ニュース
タンガロイが先端交換式ドリル『DrillForceMeister』(ドリルフォースマイスター)を拡充
タンガロイ(社長=木下聡氏)がこのほど、先端交換式ドリル「DrillForceMeister」の販売を開始した。この製品は、更なる高速・高能率の穴あけ加工を目的に開発された2枚刃仕様の大径穴明け加工用工具(工具径φ26~41)。
「DrillForceMeister」のヘッドクランプ方法には、独自のアシンメトリーコンタクトとねじを使用したクランプ方法を採用し、ねじを完全に外さずにヘッド交換が可能なため、簡単で迅速なヘッド交換を可能にしている。ヘッド交換のみでツールホルダからのドリルボディの脱着や突出し量の調整が不要となることから、工具交換時間を大幅に短縮でき、必要に応じて機上での交換も可能だ。また、このねじは容易に交換可能で、ねじ交換を行うことでドリルボディ本体を長い期間使用できる。
ヘッドのクランプ設計においては、ヘッドの拘束面を大きく確保し、高い切削力が発生する高送り条件下でもヘッドを安定して保持することが可能。また、高精度で加工された拘束部により、優れたヘッドの繰り返し取付け精度と振れ精度の確保を実現している。
ヘッドの刃先処理にはR形状のホーニングを適用することでコーティングの密着性を改善し、材種には高信頼性材種AH725を適用、革新的な刃先処理と材種性能のコンビネーションにより長寿命を実現した。
「DrillForceMeister」は、加工能率の向上だけでなく、工具交換時間の大幅短縮、再研削にかかわる費用をゼロにできるなど、トータル加工コスト削減に大きく貢献するとしている。
主な特長
●工具径:φ26.0~φ41.0、加工深さ:L/D=3, 5に対応
●2枚刃ドリルで大径穴明加工の生産性を改善
●独自のヘッドクランプ方法によって、簡単かつ高精度のヘッド交換が可能
●ヘッドの拘束面を大きくし、高いトルクのかかる大径穴加工でのヘッド着座の安定性を向上
●クランプ方式を取り換え可能なねじ構造にし、ねじ交換によりボディ本体を長く使用可能
●切りくず排出性能と剛性のバランスに優れる溝形状の採用
●R形状の刃先処理と高信頼材種AH725の適用で長寿命を実現
セコ・ツールズが「My Pages デジタルポータル」に工具提案機能を追加
セコ・ツールズが「My Pages デジタルポータル」に工具提案機能を追加した。部品生産に適したフライス加工、旋削加工、穴加工、ねじ切り加工のソリューションを特定できるよう支援する。
Suggest (工具提案)機能は、何千ものセコ・ツールズ製品の総合的な切削工具データと、80 年以上にわたる加工エンジニアリングや工程開発で蓄積した専門知識を統合したもの。この高度な情報により、シンプルなものから複雑な部品の製造に適した切削工具や加工戦略をすばやく簡単に提案できる。技術が進化し、新しい製品や工程が発表されるたびに、Suggest (工具提案)機能はセコ・ツールズの金属切削専門家によって更新されるので、ユーザーは常に最新の情報にアクセスできる。また、被削材や加工条件などのユーザーが定義した情報に基づいて、材料または加工用途の観点から、生産性の高いソリューションを提示。製品カタログをめくって数時間かけて調べるのとは対照的に、Suggest (工具提案)機能では数分しかかからない。推奨の切削工具の価格と在庫状況も、すべて Suggest (工具提案)機能から確認できる。
さらに、各データ入力フィールドにデフォルト値が入力されているので、金属加工の知識が不十分でも利用できる。ユーザーは、入力の各段階で切削データを見直し、編集、絞り込み、並べ替えを行ったり、別の提案と比較したりすることもできる。推奨工具情報はすべて保存でき、デジタル共有することも、印刷して配布することも簡単にできる。
セコ・ツールズで My Pages のサービス管理者である Ben Alexander氏 によると、「技術的能力の向上と工程最適化のサポートを切削工具サプライヤに求めているメーカーがますます増えている」とのことで、「従業員の能力が不十分な上、金属加工の技術革新が急速に進み、自分たちだけでは可能性を最大限に発揮できない現場が多い。このため、統合サポートサービスや、最新の被削材と市場傾向に対応する高度な切削工具を提供することで、お客様をしっかりサポート致します」としている。
顧客が新たな加工に適した工具を見つけるためのサポートを必要としている場合でも、進行中の加工に合うオプションを探している場合でも、Suggest (工具提案)機能が 24 時間年中無休で工程計画をサポートする。クラウドベースの Suggest (工具提案)機能はMy Pages からアクセスできる。My Pages は、オンラインウェブブラウザを介してコンピュータ、タブレット、スマートフォンで利用できる。サポートするどのデバイスでも同じ機能を利用でき、表示が最適化され、操作も簡単である。
ヴェロ・ジャパンが 統合型CAD/CAM/CAE最新版「VISI 2016 R1」をリリース
ヴェロ・ジャパンは、統合型CAD/CAM/CAEの新バージョン『VISI2016R1』を、このほどリリースした。「VISI」は、世界最先端の統合型CAD/CAM/CAEソリューションで、金型設計製造に適するだけではなく、その他業界でも幅広く利用されているシステム。最新版『VISI2016R1』では、従来より定評のあるCAD機能をさらに強化し使いやすさと作業効率の向上、Veroグループの先端テクノロジーを取り入れたCAM機能では大幅な加工時間の削減を実現している。
主な強化ポイントは、①クイックアクセスツールバーの採用、②機能の簡素化により操作性の向上を実現、③スケッチ機能強化による作図時間の大幅短縮、④キネマティックシミュレーションによるアセンブリ機構の動作確認及び干渉チェック――である。
日本能率協会 新会長に中村正己氏
日本能率協会(JMA)は、6月15日に開催した2016年度会員総会において、会長ならびに理事長が互選され、新会長に中村正己氏が、新理事長に吉田 正氏がそれぞれ選任された。任期は1期2年(2016年6月15日~2018年度 会員総会終結の時まで)。
「5000億円の達成に向け全力をあげて取り組んでいく」 日本機械工具工業会が平成28年度定時総会・表彰式・懇親会を開催
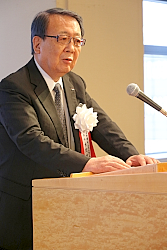
総会終了後の表彰式では、生悦住賞表彰、新庄賞表彰が行われ、表彰式終了後、懇親会が開かれた。
懇親会では、本間会長が、「昨年度の当工業会の生産実績は4591億円である。これを会員の皆様とできるだけ早く目標の5000億円を達成したい。この5000億円の達成に向け、私自身全力をあげて取り組んでいく所存である。会員の皆様におきましてもご理解ご協力のほどをお願いするとともに、忌憚のない前向きなご意見を賜りたい」とあいさつをした。
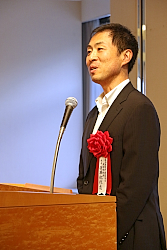
乾杯の発声を石川則男副会長(オーエスジー社長)が行った。
新入会員の紹介のあと、宴たけなわの中、牛島 望副会長(住友電工常務)中締めを行い散会した。
(注:記事は6月8日現在のもので、佐脇経産省産業機械課長は、現在、内閣府 規制改革推進室 参事官に就任しています。)
平成28年度生悦住賞受賞者
この賞は、生悦住禎太郎ダイジェット工業(株)会長が、1978年に傘寿を迎え、同年は超硬工具協会創立30周年にあたることを記念して、協会に多額の寄付をした。この意向に則り、有効活用を目的として生悦住基金が設けられた。この賞は、①会員で草の根的に功労のあった人、②会員内外を問わず業界発展に貢献された人を顕彰するために制定された表彰制度である。
諸熊正俊氏(日本タングステン株式会社)
■功績の概要
氏は、平成14年より超硬工具協会賞選考委員会、総務、業務、資材など主要委員会に参画された。特に、実質2期4年間資材委員長として超硬工具主要原料のタングステン、コバルト、タンタルの需給動向に注力され、それぞれ原料商社による定期講演会の開催を実施、会員の情報の共有化を図った。特に、平成17(2005)年年頭から高騰がはじまったタングステンの需給動向の情報入手に尽力された。ITIA(国際タングステン工業協会)からのタングステンをはじめとする超硬工具主要原料の情報入手に奔走されるとともに、大所高所から原料の安定確保を模索された。また、コバルトの特定化学物質指定時には、ITIAのHSE(健康、安全、環境委員会)を通じ、主要海外工具メーカーが公的機関と共同で行ったコバルトの環境測定データの入手に動かれ、ユーザーへの規制免除に結びつけた功績。
(タングステン・モリブデン工業会専務理事を平成28年1月末退任)
平成28年度新庄賞受賞者(13社13名)
この賞は、新庄鷹義氏が55年在任された冨士ダイス株式会社社長職から会長職へ昇格された年、合わせて米寿の慶事にあたり、同氏からの多額の寄付を元に新庄基金が儲けられたことからはじまる。受賞資格者は会員企業(正会員)の“陰徳の士”的立場にある人(一般には目立たないながら、会社にとって非常に有用なことを実践している人、ボランティアを含む)で、所属企業から趣旨にそった方の推薦を受け表彰する制度である。
〇三好忠義氏(オーエスジー)
設計者として各種エンドミルやタップを開発し、設計課長を務めた後、2005年から11年以上、国内外グループ会社(約50工場)の品質保証体制を現地で支援している。長年の経験から品質のみならず設計技能や納期管理の知識も豊富。分かりやすく教えてもらえるため、国内社員はもとよりグループ会社の社員からの信頼も厚い。
〇望月麻岐氏(関西超硬合金)
入社以来13年間、業務・営業サポートを担当する社員として、常に陰日向なく従事し、上司、社員、さらにはお客様からも絶大なる信頼を得ている。また、社内における環境改善活動グループ長として率先してテーマに取り組む姿勢はその人柄と相まって活動の原動力となっている。明るい笑顔と笑い声で社内の雰囲気を柔らかくする存在でもある。
〇野間智美氏(京セラ)
1984年の入社以来、生産管理業務に従事し、ユーザーに如何に早く切削工具の製品を届けるかを考え、CS工場に務めてきた。あらゆる場面で真摯に対応し、営業・製造の双方から頼られる存在であると同時に、お客様とのつながりを大切に考え、同行販売経験を経て、常に明るく前向きに行動する姿勢が若手社員育成に欠かせない存在である。
〇南条 悟氏(共立合金製作所)
1984年入社。超硬素材の成形加工現場を経験した後、技術開発室において長年にわたり、社内加工設備や治工具等の製作に従事している。仕事に対してひたむきで真摯な取り組み姿勢は、同僚や後輩の良き手本となっている。同社の精密加工技術を支え、まさに縁の下の力持ちとして欠かせない存在である。
〇出口雄二氏(セコ・ツールズ・ジャパン)
1993年7月入社以来、CAD責任者として長きにわたり顧客志向のサービスに徹した気配りで社員のみならずお客様からも絶大な信頼を得ている。何事にもまじめに取り組む姿勢は、その人柄と相まって模範的社員として誰からも慕われる存在で、同社の販売手法である「提案営業」を影から支える存在であり、同社の成長を支えてきた。
〇岩渕圭樹氏(日本ハードメタル)
1980年入社以来、プレス用完成粉末を生産する現場で35年間勤務。定年後もシニアスタッフとして継続勤務し、定年まじかに始まった改善提案活動では若手社員と一緒にテーマに取り組み、QCサークル活動においてもサークルチームの代表として「自身生涯初」という発表を行うなど、積極的な姿勢は若手からも慕われている。
〇稲垣達也氏(日本特殊陶業)
1971年入社以来切削工具関係の職場に従事、特に工具研磨工程での実務経験が豊富で、複雑な加工を手動機でこなす仕事ぶりは職人の域に達しており、寸法や形状検査を雇用延長の今でもこなしており、新しい設備に臆することなく取り組む姿勢は、ものづくり作業者の見本となるものであり、知識を惜しみなく伝える姿勢から人望も厚い。
〇玉井眞一氏(日研工作所)
金属35年、入社以来真面目にコツコツと仕事をこなす。「実直」という言葉がぴったりな人は他にいない。作業は極めて丁寧で、高精度が要求される作業にも絶対的な信頼がある。ミスはほとんどなし。万が一ミスがあっても同じミスは2度と繰り返さない。自分の損得より、仕事を優先する責任感を持ったプロフェッショナルである。
〇櫻井文明氏(日本超硬)
1957年入社以来、超硬工具製造ひとすじに従事してきた。その中でも特にプロファイル加工は長年にわたり様々な問題を乗り越えながら、技術を磨き、困難な仕事に果敢に挑戦してきた。その積極的な姿勢は上司の信頼も厚く、また、何事にもまじめに取り組む姿勢は全社員から模範的な社員として、同僚、後輩から慕われる大きな存在でもある。
〇牛田博士氏(日本特殊合金)
昭和60年入社以来30年間、精密加工分野において精密金型の磨き加工に従事し、真面目にコツコツと技術を構築してきた職人である。また、作業長としても永年会社発展に大きく寄与するなど縁の下の力持ちとして欠かせない存在である。後進の育成や作業方法改善に努めるなど多岐にわたり活躍しており、社員の模範的な存在である。
〇中西考之氏(富士精工)
1969年に入社以来、ほぼ一貫して生産管理や外注管理に従事。現在に連なる同社の生産管理のしくみの原型を作り上げた功労者である。陰から同社のものづくりを支えただけでなく、若い時分には、毎年現場の若手社員をスキーに連れ出すなどして、社内コミュニケーションの促進を図るなどして同社の家族的な社風の醸成にも貢献した。
〇斉藤直樹氏(三菱マテリアル)
1980年入社以来、超硬工具の合金素材の製造・販売並びに工場窓口・出荷業務等に精通している。現在はその経験を活かしつつ、工場の環境管理に携わり、誠実な仕事ぶりで工場の環境保全を支えており、環境管理のレベルアップ、省エネ・ゼロエミの推進は社内での評価も高い。明るい人柄で周囲の信頼も厚く他の社員の模範である。
〇野口 豊氏(彌満和製作所)
1963年入社。同社は製品を製造する機械を内製で製作してきた。入社以来一貫してこの内製機械に取り組んできた。主に旋盤加工を担当し、高精度が要求される部品加工において卓越した技能を有している。現在は嘱託社員として週2日出勤し、若手に技能を伝承していて、その誠実さと温和な性格で周囲から慕われている。
DMG森精機の「IGA INNOVATION DAYS 2016」に過去最多の9600名を上回る来場者
DMG森精機(社長=森 雅彦氏)が、6月7日(火)~11日(土)の5日間、同社の「伊賀グローバルソリューションセンタ」に、最新鋭工作機械58台を一堂に展示するプライベートショー「IGA INNOVATION DAYS 2016」が開催され、過去最多の9600名を上回る来場者が足を運んだ。
今回は自動車、航空機、建設機械、医療機器、金型、エネルギー産業など、さまざまな業種における最新の加工事例を紹介し、会場は連日活気に溢れていた。
今回のテーマは“DMG MORIのトータルソリューション” 。
世界初公開を含む全14種類のテクノロジーサイクルを発表した。このテクノロジーサイクルとは、工作機械にオープンイノベーションを取り入れ、あらゆる場面で同社の組み込みソフト技術により、誰にでも分かりやすい操作やプログラム、対話機能などを提供することで、複雑な加工や段取り作業などを簡単かつ短時間で実現するDMG MORIの新しいソリューション。今回は、振動を検知し機械を未然に保護する「MPC(Machine Protection Control)」、スカイビング加工の対話型プログラミング機能である「ギヤスカイビング」、回転軸中心の計測・補正を行う「3Dクイックセット」の3種類でデモンストレーションを行い多くの来場者の興味をそそった。テクノロジーサイクルは、今後も順次拡大し、発表する予定。
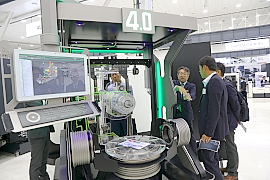
また期間中は、テクノロジーサイクル、自動化システム、航空機、5軸加工機などの最先端技術セミナーを開催した。4月から新たにDMG MORI AKTIENGESELLSCHAFTのChairman of the Executive Boardに就任したChristian Thönes氏による「ドイツでの取り組みについて-インダストリー4.0」のセミナーも開催し、ドイツから発信するインダストリー4.0を用いた最新の取り組みを紹介し、多くの方が参加した。
同社では、「会期中にお客様からいただきました貴重なご意見、ご感想を今後の製品開発やサービスサポートの一層の充実につなげていく」としている。
世界最大の加工に関するデータベースの構築
森社長とDMG MORI AKTIENGESELLSCHAFTのChairman of the Executive Boardに就任したChristian Thönes氏が会見を開いた。
DMG MORIはグローバル拠点として全世界76カ国に164の販売サービス拠点、21の工場があり、5月末時点で12,465人の従業員が在籍している。このうち約7,000人が工場・研究開発で、残りが営業・サービスを担当している。森社長は「景気の回復よりもさらに強い回復を経験している。日工会全体が十数%の受注の落ち込みを経験している中において、グループ全体として昨年並みの受注を確保している状態である」とした。また、生産については、「15,000台ほどのキャパシティを持っているが、今年は11,000台で終わるのではないかと見ている」と述べ、また、ドイツはほとんど残業をしないことを受け、日本でも働き方を変える意向があることを示し、「公的休暇について未使用の分は、未払いの労働債権であるから、社員と経営者で意識を変えて対応していく作業を行っている」とした。
本年5月、米ディーラー3社と統合に向けたLrtter of Intentを締結し、北米の新販売体制が実装完了となったことを説明した。これについて森社長は、「グローバル企業で直接お取引したいというお客様とは取引をするが、日本と同じく95%は販売店・ディーラー・商社経由で販売する。地域の文化に併せて販売網を広げる」と強調した。
現在同社では、様々なITの統合を進めている。例えば世界中どこにいても見積りを作成する仕組みや、CADの統合等を行っている。最近できたのは、「テクノロジーモニター」で、加工技術のデータベースを全世界のアプリケーションエンジニアが入力し、世界最大の加工に関するデータベースを構築している。
「われわれは毎月900台から1,000台の機械を売っているが、そこで得た知見を全て入力し、社内で共有し、コンサルティングファームとしてお客様に最適な加工に関するノウハウを提供していく」(森社長)
技術のトレンドをトーネス氏が説明をした。
「競争力のある分野に集中していくのが戦略」とトーネス氏。「ヨーロッパでは、5軸加工機に集中しているが、加えて新技術にも注力している」と話した。
この中で、「日本の開発技術者と協力してヨーロッパでは複合加工や研削加工を開発した」とし、「顧客の要望はどんどん変わっている。もっと柔軟でもっとたくさんの技術を融合した技術を欲しがっている。5軸加工機、複合加工機、研削加工機、全て融合した機械の需要が高くなっている。このような形でアプリケーションに帯する需要もどんどん幅広くなっている」とユーザーニーズについて説明し、「われわれは工作機械を提供するのではなくソリューションを提供したい」と話した。
なお、同社では、当日に来場できなかった方や、もう一度詳細情報を確認したいという方のために、興味のある機械をより詳しく調べられるよう、会場MAPから製品情報を探せるWEBサイトを開設している。
https://www.dmgmori.co.jp/iga2016/
ジーベックテクノロジーが「裏張りカッター&パス」を新発売
バリ取りの自動化を推進するジーベックテクノロジー(社長=住吉慶彦氏)が、6月22日(水)から1次穴径:2次穴径=1:1までの直交交差穴や、偏心交差・平面穴などに発生するバリを短時間で高品質に除去する「XEBEC裏バリカッター&パス」を発売する。
アプローチが不可能、プログラミングが困難、そんな理由で自動化をあきらめ、手作業で行っていた裏バリ取りに、「裏バリ取り」の常識を変えてくれるとして注目の新製品だ。
「XEBEC裏張りカッター&パス」は裏バリ取り専用に開発された球面カッターと、微分幾何学をバリ取りに応用し最適な工具軌跡を提供することで高品質なバリ取りが可能になるもの。最小穴径φ2mmから対応している。また、加工幅に合った切込量が演算され、均一な加工形状が得られる。変化するエッジ部の構成面角度に対し、常に2等分角方向に切り込む軌道で加工するため、バリ取りによる二次バリ発生を抑制する。
「XEBEC裏バリカッター&パス」の特長
●高 品 質 指定した加工幅に合った切込み量が演算され、均一な加工形状でバリ取り。
●短時間加工 高速輪郭加工でバリ取り。業界最速加工。
●長 寿 命 輪郭形状に沿った動作で、加工点を変化させ、切れ刃全体を使ってバリ取り。
■対象穴形状
直交交差・偏心交差時のドリル入り側のバリ、抜け側のバリ(裏バリ)に対応する。最小穴径はφ2mmから対応可能。
直交交差穴は、2次穴径がφ2mm以上で、1次穴径 : 2次穴径が1: 1 まで対応可能。
偏心交差穴は、2次穴径がφ2mm以上で、1次穴に対して破れ穴にならない偏心量まで対応可能。
▼詳細はコチラ▼
https://www.xebec-tech.co.jp/products/bbc.html
なお、この製品は、2016年6月22日(水)~24日(金) 東京ビックサイトで開催される『第20回機械要素技術展(M-Tech東京)』に初出展する。会場では、通常3万円する点群データを先着100名のお客様に無料でご提供するキャンペーンなども実施する。
アマダがファイバーレーザ(2kW・4kW)搭載 ブランク工程統合ソリューション「ACIES-AJ」シリーズを新発売
アマダ(社長=磯部 任氏)は、このほど自社製ファイバーレーザ(2kW・4kW)発振器を搭載した最新型ブランク工程統合ソリューションACIES-AJ シリーズを発売した。この製品は、これまでのCO2レーザ発振器を搭載したACIES シリーズに加え、昨今の市場からの要求である変種変量生産や、高品位加工への要求と低コストに対する顧客の要望に答えたファイバーレーザを搭載したシリーズである。
ACIES-AJ シリーズの主な特長
1.高生産性・低ランニングコスト
・CO2レーザマシンに比べて、クリーンカットでの薄板加工領域で、高速加工・ランニングコスト低減が可能(ファイバーレーザ発振器で2kW・4kWをラインナップ)。ファイバーレーザの特性である、高いビーム品質と集光点の密度を高めることで、高反射材の加工にも対応。
・発振器の消費電力はCO2 に比べて約1/3。
・パンチング・成形・タッピング加工とファイバーレーザ技術を統合したアマダ独自の「工程統合」により、加工全体のリードタイムを短縮し、変種変量生産に柔軟に対応。
2.安全性と作業性の両立
・作業者の安全性と作業性の確保、省スペースを実現するため、加工範囲をテーブルキャビンとシャッターで囲む新方式を採用したことで、従来機同様の運用方法による作業性を実現。
・第2原点を設定し、テーブルキャビンを開閉せずに材料のセットが可能。
3.高品質・高速加工
・切断加工はファイバーレーザ切断、成形やタッピングなどの加工は金型によるパンチング機構により、ブランク材の効率的な工程集約加工を実現。
・パンチング機構にはZR タレット、材料テーブルにはフルフラットブラシテーブルを採用。加工時には必要な台だけが昇降するため、上下成形加工・高ハイト成形加工の際にもキズレス加工を実現。
・パンチング金型の使用実績をID 情報でデジタル管理し、金型のセットミスやメンテナンス時期を知らせるだけではなく、摩耗を予測するなど「品質のデジタル管理」が可能。
4.イージーオペレーション
・アマダの最新型NC 装置 AMNC 3i を搭載。視認性が高い大画面をスマートフォン感覚で操作。図形タッチで加工条件の変更、NC で材料棚の操作、稼働実績の確認などユーザーのIoT 環境に幅広く対応。
5.長時間連続運転加工に対応
・レーザ加工中でも金型の自動交換が可能で、材料の自動供給とワークのテイクアウトによる仕分け作業など、材料自動供給装置とテイクアウトローダーとのシステムアップで充実した各種ソリューションを準備。
・新機能として長時間連続稼働に対応した「ノズルチェンジャー」、スクラップをプログラム終了時に自動搬出する「レーザスクラップ自動搬出」、カッティングプレートのブラシ部に付着したドロスを自動清掃する「カッティングプレート自動清掃」などにより、加工段取りを削減。
・「マシンを止めない自動化ソリューション」として、開発・設計段階からシステムを構築。
薄板切断加工や高速切断においてその効果を評価されるファイバーレーザだが、同社ではその優位性を最大限に生かすために、開発段階から「ブランク工程統合ソリューション」として進めている。
昨今の様々な業種から要求される加工製品の条件に応じるため、変種変量生産に素早く対応すると同時に、人手を介する作業(段取り)を極限まで減らしながら長時間連続稼で工程集約を実現したACIES シリーズ。マシンを止めることなく稼働率の最大化を実現することが可能である。
ジェイテクトが新構造のアンチクリープ玉軸受を開発
ジェイテクト(社長=安形哲夫氏)が、このほど主に自動車の変速機への使用を想定した新構造のアンチクリープ玉軸受を開発した。開発品は、クリープ(ハウジングに対して、外輪が回転してしまう現象)による摩耗に起因するハウジングや軸受の寿命低下対策として、従来一般的であった外輪厚肉化をすることなく、クリープを抑制することに成功した製品。自動車の変速機等の軽量化やコンパクト化に貢献する。
今後、CVTやHVなどの自動車変速機用軸受として自動車メーカーや変速機メーカーへ拡販を図るほか、クリープ抑制が求められる用途向けに広く展開していく。
自動車(特にCVTやHV)の変速機用玉軸受など、大きなラジアル荷重がかかる軸受には、外輪ひずみによるクリープ(ハウジングに対して、外輪が回転してしまう現象)が発生しやすいという特徴がある。クリープが発生すると、軸受とハウジングとの間で摩耗が進行し、軸の芯ずれや傾きが大きくなり、実機ユニットに不具合が生じる恐れが懸念される。外輪ひずみによるクリープ対策としては、外輪の厚肉化が一般的だが、軸受のサイズアップによる実機ユニットの大型化や重量増加といった問題があることを受け、今回、外輪の外径中央部に極浅い溝を設ける構造を世界で初めて採用し、玉と外輪軌道の接点から外輪外径とハウジングとの接触部までの距離を外輪厚肉化製品と同等とすることで、外輪肉厚を35%アップした場合と同水準のクリープ抑制を可能とし、上記問題点を解消した。
この開発により従来のような外輪の厚肉化が不要となった結果、自動車の変速機等の軽量化・コンパクト化が可能となった。
特長は以下の通り。
①外輪ひずみによるクリープに対して、今回開発品の構造・形状による対策は世界初(※同社調べ)。
②外輪肉厚35%アップと同等のクリープ抑制効果(例:ハウジング摩耗量を50%低減)。
③従来品との置き換えにより、変速機等の軽量化・コンパクト化に貢献。
タンガロイがヘッド交換式ドリル『DrillMeister』(ドリルマイスター)L/D=12を拡充
タンガロイ(社長=木下聡氏)は、このほどヘッド交換式ドリル『DrillMeister』(ドリルマイスター)に従来の最大L/D = 8 ボディのラインナップに加えて、L/D = 12 ボディの発売を開始した。
『DrillMeister』は、独自の自己拘束型クランプシステムの採用により、簡単で迅速なヘッド交換を可能にしている。工具交換はヘッドを付け替えるのみで、ツールホルダからのドリルボディの脱着や突出し量の調整が不要となることから、工具交換時間を大幅に短縮できる。また、ヘッドは小さな力で取付け・取り外しができ、必要に応じて機上での交換も可能。今回拡充を行うL/D = 12 は、工具径φ12.0〜22.9 mm に対応し、シャフトや熱交換器の穴加工等の深穴加工で、抜群の性能を発揮するヘッド交換式ドリル。ボディには強ねじれ溝を採用し、さらに溝面に特殊な磨き処理を施すことで、安定した切りくず排出性を実現している。これによって、特に切りくず排出が難しくなる深穴加工時に、抜群の切りくず排出性能を発揮する。
『DrillMeister』は、加工能率の向上だけでなく、工具交換時間の大幅短縮、再研削にかかわる費用を0 にできるなど、トータルの加工コスト削減に大きく貢献する。
主な特長は以下のとおり。
●工具径:φ12.0~22.9 mm(0.1mm 飛び)、加工深さ: L/D = 12。
●強ねじれ溝と特殊な磨き処理の採用で、抜群の切りくず排出性能を発揮。
●独自の自己拘束型クランプシステムが、簡単かつ迅速なヘッド交換を実現。
●本体部分の変形が少ないクランプ機構により、ヘッドの交換可能回数を大幅に増加。
●マージン部を持つ加工ヘッドによって、ソリッドドリルと同等の加工穴精度を実現。
●再研削が不要で、再研削コスト、予備工具の在庫削減等、工具管理も容易。