MOLDINO 野洲工場を徹底取材! ~最新工具で加工デモを拝見~
驚愕! 人を介さずに工具をつくる仕組みをつくっていた!
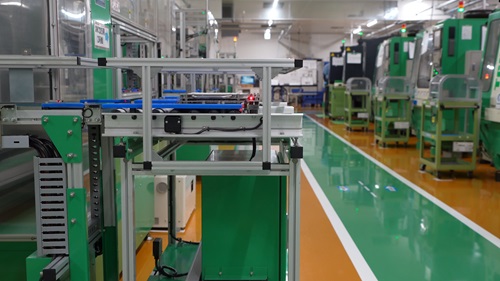
工場内を見学した。まずは削った後の工具やワークの状態を評価する部屋を覗くと2人が作業をしていた。1人は電子顕微鏡を覗いて工具のダメージを観察し、もう1人はデジタイザでワークの全体形状を評価していた。これはテーブルの上にワークを載せると、テーブルが360度回転しながらワークを撮影していき、その画像を組み合わせて3DモデルをCAD上に表すことができる仕組みである。
CADデータと加工後のワークのデータと照合することによってどの部分が何ミクロンほどズレているかを割り出すことができるので、ツールパスを微調整したり補正を入れたりしながら顧客に対して最適な加工提案に結びつけるのだそうだ。
グラファイト切削加工室もあった。単独の部屋になっているのはグラファイトを削るためだという。「グラファイトは加工をすると霧状の切りくずが出て、粉塵として舞うので他設備や治具に影響が出ないようにしているため。」と聞いた。
野洲工場の主力製品をつくる製造ラインに向かった。エンドミルとドリルがメインの野洲工場では、成田で超硬の素材を作ったものが長尺の状態で野洲工場に届く。それを切断して円筒面を仕上げ、段加工をして、先端に刃を付けていくという工程で進んでいく。
工程には時間あたりの出来高数が一番小さい〝ネック工程〟がある。仕掛かり在庫が滞留してしまえばアウトプットに時間がかかるため、「ネック工程に焦点を当て、パフォーマンスを妨げているものを集中して改善している。」と聞いた。タイミングが合わない時期の資材の投入などを防ぐことで無駄な仕掛品を削減すれば、そのぶんキャッシュは増えるというわけだ。
小径工具の恒温室があった。超硬エンドミルはMOLDINOの主力製品だが、その中でも現在、小径工具に非常に力を入れているという。
小径工具は小さい機械を使って加工をするが、この前工程ラインで、仕掛かりを管理していた。ここで仕掛かりが増えてくれば、前工程は止めるというやり方でリードタイムの短縮を実現しているという。
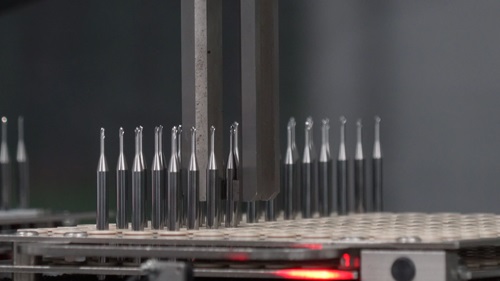
歩いていると、ラインにほとんど人がいないことに気付いた。省人化ラインで24時間稼働している。前工程が終わるとコーティングをして刃先処理をする工程に移行するその全てが共通パレットで加工ができる仕組みである。RFIDのタグが入っており、RFIDの情報が入ったものをセットすると、自動的に自律走行搬送ロボット(AMR)にて搬送されていく。搬送されたものは機械に入って加工が行われる。また、寸法が変化すると当然補正をかけていくものだが、拝見したラインに関しては加工したものが自動で測定器に搬送され、測定をする。測定した結果、しきい値の範囲から外れたものに関しては自動補正がかかる―――という、徹底的に自動化された仕組みである。
ちなみにこのラインでつくっている工具の最小径は30ミクロンの工具であった。
さて、ハイテクノロジーがつまった工場内でも、各職場で働く人たちが一番多く歩くメインストリートがある。工場でいう〝銀座通り〟と呼ばれる道である。それぞれのチームの活動が示されており、日々の生産状況も見える化してあった。
機械の台数が非常に多い工場の中では、従業員によって、「私はこの機械しか使えない。」あるいは「Aさんはこのアイテムは作れるけど、Bさんはまだ作れない。」という問題が発生しがちだが、「従業員の多能化を進めていかないと省人化ができない。」という考えのもと、野洲工場では多能化マップを作成し、師匠と弟子に分けて教育をしていく活動も実施している。これを実行することで、省人化をしながら、最低限の人数で多くの台数をこなせるような体制を構築していた。