「製造現場の自動化・省人化に貢献」 ~ブルーム-ノボテスト 山田社長に聞く~
1秒に幾千もの測定値を取得できるLC50-DIGILOG技術のココが凄い!
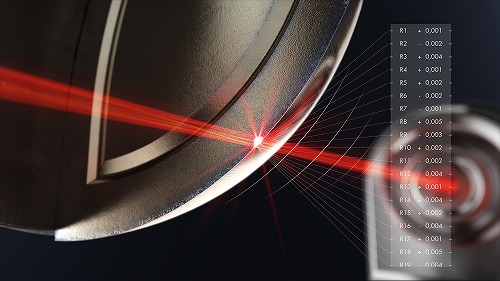
ブルーム-ノボテストが提供する〝DIGILOG技術〟や工具測定システムを用いれば、1秒に幾千もの測定値を取得でき、データストリーム評価により今までになかった高速かつ信頼性を備えたアプリケーションの活用ができると評判だが、最近、この技術に目から鱗的な新発見があり、現在、製造現場を沸かせている。この件について技術・サービス部の中本裕司部長は、「従来は光を遮った、遮らないという状態で、機械の座標の位置を数値で出してきましたが、弊社の『LC50-DIGILOG』は、アナログ的な信号をデジタル化することによってアナログに近い信号を全て解析し、見える化することができます。この技術は周波数解析を応用していますが、従来のレーザー測定技術だと、主軸の振動周波数は分かりませんでした。」と話す。
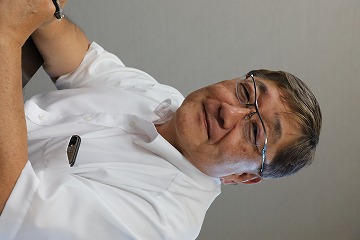
従来分からなかった、〝主軸の振動周波数と振れ〟が見える化できるメリットは、例えば同じ加工でも、使用した機械によっては結果が違ってくるということも目で見て分かるということにもなる。加工には、様々な機械的な要素があるが、〝気になる部分〟が正確に推測できるという点に、『LC50-DIGILOG』が持つポテンシャルの高さに同社の技術部隊も驚いたという。
「従来は、工具の状態ばかり見ていたのですが、実は機械の状態まで知ることができるのです。例えば、ベアリングがあって球がたくさん並んでいます。中のリテーナー、外輪、内輪のところに、もしキズでも入っていたとすると、コトコトと振動が起こります。それが回転数や球の数に合わせて計算すると、周波数が出てきますが、これが見えるようになったことにより、『LC50-DIGILOG』のポテンシャルが一気に上がりました。」(中本部長)
高価なワークと工具を台無しにしないために
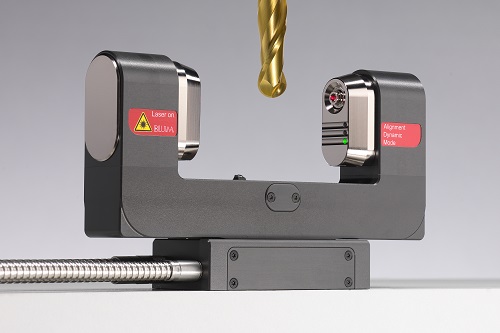
高級機の主軸といえば、〝安定〟していることを思い浮かべるが、それでも特異な振動が出た場合、原因はなんだろう? と現場は考えるだろう。ホルダーはHSKやBTと形が違うものがある。となると、その特異な振動について、例えばこの2つのホルダーの一方が正常値を示しているのにもう一方が異常値を示した場合、ホルダーの主軸が高級機だとすると、まず、主軸に問題があるということは考えにくいことから、中本部長は、「振動の周波数を見える化することで、ホルダーにアンバランスがあるのではないかと、すぐに気付きます。アンバランスがあると、主軸の持っている回転数と影響し合って〝ピーク〟が出てくる。回転しているときの変位まで分かるのです。主軸が回っているときにバランスが悪いと触れが出ます。状態が良ければ中心がピシッと合ってクルクル回るのですが、バランスが崩れてくると、ある周波数では別の動きをし出すので、これらが見える技術があると、加工において信頼性が増します。通常のデジタルでは信号のオンオフしか見えないのですが、『LC50-DIGILOG』は、その中間の動きが見える。これを分析することによって周波数が分かるのです。」と説明をしてくれた。周波数分析は周波数と振動から変位量をみつけることができれば、速度も加速度も分かるので、ソフト的にも計算ができるようになり、さらなる予防保全に役立つわけなのだ。なかなか奥が深い―――。
高価な材料を、慎重に安価な機械でゆっくり加工するのもアリだが、厳しいご時世に加工費をいかに下げ、利益を確保するか、となると工程短縮、高速加工は必須である。それには、加工における様々なリスク管理が必要だ。例えば工具が破損し、ワークに食い込んでしまうと、残念ながらそれはゴミになってしまう。今まで費やした加工の工数や材料費を考慮すると、ワーク1つがボツになるのは、ものすごく損害が大きく、もし、このような原因により、加工を失敗したならば、そのショックは大きく、膝から崩れ落ちる方もいるだろう。作業者の心理的不安を取り除く意味においても、今の時代に合致した新たな加工システムの必要性は高い。
現在、同社の『LC50-DIGILOG』では、正確な測定が実行され、且つ全ての工具がマシニングセンタ内で回転中に測定されることにより、機外での工具測定では実現不可能な加工精度に到達している。加工後の工具状態の確認にも活用されているが、工具に付着するクーラントや切粉などの影響を受けることがない。これは、〝DIGILOG技術〟で採用されているフィルタリング機能により、工具の付着物等に因る測定誤差は排除されることによる。高価なワークも工具も『LC50-DIGILOG』を導入すれば、安心が確保され、心強い〝守護神〟として、製造現場を見守ってくれるだろう。