【後編】三菱マテリアル 「こんなドリルをつくりたい!」~開発者の奮闘と新ドリルの実力~
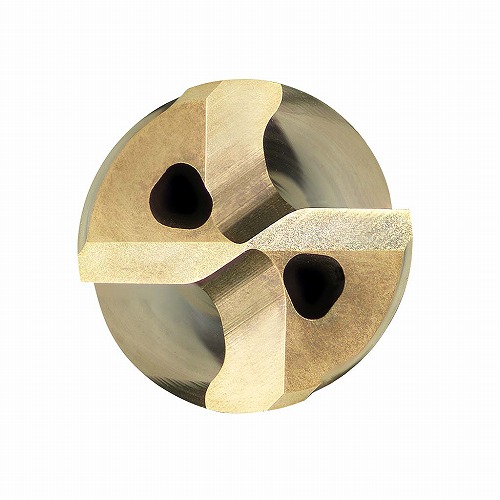
前回は、三菱マテリアルが辿ったドリルの歴史や小径穴加工市場と「こんなドリルをつくりたい」という同社の情熱を掲載した。注目したい点は、φ2未満の異形穴を有したオイルホール付きドリルにおいてL/D=40までというレパートリー展開が世界に存在しないことである(同社調べ)。さらに今回開発された『DVAS』は、φ1.0からのサイズ展開でL/D=50という驚異的な細長さであり、これもまた、過去に類を見ない製品だった。
後編は、開発者の奮闘と新ドリルの実力について掲載する。
営業側から開発に突きつけられた困難な要求をどうクリアしたのか―――!?
折損なんて許さない! ~より深い穴を安定的にノンステップであける~
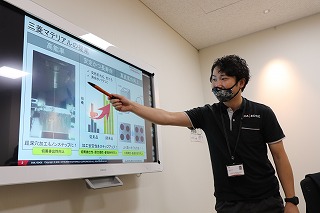
加工現場で起きるアクシデントに対応するため、営業側から厳しい要求を受けた開発部隊が新ドリルに仕込んだ数々の技術を披露する日がやってきた。
新ドリル『DVAS』は、より深い穴をノンステップであけること、従来、ガンドリルやドリルのステップ加工、あるいは放電加工でしか加工ができなかった箇所にも穴をあけるために開発された工具である。安定した加工を実現し、品質と能率を一度にアップさせることにより、経済効果を高めるためのドリルなので、折損し、ワークの中にドリルが残存してしまうおぞましい現象など、もってのほかなのだ。
「従来であれば、こうした場合、放電加工により追加工で穴をあけ直す必要がありました。このような不良を削減するためには新しいドリルの開発が必要です。従来のドリルは寿命が保つときもあれば、数穴で折れる時もあるため、不安定な部分があったのですが、今回はこの点も大幅に改善しております。」と自信を見せる開発本部 ドリル・超高圧開発センター 工具開発グループの佐藤晃さん。
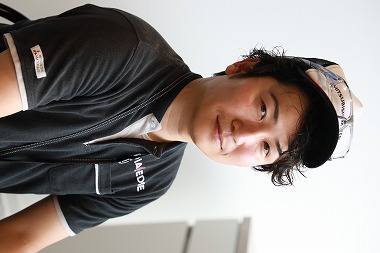
佐藤さんが特に力説していたのは、〝真直度の向上〟だった。穴の入り口はほぼ狙った箇所にあくが、深穴の加工では、些細な影響から、穴の出口がいびつなポジションであいてしまうことがある。
穴の位置精度や真直度が悪いと、「使えないね。」とユーザーに冷たくソッポを向かれてしまうのは、当然の話。ドリルの折損や精度の悪い穴加工などでユーザーの高価なワークをダメにするわけにはいかない。狙った箇所に真っ直ぐで美しく穴をあけることを実現しなければ、工具メーカーとしてのメンツは保てない。ユーザーの欲するのは美しい穴だ。しかも、無駄を省き、スピーディーな加工を求めている。
そこで、開発が考え抜いて新工具に与えたのは、新工具形状に新材種だった。これには、同社の強みである素材の成形技術が盛り込んである。
工具折損の理由に、切りくずが詰まって噛み込んでしまうことが挙げられる。この現象を改善するため、小径のドリルでも大流量のクーラントを出すことによって切りくずの排出を高めている。ではどうやって小径ドリルに大流量のクーラントを排出できるようにしたのか――――。
鍵を握る『TRI-Cooling』と新形状
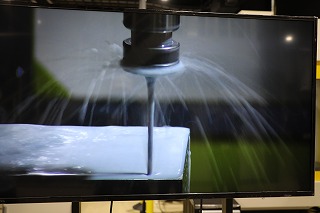
「この鍵を握るのはオイルホール『TRI-Cooling』です。」という佐藤さん。従来のオイルホールは、ドリルのサイズに対して小さな丸穴を採用していた。オイルホールのサイズを単純に大きく設定すると、ドリルの溝とオイルホールが干渉して破れてしまうという理由からだ。そもそもドリルのサイズが小さいので、ちょっとした誤差で外側にオイルホールが破れてしまう。そこで、「素材の設計、素材成形技術を見直し、今まで適用できなかった大きな断面積を持つオイルホール『TRI-Cooling』の採用に至った。」とのこと。これにより、クーラントのもつ運動エネルギーが増し切屑排出性に寄与する。従来比でなんと200%以上もクーラント吐出量が向上したという。
「この技術の活用で、切りくずの排出や切削熱の排熱が格段に向上し、寿命安定性に大きく寄与しました。」と笑顔を見せる佐藤さん。
では実際に他社品と比較してみよう――――。
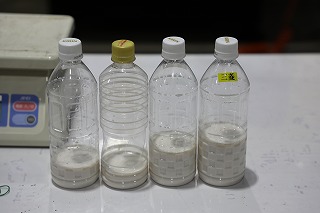
新工具『DVAS』と比較したのは、A社、B社、C社の3社。1分間にクーラントが排出した量を比較する。クーラント圧は2MPa。
気になるのはクーラントの勢いである。他社品と比べ、『DVAS』はクーラントの勢いが激しく噴水のようにコレットまで跳ね返っているではないか!クーラント量の違いはペットボトルで1番少ないものと比較しても倍以上、出ているのが分かる。
従来、「高圧クーラントの設備がないと小径の深穴加工は困難ですよ。」という推奨の仕方をしていた同社だが、今回、新開発した『DVAS』は2MPaでも十分排出性が高いことが分かった。ということは、今回の開発により、設備的な制約の敷居が下がったともいえる。高圧クーラント設備がなくても小径の深穴加工が高能率でできるということも、他社との差別化要因のひとつであろう。
今回は形状も新技術を盛り込んでいる。具体的には「究極の直線切刃」を採用し、シンニング切刃と主切刃を滑らかな円弧で連続的に繋ぐデザインにより、耐欠損性を向上させている。この「究極の直線切刃」は応力が集中する尖った部分を除いた切刃設計であり、切りくずが悪さをして局所的に欠けることを防止する。さらに、すくい面にはフラットなランド部を設けることで、耐クレータ性と切りくず分断性の向上を実現させていた。
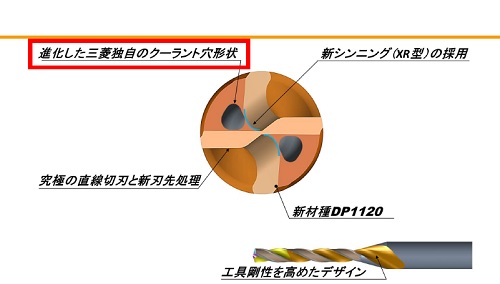
シンニング部には新形状(XR型シンニング)を採用したことにより、シンニング切刃で生じた切りくずをスムーズにカールさせ、切りくず流れを整流化することで、低抵抗かつ優れた切りくず分断性能を実現させていた。ドリル専用の超多層PVDコーティングと微粒な超硬母材を採用した『DP1120』も耐クレータ性、耐欠損性を向上させるための新材種だ。
なお、ショートドリルに関しては、首下部の長さが最小限となる独自のデザインを採用することで、工具剛性の向上と切りくず排出性の確保を両立している。切りくず排出領域をテーパー部にかけて設け、従来のデザインよりも工具性能が20%程度向上し、穴位置精度もアップした(*L/D=2,7,12のみ適応)。比較的浅い穴をあける工具には工具防振を高めつつ、工具そのものが持っている切れ味を確保した結果、このデザインに行き着いたとのこと。
それでは、過去に類を見ないφ2のL/D=50という驚異的な細長さの新ドリルで実際の加工デモを見せてもらおう。