【前編】プライドをかけた熱い想い こんなドリルをつくりたい! ~超硬ソリッドドリルの歴史と小径穴加工の難しさ 三菱マテリアル~
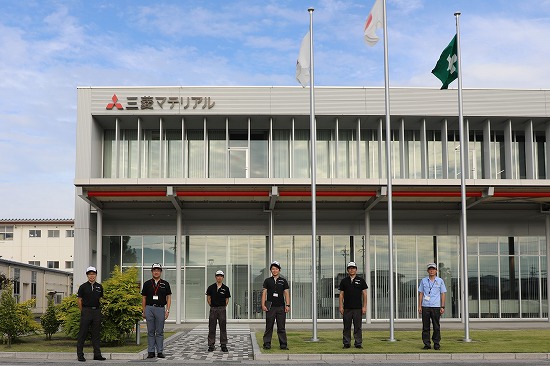
三菱マテリアル・加工事業カンパニーが精力的に画期的な新製品を開発し、いよいよ市場投入直前段階まで来ていると聞きつけた。そういえば、前回取材した『MS9025』も振動切削に対応するという次世代の安定した加工を求める現場のためにつくられた工具であり、最先端技術と独自性が際立っていた。このとき、「今後も世界で存在しない画期的な工具をつくる予定です!」と力強い意気込みを示していたことをふと思い出した筆者。「ひょっとしたら世界初になるかもしれない工具が登場するかも!?」と期待に胸を躍らせながら、愛用カメラをひっさげ、開発が行われている同社岐阜製作所へ向かった。
今回、新たに開発されたのは新小径ドリル『DVAS』。前編・後編に分けて掲載する。
三菱マテリアルが歩んだドリルの歴史
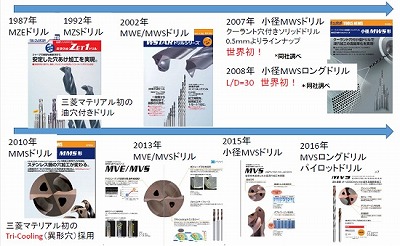
三菱マテリアルからドリルが登場したのは1987年。初代超硬ソリッドドリル『ミラクルZET1ドリル MZE』がこのとき誕生した。その5年後の1992年に同シリーズより同社初の油穴付きドリル『MZSドリル』がリリースされ、さらに10年後の2002年にはこれら製品の進化形として『WSTARシリーズ MWE/MWSドリル』を発売。この製品はフードプロセッサーをヒントにして設計されたというウエーブ刃形が切れ味を担保するつくりが特長だった。
さらに進化は続き、2007年にはWSTARシリーズからクーラント穴付きソリッドドリル『小径MWSドリル』がリリースされた。注目すべきはドリル径φ0.5からオイルホールを付けている点だ。同社調べによると、これがなんと世界初! その翌年にはさらに小径での最大L/D=30のロングタイプも登場し、こちらも同社調べでは世界初となった。
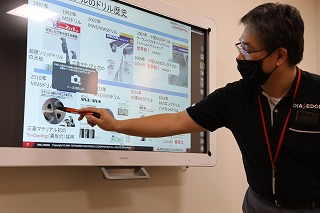
WSTARシリーズの進化は続く。2010年には培った技術をてんこ盛りにしたステンレス鋼用の『MMSドリル』が登場。このとき三菱マテリアルにとっては初となる三角穴の異形穴を採用し、この異形穴を同社では〝TRI-Cooling〟と命名した。この技術を応用し、2013年にはウエーブ刃形をチューンナップして新たに設計した汎用の『MVE/MVSドリル』、2015年には『小径MVSドリル(※丸形油穴)』、2016年には『MVSロングドリル/パイロットドリル』が市場投入された。
「昔はソリッドドリルといえばハイスドリルが多かった。超硬ドリルは特別なようで使いづらいイメージがあり、この風潮に危機感を感じた弊社は1987年に超硬ソリッドドリルの元祖として大々的にミラクルZET1ドリルを市場投入した経緯があります。弊社の超硬ドリルの歴史は超硬ドリルで初めてAlTiNコーティングを採用した〝強い超硬ドリル〟をつくったことからスタートしたのです。」と話すのは、同社営業本部・営業企画部の江波幸治部長補佐。
深穴加工の難しさは、切りくずが詰まり工具が折損してしまう可能性が高いことにある。元々超硬ドリルはハイスドリルと比べると硬いぶん、折れやすいというイメージがあった。「切りくず詰まりから発生した折損をなくそう!」という意気込みで製品を進化させ、2002年に登場したのがWSTARドリルであり、このシリーズは現在もあらゆる産業で重宝されている。
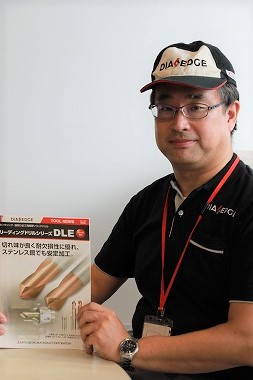
特に技術的にこだわったのは、オイルホールだった。φ0.5からの油穴付き小径ドリルであるMWSシリーズを出した2007年頃になると、従来、切削では不可能だった穴あけ加工もできるようになり、さらに小径ロングドリルでは2008年当時、世界初のL/D=30までを誕生させている。油穴も従来の丸形から、おむすび形の〝TRI-Cooling〟に進化していったのだが、この経緯について、「いくら油穴が付いているドリルといえども、ステンレスを切削速度VC=100m/minで加工ができるなんてことは、当時では考えられない話。そこでステンレス加工の大幅な加工能率のアップを図るために生み出されたのが〝TRI-Cooling〟でした。」と江波部長補佐。こうして歴史を振り返ると、三菱マテリアルが小径ドリルやロングドリル、オイルホール等の技術に強みを持って成長してきたのが分かる。
同シリーズは更なる進化を遂げ、2016年にはL/D=40まで(φ3以上)を標準化。他社に対して一歩進んだ先を提案する意気込みを見せつけている。
「ドリル市場において、技術力に関しては常に一歩先を進んできた。」と自信を見せる同社だが、その一方で、近年、競合他社もオイルホールを工夫し、ロングドリルにおいても様々な製品が市場に登場している。
「もうこれは、弊社の意地とプライドをかけて競合他社よりも更に先へ進んだ新製品をつくるしかありません!」
これが、今回、新製品開発にかけた三菱マテリアルの強い思いだった。
小径穴加工市場と熾烈を極める他社との競争
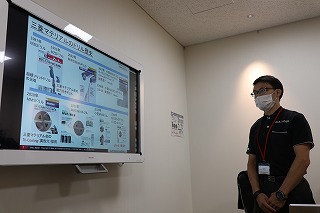
同社では、このシリーズに関して、従来では汎用径と呼ばれるφ3からφ12以上、あるいはφ20ほどの大きいサイズから先に製作をして、それを小径にブレークダウンすることを実行してきたが、小径ドリルのノウハウがかなり蓄積されてきた今回、新しく発売する『DVASドリル』に関しては、小径サイズであるφ3未満から開発をしたとのこと。従来とは違ったアプローチの仕方に並々ならぬ意気込みを感じる。
営業本部営業企画部の中山明信さんは、小径穴加工市場のターゲットについて、「小物精密加工がターゲットになっています。燃料噴射関連部品ではSCM440の他に、ステンレス鋼ではSUS420J2やSUS440Cなどが主流となっています。自動車のミッションでも、多段化によって搭載部品点数が増えているソレノイドバルブに電磁軟鉄が採用されるなど、難削材化が進む中で更なる安定加工が求められています。医療部品では、骨をつなぐボーンスクリュー等に、チタン合金やコバルトクロム合金、あるいはステンレス等といった難削材が生体親和性の高さから使用されており、高精度かつ安定した加工はもちろん、能率アップも両立したいという盛りだくさんのニーズが加工の現場にはあります。需要がたくさんある市場なので競合他社も放っておくはずがなく、さまざまな国内外メーカーがオイルホール付き小径ドリルを市場に投入しています。」と、工具メーカーが熾烈な競争の中で研究開発をしていることを示唆した。
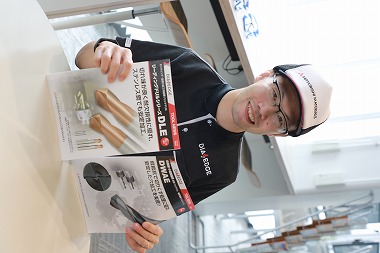
「弊社が小径ドリルMWSのL/D=30までを発売したときは市場にとって画期的な製品だったのですが、今ではどんどんキャッチアップされているというような状況です。それをいかにして凌駕していくか。それにはわれわれの強みを活かした製品を見せつけ、市場での存在感を改めて訴求していくしかありません。」(中山さん)
小径・深穴加工は技術的にも困難な課題が多い。中山さんは、「深穴加工の難しさは、切りくずが詰まりやすいうえ、折損の発生で折れたドリルが穴の中に残留するなど、トラブル対応が困難な点にあります。切りくずが、はけるようにステップを入れて、切りくずを分断する加工もありますが、そうすると能率が悪くなるのでノンステップの高能率加工が望ましい。しかし、これを実行するためには、工具にも様々な工夫が必要なのです。」と、技術的な課題への苦労をチラリと滲ませた。