【後編】三菱マテリアル 「こんなドリルをつくりたい!」~開発者の奮闘と新ドリルの実力~
加工デモが見せつける新ドリルの実力!
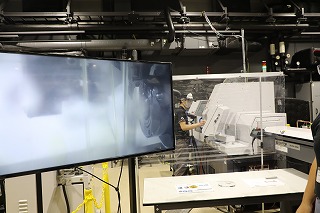
ここまでの深穴加工は、通常、トンボ加工で行わないと穴があけられない領域だが、トンボ加工は段取りに時間や手間がかかるうえ、穴位置がズレたり、食い違ったりして穴が貫通しないこともある。だが、今回の加工デモでは、自動盤によるステンレスSUS304のノンステップ深穴加工だ。使用機械は、シチズンマシナリー(株)製『Cincom L20』。これまでにバリ低減効果のあるリーディングドリル『DLE』や振動切削対応インサート材種『MS9025』等を評価してきたお馴染みの自動盤だ。より確実にユーザーでの使用条件を再現できるマシンで、深穴加工にチャレンジ!
スイッチオン!
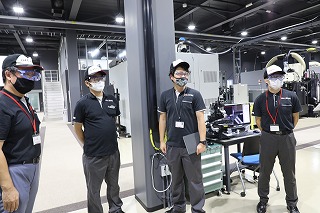
φ2の穴深さ100mm(L/D=50)なんて尋常じゃない長さだ。見ているだけでなんとなく不安になるほどである。工具が長ければ、工具の振れも気になる。バキっといっちゃうんじゃないか・・・あぁ、怖い(←心の声)
旋盤なのでワークが回転し、ドリルは回転していない。佐藤さんは、「工具自体が回転しないので、切りくずはクーラントで押し出すしかない。油穴が小さくてチョロチョロとしたクーラントしか出ないとなると簡単に切りくずが詰まってしまう。しかも自動盤加工の場合は粘度の高い油性のクーラントを使用するので、より加工が困難になってしまいます。それを回避するために今回の新ドリルが誕生したのです。難しい自動盤の加工でも安定加工ができるのが新ドリルの強みになります。」と説明をしてくれた―――と思ったら、あっという間に穴の貫通は終わっていた。
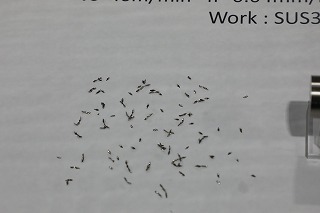
切りくずを拝見したが、非常に細かく分断されていた。これで、溝の中に切りくずが引っかかる問題発生確率を減少することが見て取れる。工具の長寿命化にも貢献するはずだ。
なお、φ2のL/D=20で合金鋼を加工したテスト結果では、従来品のものだと400~500穴で折損があったが、今回開発した『DVAS』は1,000穴加工しても欠損なく刃先が残っていた。また、航空機関系では比較的小さな浅穴のニーズもあることから、インコネル718でテストしたところ、従来品のものは数穴で折れたものの新製品は60穴を加工しても正常な摩耗で工具は生き延びていた。
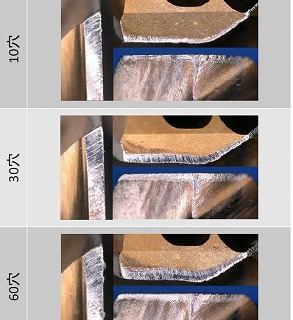
真直度についても、φ2のL/D=40で①パイロットドリルで下穴加工 → ②ロングドリルでノンステップ加工を実行したところ、海外メーカーと比較すると、海外は0.15mmから0.16mmほど曲がっているのに対し、『DVAS』は、0.05mm以内に収まっている。
最後に、営業本部・営業企画部の江波幸治部長補佐は、「われわれがサポートしている燃料噴射関連部品やボーンスクリュー、ソレノイドバルブなどを加工しているお客様は、加工精度や加工の安定性について課題を抱えていらっしゃいます。特に医療部品のキャニュレイテッドスクリューやボーンスクリューなどは、穴あけ加工をしていくと、どうしても加工に時間がかかってしまうので、できればワンステップで加工したいというニーズがあります。また、従来、深穴加工はトンボ加工が主流でしたが、段差ができたりするなど医療部品に関する完全性の観点からもよろしくありません。このときのサイクルタイムを計算したところ、メイン側のサイクルタイムが3.48分。サブ側の加工時間は4.67分で、ダウンタイムが発生します。それであればこのメイン側の残っている時間にワンステップで加工できれば能率があがります。これが今回新開発したドリルの優位性です。」と話した。
現在、さまざまな国内外メーカーがオイルホール付き小径ドリルを市場に投入しているが、異形穴である『TRI-Cooling』を世界に先駆けて1φから採用していることに、「他社の追随を許すわけにはいかない!」という同社の意地とプライドを見ることができる。そして、「こんな工具をつくりたい!」という情熱が、世界でも類を見ないこの工具を誕生させたのだ。
なお、この『DVAS』は、2020年度下期に発売予定である。