムを生産実行システムや最新の自動化システムと接続して、あらゆる生産活動のデジタルデータ化を現在推進しており、クラウドサービスやAI技術等の導入をすでに開始している」と述べた。
このような取り組みを通じて、同工場では、製造リードタイムの3割削減や、仕掛在庫の3割削減、管理コストの5割削減としたiSMART Factory化の数値目標の実現を目指している。
「今後は、“常に進化しつづける工場”をスローガンとして、iSMART Factoryのコンセプトが世界の製造業に貢献していくことを目指している」(山崎社長)
全社的な改革プロジェクト
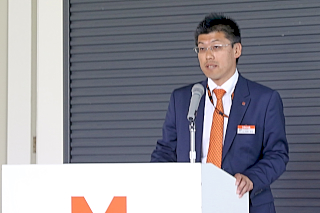
「弊社は“工場はショールーム”という理念のもと1919年の創業以来自社製品を自社生産設備で活用し、その効果を実証することで、お客様に安心して私どもの製品を導入していただくことを経営方針としてきた。90年代後半に実現したcyber Factoryは、当時広く普及し始めたWindows95のパソコンを搭載した自社CNC装置、MAZATROL FUSUON640を前面的に採用し、工場内のデジタルデータ化を一気に推進した」(堀部部長)
同社では、多関節ロボットをはじめとした自動化システムの開発、さらにはインテリジェント化の取り組みなど、今日のMazak iSMART Factoryにつながるコンセプトをいち早く実現しており、この構想は国内外10箇所の生産拠点に水平展開されている。同社の生産拠点は、日本国内で大口製作所、岐阜県美濃加茂市にある美濃加茂製作所、第2製作所、オプトニクス、三重県桑名市にある精工製作所の5つの拠点を構えている。海外では、1974年に開設した米国ケンタッキー工場を皮切りに、1987年に英国工場、1992年にシンガポール工場、2000年には中国・寧夏に、2013年に中国遼寧工場を立ち上げ、現地のニーズにタイムリーに応える生産拠点を展開している。
5phaseで構成 大口製作所は現在3.5phase
さて、堀部部長の説明によると、Mazak iSMART Factoryは5つのphase(段階の意味)で構成されている。
第1phaseは、IoTサイバーセキュリティ対応による接続・可視化。これは、ネットワーク機器最大手シスコシステムズ社と開発したSMART BOXを導入することで実現した。これによってメーカーやモデルの新旧を問わず、センサー情報を含めた工場全体の設備機器の情報を一元的に取得することが可能になり、突然の設備異常や不具合に素早く対処するなど、生産性の維持、向上が実現した。
第2phaseは、製造ビッグデータの分析・生産改善の段階。MTコネクトで得られたデータをビッグデータ化し、工作物の精度結果や品質データ、設備機器の保全データ等とつき合わせて分析することで様々な生産性改善のヒントや製品にフィードバックするノウハウが生まれている。ちなみに、iSMART Factoryのプロトタイプといわれる米国ケンタッキー工場は、この第2phaseにあるとのこと。さらに iSMART Factory化で得られた生産関連の知見をMTコネクト対応の稼動監視、分析ソフトウェア SMOOTH MONITOR Axとして開発、これら商品をiSMART Factory内で導入し、運用することで、さらに新しい知見やノウハウを生みだし、iSMART Factory内で顧客に商品、サービスとして提供するとしている。
第3phaseは、様々なシステムの連携を深め、さらに高度な分析を行うことで、各工程や工場全体の最適化を図る段階。大口製作所では、同社英国工場で先行導入した新しいERP基幹システムを導入、生産実行システムや最新の自動化物流システムと接続して高度に連携させながら、多品種少量でも効率良く生産できる、マスカスタマイゼーションの実現に向けて取り組んでいる。
第4phaseは、熟練工のノウハウをAI化、システム連携の高度化を図る段階。大口製作所では、機械加工の切削条件をAI技術とビックデータで最適化する取り組みをすでに始めており、デジタル・ツインと呼ばれるシミュレーションによる最適化や、さまざまなサービスを提供するプラットフォームとしての位置付けもある。Mazak SMART Cloudの導入検証なども行っており、堀部部長は大口製作所の位置付けを「現時点で、3.5phaseにある」と話した。
第5phaseは、つねに進化し続ける技術や目まぐるしくかわる国際情勢やグローバル市場を反映し、自立的に進化し続ける工場としてのiSMART Factoryの近未来ビジョン。
「今後の技術進化によって、第6フェーズや第7フェーズといった新しい取り組みをし続ける必要があると考えている」(堀部部長)
さて、大口製作所におけるシステム連携や製造ビッグセータの活用でどんなメリットがあるのか気になるところだろう。具体的には、iSMART Factoryで製造される製品群は、製品ライフサイクル・マネジメントの考えのもとに、その製造はサプライチェーン・マネジメントによって、受注から組立、出荷、検収までの全ての企業活動をデジタルデータ化し、3DCADデータやPDM、ERPやMES 、CRM等のものとの高度な連携を図る。これは製造ビッグデータを形成することにつながる。こうした流れで、システム連携による最適化、仕掛在庫や管理工数の削減、製造リードタイムの短縮といったものを達成する仕組みである。これらの知見を製品やサービスにフィードバックすることで、開発リードタイムも短縮できるといった様々な効果を生むことが期待できるのだ。
工場見学はアトラクション感が楽しめる! まさに工場はショールーム!
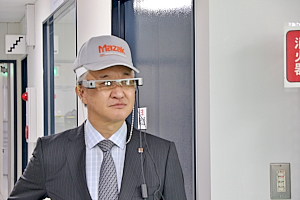
このグラスをかければ、加工動画や説明資料が目の前に表示される。現実は、デモ加工が見えづらい場合もあるが、これをかければ、普段は見えにくいところもよく分かり、さらに理解を深めることができる。また、グラスをかけることによって、アトラクション感も楽しめた。こうしたものに慣れていない筆者は「おお~すごい!」と思わず声を上げ、宙に向かって妙な動きをしてしまったほどだ。
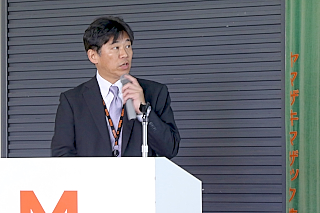
まずは機械加工部門(自動化)を見学。全ての加工機はネットワークに接続され、稼動状態を監視、および稼動データの収集をしている。8台のSMART BOXで接続されている加工設備や周辺装置は、他社製の加工機も含んでいる。それ以外にも周辺装置の自動搬送台車、切粉集中搬送システム、自動倉庫、これらをMTコネクトのデータを通してSMART BOXを介してデータの収集をしていた。
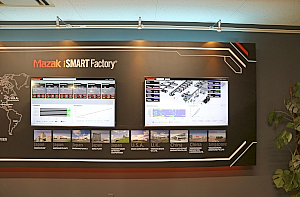
稼動状態が見られるモニターがあった。直近24時間の稼働状況が見られるようになっている。累積運転時間/目標時間の比較画面もあった。あらゆる設備装置の稼働データを収集しているが、このデータは1,230万件/日という膨大なデータを現在、分析・改善している。切削時間・非切削(エアーカット)時間など自動運転時間を細分化して分析、アラーム発生周期などを分析して発生要因を特定してダウンタイムを削減し、稼働率アップを図るのが狙い。この取り組みにより一例だが、アラーム発生による停止時間が37%も減少したとのこと。
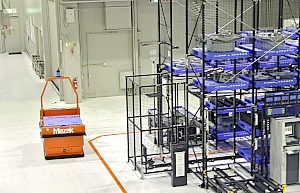
同社では、AI(機械学習)による切削条件の最適化に取り組んでいる。Mazak Smooth CNCを搭載した工作機械では、切削条件の可変機能(VFC)と振動センサ等を用いて最適化した切削条件をデータベースに蓄積し、他の機械や新しい加工プログラムに反映することで、生産性の向上に役立てている。
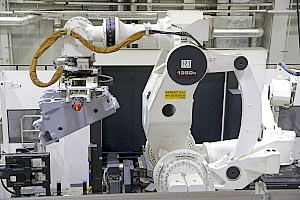
続いては板金加工工程を見学。
一元管理するQRコードと耐熱タグだが、自社性のレーザー加工機でQRコードを印字する。QRコードで読み取ることによって、プログラムや図面を自動ダウンロードすることができるのだ。これは、図面やワーク探しの時間の削減にも繋がる。この取り組みで、人為的ミスをなくし、稼働率を上げて生産性を30%も向上したという。
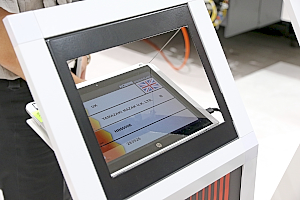
械加工工程の最適化、設備の補修タイミングを最適化するなど、AI技術のひとつである機械学習機能の導入、検証を開始するところで、第4phaseの完成ももう近い――。
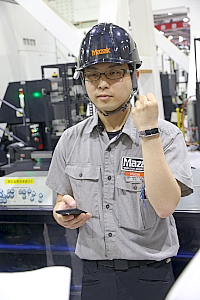
同社では、昨年より販売を開始している安全・確実に工場内をネットワーク化するMAZAK SMART BOXや、可視化ソフトウェアSmooth Monitor、先日発表した複合加工機の自動化システムと自動倉庫システムを融合したMAZATEC SMSなど、新たな製品やサービスソリューションを自社で実証し、顧客へ提供していく。