DMG MORIが高性能主軸MASTERシリーズを搭載した「NTX2000/2500/3000 2nd Generation」の販売を開始
DMG MORI(社長=森 雅彦氏)が、このほど複合加工機NTXシリーズの第二世代モデルとなる「NTX2000/2500/3000 2nd Generation」の3機種の販売を開始した。
このマシンは、1,000台以上の納入実績を持つ第一世代のNTXシリーズを深化させ、さらにバリエーションを増やした複合加工機。航空機、医療機器、金型など形状が複雑化するワークの同時⒌軸加工にも対応する。タービング用の高性能主軸turnMASTERと全長わずか350mmの工具主軸compactMASTERを搭載し、圧倒的な切削能力を実現しているのが特長だ。従来機に対して顧客からの要望が多くあった機械停止の大きな要因のひとつである切りくず対策には、様々な実験や分析を繰り返し、革新的な切りくず処理を実現している。
産業のトレンドをキャッチ! 加工現場の“生声”を惜しみなく反映
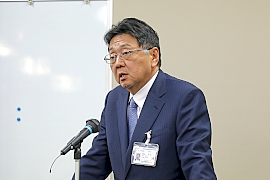
この機械は本年4月より販売を開始するが、この34の意見や要望についてはほとんど取り上げて反映しているという髙山専務。「お客様に届ける時点から高い完成度の機械を届けられると考えている」と自信を見せる。
同社のNTシリーズは2005年からスタートしているが、それまで複合加工機ミルターンは旋盤ベースの機械にミーリングの主軸を付けた機械だった。「その時、お客様からミーリングでも重切削がバリバリ削れる機械が欲しいという話があって、機械の構造を旋盤ベースから徹底的に見直し、切りくずが多く出ても処理できるように加工室のカバーを縦面にしました。2005年からのコンセプトは踏襲しています。さらに今回、1番強調したいのは、compactMASTERという主軸を開発したこと。今までと同じスペースですが、少しでも大きなワークを加工できるところが1番のセールスポイントです。スニークプレビューのときに、改善すべき点や要望等の一方で、どういった点が良かったかをリサーチしたところ、8割以上のお客様が“加工空間が大きくなった”と喜ばれています。」と、ユーザーの声をこと細かく拾い上げ、満を持してつくり上げたマシンであることを強調した。
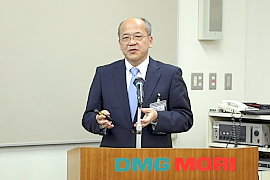
「NTX2000/2500/3000 2nd Generation」の開発を担当した酒井茂次執行役員 開発本部ターニングセンタ開発部部長(以下酒井部長)は、最近の動向について、「特に航空・宇宙、医療機器、電機機械器具、精密機械器具・光学機器は需要が増加するとみています。」と話す。今回はこうした時流を背景に、製品力のアップを図ったとのことだ。
「NTX2000/2500/3000 2nd Generation」の特長
高性能主軸/刃物台
●3年保証のMASTERシリーズ主軸を搭載
〈ターニング用高性能主軸turnMASTER〉
・ベアリングのボール大径化と部品精度の向上により、耐久性を強化
・マグネスケール製の高精度回転センサを搭載し、高精度加工を実現
・NTX2000 2ndGeneration 標準仕様:最大トルク421N・m(従来機比83%アップ)主軸最高回転速度5,000min-1
・NTX2500 2ndGeneration 標準仕様:最大トルク599N・m、主軸最高回転速度4,000min-1
・NTX3000 2ndGeneration 標準仕様:最大トルク1,194N・m、主軸最高回転数3,000min-1
複合加工機史上最小の工具主軸compactMASTER
・標準仕様:最大トルク132N・m、主軸最高回転速度12,000min-1
・モータの回転力を直接伝達するダイレクト・ドライブ・スピンドル(DDS)を採用し、切削能力を向上させるとともに、メンテナンス頻度や故障リスクを低減
・複合加工機史上最小(同社が発売した複合加工機に限る)となる全長350mmのコンパクト構造により、90°回転しても第2刃物台との干渉領域が小さく、第1、第2両主軸での加工が可能なため、加工能率が大幅に向上
・X軸ストロークの拡大により、主軸中心からマイナス125mmまで直線軸移動での加工可能
酒井部長は、「従来だと複合加工機の工具主軸は全長が500mmありましたが、今回は350mmと大幅に小さくなりました。これにより端面加工では中のスペースを有効に活用できるうえ、中で旋回したときの干渉が非常に小さくなりました。」と、優位性についてコメントした。
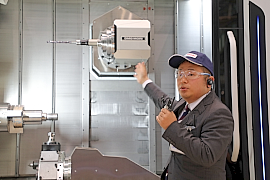
熱源である主軸などのモータや、ボールねじなどの工藤部に冷却水を循環させる同社独自技術「機体冷却水循環」により、熱変異を抑止、回転軸のB/C軸にマグネスケール製ロータリースケールを標準装備している。
今回、実機を見ながら説明してくれたプロジェクトリーダーでもある栗谷龍彦部長(開発本部 複合加工機開発部:以下栗谷部長)は、「複合機にはじめてのY軸を搭載したことでミーリングの活躍する場が増えました。サイクルタイム短縮にもなります。こだわりのマガジンも注目して欲しいポイントです。作業者は日常的に工具交換や工具の確認をされます。夜、暗くてもツールが見えるようにとマガジンの中を明るくしました。」とマシンを指した。
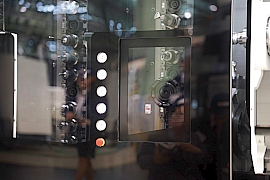
さて、機械停止の大きな要因のひとつである悩ましい切りくずには冒頭にも書いたとおり、革新的な切りくず処理を実現している。具体的には、従来機より処理能力を向上させたドラムフィルタを搭載したオプションの機外チップコンベヤにより、効率的な切りくず処理と高精度なクーラントろ過を実現。切りくず流しクーラントを標準装備し、主軸直下の切りくず排出性が向上している。切りくず除去、加工点の冷却、工具寿命の延長に工過程名切りくず処理機能を装備しているのも優位性のひとつだ。ユーザー視点でつくりあげたマシンだからこそ、製造現場にもたらすメリットは大きい。