日本最大の金型メーカー キヤノンモールド 斎藤社長に聞く ~多品種大量化への道~
友部事業所で見た内製化へのこだわり ~高精度・高品質の金型を実現~
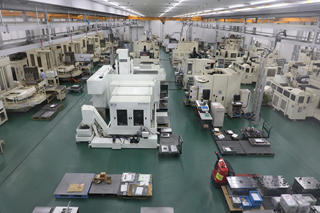
近年、熾烈な国際競争力に煽られ、価格競争の消耗戦が繰り広げられ、ユーザーの製造現場ではコストの見直しや、生産体制の見直しなども進んでいる。高付加価値金型へのニーズは高まるばかりだ。
このような背景から、同社が狙うのは、金型の〝高耐久〟と〝高精度〟だ。この2つが実現していれば金型のメンテナンス性が非常に良くなるなど、顧客の生産におけるトータルコスト削減に貢献することになる。
同社の最大の強みは、なんといっても、ダイセット(モールドベース)の〝内製化を構築〟している〝高い生産技術力〟だ。『高精度金型は高精度のダイセットから生まれる』という強い信念のもと、ダイセットをほぼ100%内製化する専用工場を稼働させ、顧客のニーズに応えている。
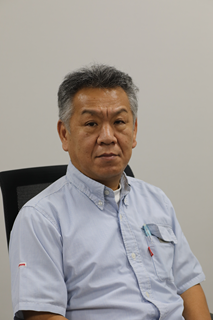
友部事業所のレイアウトは、材料や部品の入荷、ダイセット加工、内製ユニット組立、金型部品・駒加工、仕上げ・組立という右から左への一方通行で、無駄な移動を排除できる仕組だ。工場内は柱がなく、取締役友部事業所長の芝沼文彦氏(以下芝沼所長)は、「トラス梁の強固な屋根を設置することで無柱空間が実現できた。梁の空間に配線や配管を通すことで、整然とした機械加工工場ができた。」とメリットを話した。また、ダイセット製造エリアでは、精度が狂う原因になる機械の振動が伝わらない床構造をしており、徹底した高精度へのこだわりを見せている。
芝沼所長は内製化へのこだわりについて、「金型の基となるダイセットを高精度に仕上げなければ、高品質な成形品が生まれない。お客様に納める製品が高い品質と長寿命化を実現したものであると同時に、美しい外観であればお客様も大切に使用してくれる。」との熱い思いを示した。
高品質な金型をつくるために各寸法、公差を厳しくし、組込再現性を高め、メンテ時間削減、変形防止による長寿命化を実現している同社。ダイセット加工ラインでは、安田工業の大型マシニングセンタがズラリと並ぶ。こちらはYASDAストリートといった印象だ。
電極・放電加工プロセスの大幅短縮にも注目したい。これを実現したのは、電極設計から放電加工までの加工プロセスを自動化し、工数削減と省人化を図ったことによる。具体的には従来、1電極に31分かかっていたものが、12分(61%)の短縮に成功、年間、7,093時間(対象22,400本)を削減し、1名省人を実現している。

また、同社では材料の品質を保証し、高品質な金型を提供するため、熱処理工程も内製化している。芝沼所長は、「熱処理は肉眼では見えない金属組織を変化させる工程なので、温度設定、管理を慎重に行い、熱処理後の製品は毎回硬度検査を実施している。」と確実な品質管理を実現していた。金型製作のリードタイム短縮も自社で熱処理を実現することのメリットである。
細かいことだが、磨き工程の椅子がゲーミングチェアだったことに気付いた。磨き工程は気を使う作業が長時間続くため、「少しでも疲れないように」という配慮だという。