「未来の扉を開くエンジニア集団」新川製作所 新村社長に聞く
最高の設備と切削工具で量産に向けた課題解決のサポート
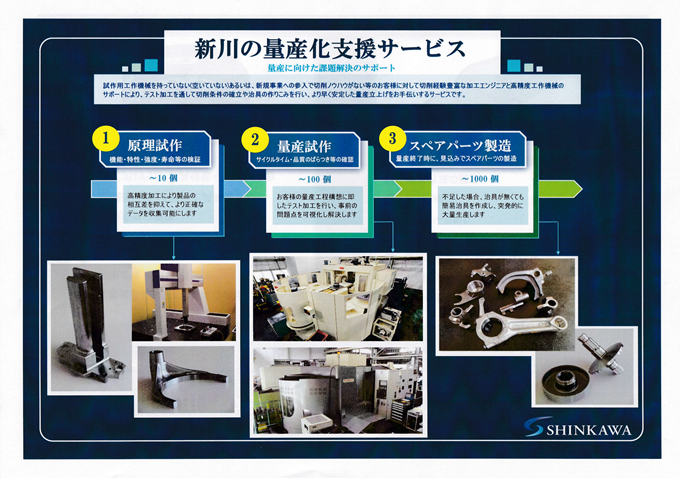
同社は保有する設備の強みを活かして、量産に向けた課題解決のサポートを行っている。試作の難しい点は、その都度、〝違うもの〟を加工しなければならないことだが、優良企業であれば、依頼を受けた時に、「顧客の要望に短納期で応えたい」と考えるのは当然だろう。
同社では、試作用工作機械を持っていない、あるいは機械が空いていない場合や、新規事業への参入で切削加工のノウハウが乏しい顧客に対して、切削経験豊富な加工エンジニアと高性能工作機械のサポートで、テスト加工を通じて切削条件の確立や治具の作り込みを行い、より早く安定した量産立ち上げをサポートする心強い仕組みを構築している。
高性能工作機械の能力を最大限に引き出す切削工具の数々を公開!
~いかに加工課題を克服したか~
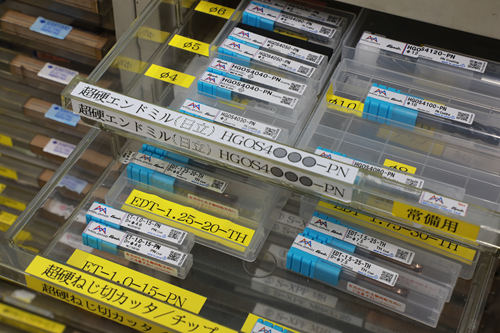
「切削工具の能力が高くなければ、製品の面品位も悪くなり、部品や金型の精度に影響を及ぼします。」と新村社長は言う。切削工具のアイテム数は非常に多く、高性能工作機械の能力を最大限に引き出すには、条件にマッチした切削工具の力なくしてクオリティの高い製品は生まれない。同社の高度な仕事を支える切削工具の多くはMOLDINOが活用されていた。
新村社長にMOLDINOに魅力を尋ねると、「多少高価でも寿命が長いほうがいい。最後の仕上げは絶対にMOLDINOと決めている。もちろん同等の品質を実現した安価な切削工具も探してはみたものの、MOLDINO以外で、われわれが求める品質を維持できるものが今のところ見つけ出すことができなかった。」と〝MOLDINO推し〟を告白した。
――――ということで、実際にどんな加工シーンでMOLDINOの工具を活用し、加工改善とともに高能率・高精度加工を実現したのか――――。
■エポックDスレッドミル EDT-TH
主に金型の焼き入れ後のタップ加工に使用。従来は焼入れ前にマシニングでタップ加工を行っていたが、焼入れ後にタップ加工が可能になったため、マシニング加工を行わずに焼入れ工程に行けるようになった。これらの成果により工程の削減、短納期が可能になった。
従来は、焼き入れ前にタップなどのマシニング加工を行うと、焼入れ後の旋盤加工で断続切削を行わなければならず、旋盤加工では断続切削の対策として加工条件を落とすなどの対策を行っていたが、それでもチップが欠けるなどトラブルが多発した。改善策として、同工具を使用することにより、焼入れ前のマシニング加工を止め、焼入れ後に行う旋盤加工の断続切削が無くなり、切削条件を上げることができたことで、加工時間の短縮につながった。お陰で断続切削による刃先の欠けなどの嫌なトラブルが無くなった。
焼入れ後にマシニング加工を行うことで焼入れによる歪みの影響がなくなり、製品の精度が上がった。マシニングの加工時間は焼入れ後の加工のために増えたものの、5軸加工機を活用して工程削減を実現している。また、設計変更などによる焼入れ後のタップ追加工など、「新しい仕事にも対応することができた。」という。
■エポックTHハード CEPS-TH CEPR-TH
焼き後HRC55以上の中仕上げ~仕上げ加工はこの工具一択! 焼き後の加工の面精度、刃物の耐久性と耐摩耗性が優れているので、安心して使っているとのこと。
■エポックターボミル ETM4-TH ETMLN4-T
φ3~φ12を粗加工メインで使用。小切り込みによる安定した加工で無人運転などに一役買っている。焼き後加工にも有効でHRC60の底刃による粗加工では耐久性が最も高かった。
■エポックパナシアスクエア HGOS4-PN
生材の仕上げ加工に使用しており、「仕上げ面の精度とコストパフォーマンスが良い」と絶賛!