不二越 工具はここまで進化した! 「バリレスシリーズ」の実力を探る
ものづくりは工具で進化する! バリレスドリルの優位性
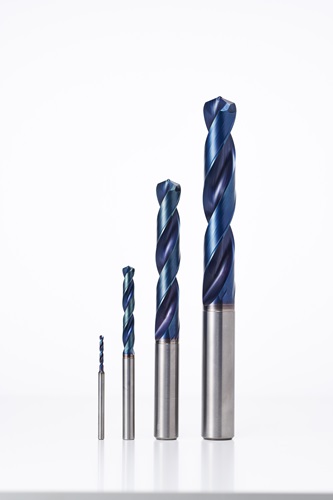
場所を移して加工実演を拝見した。
穴あけの際にドリルの〝抜け際〟に力がかかり、この時にできる〝陣笠〟(傘の形をした切りくず)が取れた後に残るバリ。厄介なことに陣笠そのものが残る場合もある。通常の汎用ドリルで穴をあけると、「加工した穴数の50~75%ほどに陣笠が残る。」という。
ドリル加工においてバリや陣笠発生のメカニズムについて、「汎用ドリルで(先端角140°)では穴の出口側で曲げと塑性流動が発生します。これを抑えるためには、回転数や送りを下げるのが一般的ですが、加工能率を落とすことでサイクルタイムが長くなるのです。こうしたデメリットを払拭するのが〝アクアREVOドリルバリレス〟なのです。さぁ、見てください!」と自信を見せる干場部長。
まずは汎用ドリルと『バリレスドリル』で5穴ずつ穴をあけるデモを行った。被削材はSS400。比較的柔らかい材料でバリが出やすいものをあえてチョイスしたようだ。切削速度は50(m/min)。見学しやすいようドライ加工のため、切削速度は少し下げている。横形のマシニングにワークがセットされ、加工の様子をカメラで映す。
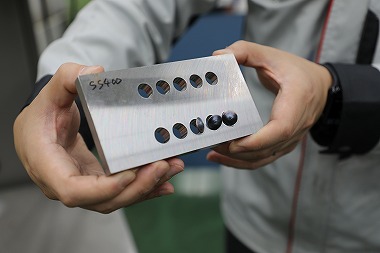
結果は写真の通りである。陣笠とバリは一切ない。ワークをさわってみると、バリレスドリルであけた穴の表面はツルツルだ。汎用ドリルはバリが目視でも感じられ、怪我を恐れて触るのを止めた。これでほぼ汎用ドリルと同じ寿命を確保できるというから驚いた。穴加工の出口での貫通状態の比較では汎用ドリルで初期のバリ高さ0.17ミリに対して1/10以下の0.01ミリを実現している。
続いて現場でも多く加工されているバリ取りが難しいクロス穴加工(既に穴があいている箇所に交差する穴をあける加工)の実演を見学。自動車や産業機械などに多く使用されている主要部品のシャフトなどは、中空の箇所に外周からの穴あけをする加工が多くあるが、バリが出やすいうえ、陣笠も残りやすい。その内部のバリ取りには多くの加工現場が苦労されており、「通常はバリ取りツールやブラシなど、バリ取りで3工程を入れているユーザーもいる。」とのことで、クロス穴加工で残ってしまったバリは、タイムパフォーマンスを低下させる原因であることがわかる。
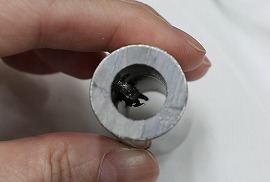
今回はシャフトを想定してS45Cの中空穴に5軸加工機を使用して外周から3箇所穴を開けた。条件は、汎用ドリル、バリレスドリルともに切削速度は87.5(m/min)、送り率は4%、切削油は水溶性。まずは、汎用ドリルで穴をあけ、続いて軸をぐるっと旋回し、クロスしている中空穴のところにステンレス製のブラシを入れ、バリを除去する。
ところが――――――。
加工を終えて穴を覗いてみると――――。
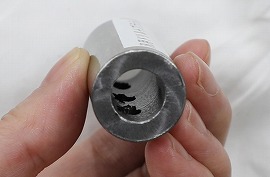
ブラシを入れてもワークにしがみつくような未練がましいバリが残っているのを発見! なんというしつこいバリ! これがクロス穴加工の厄介なところなのか!
この工程で出たバリを万が一、放置した場合はバリが脱落するなどして部品が故障し、品質問題に発展しかねない。従来はこの工程に工程を重ね、時間をかけて加工を行うしかなかった。ところが今回、同社が新たに開発したバリレスドリルは、一発穴加工にてバリレスを実現できるという。
ということで、バリレスドリルを用いたクロス穴加工を見学させてもらい、その内部の穴を確認すると、写真にあるとおり、ツルピカである。
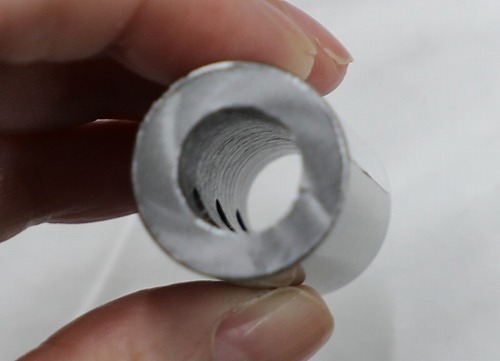