ニュース
日本機械工具工業会 2025年2月分 会員統計生産額まとまる
日本機械工具工業会がこのほどまとめた2025年2月分の機械工具生産額は次のとおり。〈( )内は対前年比〉。■生産額 切削工具 353.1億円(103%)、耐摩耗工具 30.8億円(98%)、総合計 390.8億円(102%)。■ドリル生産額 特殊鋼工具 11.2億円(79%)、超硬工具 37.5億円(100%)、ダイヤ・CBN 1.1億円(121%)、総合計 49.8億円(95%)。■エンドミル生産額 特殊鋼工具 4.8億円(121%)、超硬工具 38億円(111%)、ダイヤ・CBN 1.3億円(113%)、総合計 44.2億円(112%)。■カッタ生産額 特殊鋼工具 1.4億円(152%)、超硬工具 5.2億円(106%)、ダイヤ・CBN 0.4億円(82%)、総合計 6.9億円(111%)。■ギヤカッタ生産額 総合計 5.3億円(74%)。■ブローチ生産額 総合計 7.2億円(98%)。■ねじ加工工具生産額 特殊鋼工具 31.3億円(99%)、超硬工具 3.3億円(98%)、総合計 34.6億円(99%)。■バイト生産額 特殊鋼工具 0.1億円(127%)、超硬工具 7.8億円(91%)、総合計 7.9億円(92%)。■リーマ生産額 特殊鋼工具 1億円(96%)、超硬工具 2.4億円(120%)、総合計 3.4億円(112%)。■鋸刃カッタ生産額 特殊鋼工具 1.2億円(94%)、超硬工具 0.5億円(97%)、総合計 1.7億円(95%)。■インサート生産額 超硬工具 143.9億円(108%)、ダイヤ・CBN 19.6億円(102%)、総合計 163.5億円(107%)。■ボディ関係生産額 総合計 15.5億円(99%)。■超硬合金生産額 切削用 120.3億円(104%)、耐摩耐触用 14.7億円(93%)、総合計 136.6億円(103%)。
岡本工作機械製作所 代理店を対象に「2024年度PSG会 支部連絡会」を大阪・名古屋・東京で開く
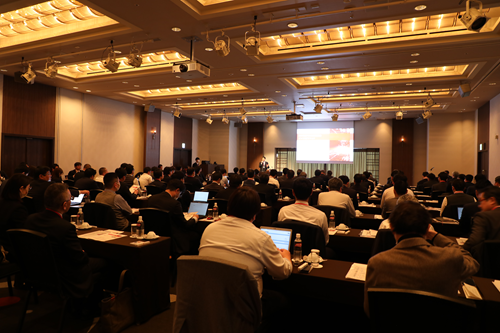
岡本工作機械製作所(社長=石井常路氏、本社:群馬県安中市)は、去る2月18日に新大阪江坂東急REIホテル(西部支部)、同19日にメルパルク名古屋(中部支部)、同20日にベイサイドホテルアジュール竹芝(東部支部)で「PSG会 支部連絡会」を開いた。
(取材は東部支部)
アフターサービスの強化に注力
江連 営業本部東日本統括部長が日頃の感謝の意を表したあと、同社の概要について説明をした。それによると、同社の機械が納入している業種について、「一番多いのは産業機械装置向け、続いて自動車関連(EV)、半導体関連の順になっている。」と説明したあと、複合研削盤の伸び率が大きくなっている。脆性材向けの複合研削盤の受注がある。脆性材はガラス、セラミックス等の関係で伸びている。」と話した。
また、汎用の平面研削盤のシェアをさらに伸ばしていくとしたうえで、「重要なことは、アフターサービスの対応である。まず、サービス員の増員を図るため施策を始めている。現状は10拠点でサービス員を45名体制まで持っていくことができた。また、サービス員のスキルや様々な経験が重要になってくる。また、サービスパーツの即納率を上げるため、現在安中工場の中に自動走行システムを建設中である。これまで以上にアフターサービスに注力していく方針だ。」と力を込めた。
次に2025年度の受注予想について、「春以降にはV字回復をするということを想定して種まきを現在行っている。好調業種である半導体、EV関連、脆性材加工向けのユーザーへアプローチをする。また、SDGsを見据えた環境対応、自動化、省人化等、付加価値のある製品の提案をしていきたい。主力製品である平面研削盤のシェアアップ、また新型機種を導入することによって新たな市場を開拓しようと考えている。アフターサービス強化に注力をして、部品即納率のアップ、ダウンタイムを減らすことを考えながら行動をしていく。弊社は2015年より研削革命を目標にさまざまな提案を行ってきた。高効率研削、機上計測、自動化、複合化、周辺機器メーカーとのタイアップ、これも含めて今後も引き続き研削革命を行っていきたいと考えている。」と意気込みを示したあと、協力を要請した。
加工のトレンドを押さえた「省エネ」「自動化」「超精密」の3つの柱
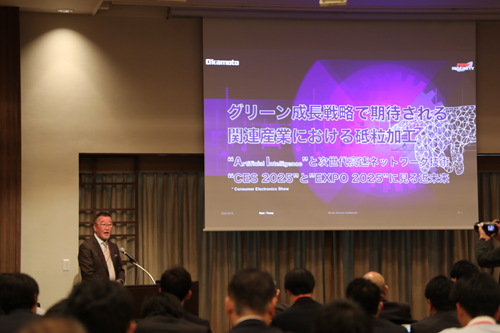
今回のPSG会では、「省エネ」「自動化」「超精密」の3つのトピックスを柱に好調業種に向け、どのような機械を提案し、どのような機能を盛り込むかを含めた説明がされた。
「省エネ」では、同社の省エネ研削盤シリーズが紹介された。省エネ補助金(一定の省エネルギー効果がある取り組みに要する経費を補助することで各分野の省エネルギー化を推進し、内外の経済的社会環境に応じた安定的かつ適切なエネルギー需要構造の構築を図ることを目的とした補助金)についても触れ、予算が2,000億円から7,000億円へ増額が予定されることを受け、設備更新をする際に省エネが重要になることから、今回は同社の補助金対象モデルの油圧レス、省エネ研削盤、CNC成形研削盤「HPG500」シリーズが紹介された。
この機種は①汎用モデル、②CNCモデル、③高速反転モデルとユーザーニーズに応じて機種が選択可能。注目する点は、作動油削減でメンテナンス性を向上したこと。消費電力を50%以上のコストカットに成功している。また、廃油を無くして、CO2排出を年199.2kgも削減。しかも、研削加工の大敵である発熱抑制で高精度研削を可能にしている。
また、同社のベストセラー機「PSG-SA1」シリーズでは、省エネ用のオプションを実装。機上計測ユニットの「Quick Touch」で工程集約を実現した。また、余分な電力をOFFする〝省エネモード〟を新オプションとして実装を開始したことで、油圧モーターがテーブル駆動時以外オフすることで、電気代などのランニングコストを削減、省エネ補助金対策にも有用であることを説明した。
次に「自動化ソリューション」について説明をした。同社では「研削盤の自動化を行う場合、どの工程を希望するか」のユーザーアンケートを実施しており、それによると、3大希望は、ワーク脱着を含む自動化が29%、ドレス作業22%、加工開始点20%だったことから、動画で「UPZ-Li」シリーズでは協働ロボットによる砥石交換や、複雑形状のワークを自動で超精密仕上げをする様子、また、ロータリー平面研削盤のロボット仕様「PRG-iQ」では需要が増えつつあるプレート加工も自動化する様子などが動画により説明された。同社では、ロボットを用いた自動化ライン構築も提案可能だ。
続いて「超精密加工ソリューション」では、高精度加工が必要なEV関係製品を例にとり、同社の超精密研削盤ラインナップが紹介された。それによると、①大型ワークを対象とした「UPG-CHLi」シリーズの加工例としてモーターコア順送金型やスロットダイの研削加工、工作機械部品加工の様子、②中型加工ワークを対象にした「UPG-CA-iQ(Li)シリーズではレンズ金型が、③小型ワークを対象にした「UPZ210Li」シリーズでは電子部品のコネクタ金型の加工などがそれぞれ動画を用いて説明され、いずれも加工のトレンドを押さえた内容だった。
PSG会での目玉のひとつである特別講演では、「グリーン成長戦略で期待される関連産業における砥粒加工 〝Artificial Intelligence〟と次世代高速ネットワーク技術 〝CES2025〟と〝EXPO2025〟に見る近未来」をテーマに伊藤常務が講演をした。
講演はアメリカの状況からはじまり、米国がコンピュータや半導体など他国への依存度が高い点から日本企業にもチャンスがあるという見方があるとして、成長戦略について様々な例をとって分かりやすく説明をした。また、近年のトレンドである生成AIチップの必要な性能や、今後グリーン成長戦略を支える技術などについても詳しい話がなされ、会場内の聴講者は熱心にメモを取る様子が見られた。
「1年前倒しで目標を達成」
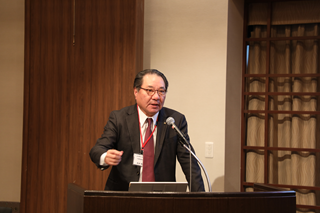
石井社長があいさつに立った。この中で石井社長は、「過去3カ年計画を繰り返してきたが、全中期経営計画の〝ソリューション2025〟の売上目標500億円、営業利益は60億円を目標にして本年3月に目標を達成しようと2022年から実行してきたが、お陰様で2024年3月に1年前倒しで目標を達成できた。これも皆様方のお陰である。」とお礼を述べたあと、「昨年4月から2028年3月期、当社にしては珍しく4カ年計画になるが売上690億円、営業利益110億円を目指した新4カ年計画〝INOFINITY700〟を発表し、現在実行中である。この中継は2030年の3月期に目指す姿として発表した〝ビジョン2030〟を見据えた中計になっている。INOFINITYは造語であり、革新という意味のInnovation、無限という意味のInfinityの言葉を掛け合わせてINOFINITYという言葉をつくった。研磨、研削の可能性を無限に追及し、進化した革新的な研削ソリューションを提供していく会社になりたいという意味を込めてINOFINITY 700という中計の名前とした。」と力強く思いを述べた。
また、海外の研削盤製造拠点の拡大についても触れ、「中国常州工場では年間400台の平面研削盤を製造するキャパを持つ工場が稼働し、中国市場の拡販に貢献している。また、販売面では海外拠点についても成長著しいインドマーケットをターゲットに、インド、プネに販売子会社を2021年に設立した。当社にとって最も戦略性が高い北米は、当社100%子会社のOkamoto CorporationがEllison Technologies社と昨年9月に販売強化に向けた覚書を締結している。工作機械は、高付加価値製品の米国での販売強化、半導体製造装置は、SiC等の化合物半導体の顧客開拓を進めていく。」と説明し、半導体製造事業については、「新幹線や幹線道路が近くにある埼玉県さいたま市大宮に用地を取得し、今年10月には技術開発とショールームを展開することでテスト加工活動の工場、またエンジニアの採用面でも有利な活用ができると考えている。半導体製造装置の集積地である九州には、2023年5月に伊万里市にパーツ対応やメンテナンスを担当する九州テクニカルサポートセンターを開設し、半導体分野での自動化に実績を持つプレシード社に資本出資を行った。23年11月には宮崎県都城市の大和工機を完全子会社化した。大和工機においては、大型のクリーンルームを備え、半導体関連の大型の装置の生産が可能であることにより、本社工場、大宮のショールーム、九州の拠点で弊社、岡本工作機械の半導体事業を拡充していく。」と意気込みを示した。
1935年創立の同社は、2030年には世界に類のない砥粒加工機、総合砥粒加工メーカーとして平面研削盤、半導体ウエハー研磨装置でグローバルナンバーワンを目指すという長期ビジョンを掲げており、本年90年を迎える。今後もサステナブル経営を推進し100年企業を目指す方針だ。
親睦を深める懇親会では、ゲームなどの企画もあり、参加者は大いに楽しみながら懇親を深め、宴たけなわの頃、散会した。
三菱マテリアル 「DIAEDGE突っ切り大作戦」キャンペーン実施中 ~2025年3月31日まで~
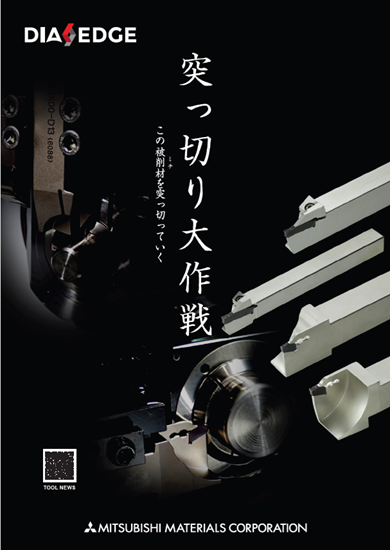
三菱マテリアル 加工事業カンパニーが「DIAEDGE突っ切り大作戦」キャンペーン実施中。対象製品は、溝入れ突切り旋削工具「GY/GWシリーズ」(モジュラータイプは対象外)。
対象製品の専用インサートを30個講中で一体型ホルダを無償で提供する。
↓最新情報・問い合わせ先↓
https://www.mmc-carbide.com/
MOLDINO 2商品を発売
MOLDINOがこのほど、①高能率加工用コーナRエンドミル エポックターボミル(ペンシルネック)「ETMP-TH」にフリーネックタイプを追加、②高硬度鋼加工用ボールエンドミル IXエポックディープボール-TH3「IX-EPDB-TH3」の2商品を発売した。
高能率加工用コーナRエンドミル エポックターボミル(ペンシルネック)「ETMP-TH」にフリーネックタイプを ~ビビり振動を抑える工具形状と把持量の調整で深部の高能率切削が可能に!~
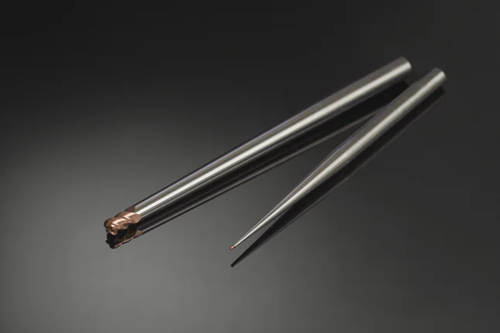
近年、アルミダイカスト等の鋳造型においてギガキャストに代表される大型金型の開発が進んでいることを背景にさらなる深彫り加工の要求が高まっている。
同社によると、「この状況下、加工現場では〝工具とワークが干渉しない様にストレートネックの工具を使用する〟、〝ホルダーに干渉しない様に工具の突き出しを無駄に長くする〟など、干渉を気にすることの無い状態で工具を使用される場合が多い。弊社はペンシルネックタイプの工具を使用することを推奨していますが、加工能率の低下や、工具の種類が膨大になり工具管理面で苦労されているユーザーも存在します。」としており、この課題に対する解決の手段として、同社では工具の干渉リスクを低減し、かつ工具集約を実現する“フリーネック形状”に着目した、仕上げ領域に適用するペンシルネックボールエンドミル(EPDBPEATH)のフリーネックタイプをすでに昨年2月に先行して発売していたが、現場からは荒から中仕上げ領域の加工能率を向上できる工具の要望が多かったため、このほど高能率荒加工で定評のあるエポックターボミルペンシルネック(ETMP-TH)のフリーネックタイプを追加し発売した。
また、先行発売した刃先交換式工具用のモジュラーミル専用超硬シャンクと併せ、大型金型に対するトータルソリューションへの対応を加速させていく方針。
〈特長とメリット〉
(1)金型製造の納期短縮の要請に応える高能率加工用コーナRエンドミル。
(2)オーバル形状の刃径断面を持ち、特にコーナー部の加工でビビり振動が抑えられ、安定した高能率な切削を実現。
(3)コーナ刃に高剛性形状を採用しており、1刃送り量の大きな高送り加工が可能。
*以下はフリーネックタイプについて*
(4) 首部に段差がないので壁面への干渉リスクが低減される。
(5)工具が加工部に届かない時に突き出し量を調整できる。
(6)把持量の調整で様々な加工深さに対応できますので工具の集約が可能。
■推奨できる加工用途
・エポックターボミル:各種金型の高能率荒加工
・フリーネックタイプ:金型深部の高能率荒加工と工程集約
■仕様
・エポックターボミル(ペンシルネック):Φ1~Φ16(60アイテム)
・内 フリーネックタイプ:Φ1~Φ10(39アイテム)
■価格
¥18,280~¥171,620(消費税別)
高硬度鋼加工用ボールエンドミル IXエポックディープボール-TH3「IX-EPDB-TH3」 ~60HRCクラスの高硬度鋼加工で工具寿命が大幅に向上!~
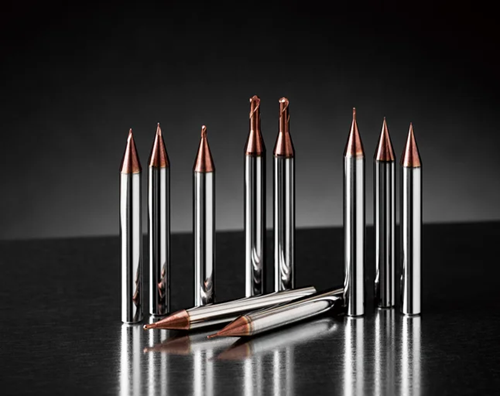
金型の「高機能化」「高性能化」に伴い、金型材料は高硬度化による難削化が進む一方で、精密金型に求められる加工精度も年々厳しさを増している一方、高硬度鋼の加工では工具摩耗が激しく、ワークの削り残り量が多くなるため、加工精度の向上が課題となっている。
この課題解消を目的としてMOLDINOは、高硬度鋼加工用ボールエンドミルIXエポックディープボール-TH3「IX-EPDB-TH3」をこのほど発売、同商品は、新開発した〝超々微粒超硬素材〟を採用している。次世代添加元素を加えることで、従来の超硬を超える耐摩耗性(硬さ)と耐欠損性(靭性)の両立に成功した。また、この新素材に最適化した刃形設計により、高硬度鋼の長寿命かつ高精度な加工を実現している。
〈特長とメリット〉
(1)新開発の超々微粒超硬合金の採用により、高硬度鋼加工における耐摩耗性と耐欠損性を高次元で両立した。
(2)特に60HRCクラスの高硬度鋼加工で工具寿命が従来の整数倍に向上するため、高価格なcBN工具からの置き換えにも期待できる。
(3)焼き嵌めホルダに最適なショートシャンク設計。
(4)外径実測値をラベルに表記した。測定の手間なく実測値をCAMに反映でき、加工精度の向上が狙える。
■推奨できる加工用途
小型精密金型(高硬度鋼)の荒~仕上げ加工
■仕様
Φ0.1~Φ2.5(全106アイテム)
■価格
¥6,950~¥9,520(消費税別)
アマダプレスシステム 15軸制御 ワイヤ回転式トーションマシン「LM-26A」を販売開始 ~独自のダブルスウィング軸により加工領域を拡大~
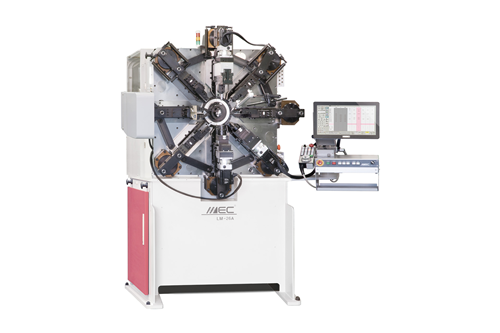
アマダプレスシステムは、このほどワイヤ回転機構と8本の加工スライドで、直感的な操作を実現する15軸制御ワイヤ回転式トーションマシン「LM-26A」の販売を3月11日から開始した。
トーションマシンは、ねじりばねを得意としながら引きばね、圧縮ばね、フォーミングなど、あらゆる線加工の成形が可能なばね成形機で、新商品の「LM-26A」は、2023年に発売した対応線径違いの「LM-16A」と同様に、加工スライドを4軸ずつ上下に分けて、スライドの横移動を数値制御するダブルスウィング軸を搭載している。
これにより、これまで難しいとされていた複雑形状の加工など、加工領域が拡大するうえ、さらに、プログラムによる高い再現性により、段取り時間の短縮や作業軽減につながり、生産性が向上した。
また、従来機のTM-20Mと比べ、より太線の加工を可能としながら設置面積は同等の省スペース化を実現した。
同社では、「近年、モノづくりの現場では品質や生産性向上の要求のみならず、少子高齢化や熟練技能者の引退などの人手不足を背景に、自動化や段取りの簡易化に対するニーズも高まっている。このような課題に対し『LM-26A』は、独自のばね成形専用プログラム『MNO2』によるプログラム作成の簡易化や生産状況の見える化のほか、多彩な機能を通じて解決し、高効率生産をサポートします。」と意気込みを示している。
主な特長
(1)高精度加工の実現
2連フィードローラユニットの採用により、ワイヤにかかるフィード圧の負荷を軽減し、安定したワイヤ送りが可能になった。さらに、高い分解能のサーボモーター制御により、精密な動作が可能になり、高精度加工を実現。加えて、全スライドがセンサーとして使用できるモーターセンサーシステムにより、巻き角度、コイルの自由長などを1000分の1mm単位で計測できる。結果は表やグラフで表示され、各軸の修正が可能。
(2)加工時間の短縮と段取り削減による生産性の向上
高速回転のロータリーサーボスライドが曲げ加工の時間を短縮する。スピナツールは、コンパクトでありながら軸ピンと外ピンの間隔調整が可能なため、線径ごとのピンの交換作業が不要。これにより、交換時の打ち直しや焼き入れの作業を削減でき、段取り時間とランニングコストを削減する。
(3)独自開発のプログラムによる操作性の向上
ばね成形機専用プログラム「MNO2」は、プログラムの流れや各軸の動作状況、入出力、ジャンプ項目などが一目で把握できる。ナビシステム機能とタッチパネル仕様より、操作性が大幅に向上し、簡単にプログラムを作成でき、段取り時間を短縮できる。また、IoTへの対応として、マシンの稼働状況をスマートフォン、PCなどで監視でき、予防保全機能による定期的なメンテナンスで生産効率の向上に貢献する。
(4)加工ニーズに合ったソリューションを提案
スライドが最大200mm前方に動く「3Dスライドユニット」、干渉回避に有効なワイヤ切断後の加工を可能にする「エアグリップユニット」、コイルの外径調整をサーボモーターで行う「外径サーボユニット」、コイル長さを計測する「静電容量センサーユニット」など、後工程や計測など様々なニーズに合わせ、豊富なオプションユニットを取りそろえている。
仕様
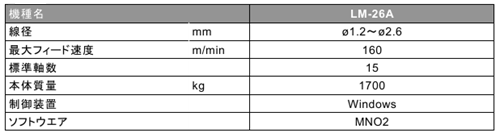
DMG森精機 「健康経営銘柄」に2年連続、「健康経営優良法人 ~ホワイト500~」に3年連続で認定

DMG森精機は、このほど健康経営に優れた上場企業として昨年に続き2年連続で、経済産業省と東京証券取引所による「健康経営銘柄2025」に選定された。同銘柄は社員等の健康管理を経営的な視点で考え、戦略的に取り組んでいる企業を選定するもの。また、経済産業省と日本健康会議により3年連続で、特に優良な健康経営を実践している法人を顕彰する「健康経営優良法人2025」の大規模法人部門「ホワイト500」にも認定された。
現在、会社の安定した事業運営と持続的な発展成長にとって、社員が心身ともに健康であることは必要不可欠とされているが、同社は、2018年に12時間勤務間インターバルを義務化、2019年に全社員に人間ドック方式の各種がん検診を含めた健康診断を個人負担額なく導入、2020年に敷地内全面禁煙化を実現し、さらに健康管理増進センターを設立した。
2021年に「DMG森精機 健康経営宣言」を発表し、順次、社内健康データの見える化、ラインケアのヘルスリテラシー向上を目的とした管理職のためのWebinar研修の開始、要二次健診者の追跡や服薬アドヒアランスの確認、40歳未満有所見者に対する保健指導、運動・栄養教室の開催などを継続して実施している。
最近では、血圧対策と食生活の見直しの啓発のための「毎月17日は社内昼食の全メニュー減塩デー」を開始、「女性の健康とワーク・ライフバランスに関する実態調査」に基づき「生理休暇」日を有給化、介護離職者予防の取組みも始めるなど、より組織的で系統的な取り組みを展開している。また、世界各国の拠点事業所で栄養バランスのとれた昼食を提供している。
同社では今後も経営理念に掲げる「よく遊び、よく学び、よく働く」を体現する社員の意欲的な働きに期待するとともに、会社をあげて組織的な健康増進施策を推進することにより、社員が高いワーク・エンゲイジメントを持ちながら、健康に個々の能力を発揮できるよう取り組んでいく方針。
フジムラ製作所 「最新ベンディングロボットシステム」など最新マシンを導入
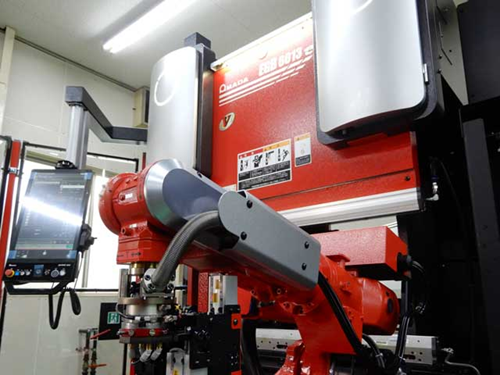
国内最先端の「デジタル板金」を進める、フジムラ製作所は、このほど最新設備としてアマダ製「全自動曲げ加工システム EGB-6013ARce」と「自動金型交換装置付き 最新ベンディングマシン EGB-6020ATCe」を導入したと発表した。「EGB-6013ARce」は、埼玉県内で初の導入となり、3月中旬から本格的に稼働を開始する。
「EGB-6013ARce」は、少量多品種生産が中心だった受注に加えて、最近は量産品などの取引先が増加してきたことで、これに伴う生産体制を強化するために第一工場に導入した。特に小物製品の加工に最適なシステムであり、小物曲げ製品は突き当てが難しい形状のものや、小物曲げ加工時に危険が伴う場合があることから、作業者の安全面を考慮して人的負荷を軽減する狙い。
可搬重量10kgで人間の可動域に近い自由度を持つ「6軸多関節ロボット」と、加工製品に合わせて自動でグリッパーを交換する「オートグリッパーチェンジャー(AGC)」、さらに最大27種類の金型を搭載し自動で金型交換を行う「ツールストッカー」を最新式のコントローラーとタブレットを連携させてオペレーションすることが可能となっている。さらに材料のセットや加工後の製品を搬出するコンベヤー装置などにはセンシング技術を用いており、経験の少ない現場オペレーターにも扱いやすいシステムで構成されているのが特徴。
同社としてはベンディングロボットの導入は初めてとなるが、これはベンディング工程の自動化を含む板金加工体制を、発注先の業種や要望に合わせて適時、再構築を図る必要があると考えていることと、社員全員のロボット(自動化)への意識を高め、「実際に使うことによって、その便利さを現場作業者にきちんと理解してもらいたい」という狙い。今回の導入により、工場内の自動化とデジタル化の一体感を高め、一層のDX 化を図っていく方針。
「ベンディングロボット EGB-6013ARce」 基本システム概要
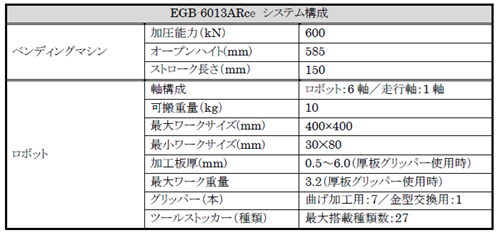
また、第四工場に導入した「EGB-6020ATCe」は、これまでも導入実績のあるベンディングマシン用ATC(自動金型交換装置)を搭載した最新小型曲げ加工マシンとなる。ベンディングマシンの金型交換は重量作業であると同時に金型の取付ミスなどのリスクがあることと、経験の少ない作業者には負担が大きい作業であり、金型ストッカーからの取出し・収納といった時間がかかる。
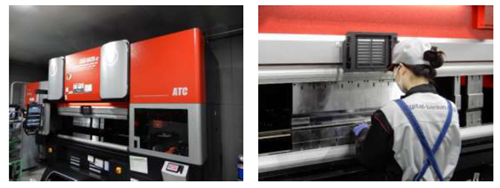
フジムラ製作所では、これまでも大型ベンディングマシンなどではATC付のマシンを導入しており、その効果を高く評価してきた。
同社では、「今回は、10ロット以下の小物製品の加工においても効果があると考え、導入に至りました。また、ATC の効果は安全と正確さだけに留まらず、曲げオペレーターに女性が増えていることや、外国人オペレーターにとっても安全性と作業性を両立させた利便性の高いシステムとして期待しています。」とコメントしている。
「自働金型交換装置搭載ベンディングマシン EGB-6013ATCe」 基本システム概要
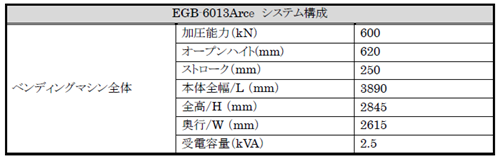
日立建機 使用済みの作動油を再生する技術を開発
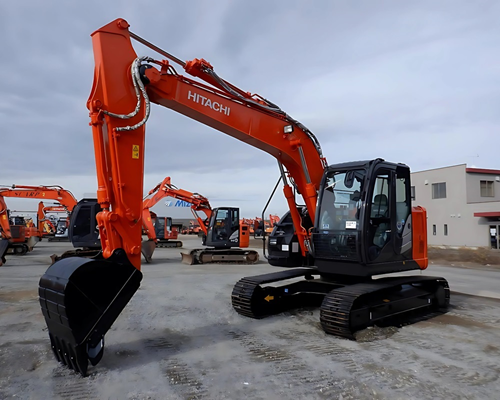
日立建機は、このほどサーキュラー・エコノミー(資源循環型経済)の実現に貢献する取り組みの一環として、使用済みの作動油を再生する技術を開発したと発表した。
同社は、再生した作動油を用いた中型油圧ショベルZX135US-5B(13tクラス)1台を、メーカー保証付き中古車としてこのほど日本で販売した。今後も日本で再生する油圧ショベルには本技術を適用し、作動油を含めて車体全体を再生していく計画。
日立建機グループは長年にわたり、顧客の使用済み純正部品を新品同等に再生して市場に供給している。また、2021年からは油圧ショベルなど建設機械の車体本体の再生にも取り組んでいる。今回は、稼働時間3,200時間以上の中型油圧ショベルZX135US-5Bを新車同等の性能まで再生し、さらには再生した作動油を用いて再び中古車として市場に供給する。再生した作動油を中古車に用いて商用化するのは、日立建機にとって今回が初めて。
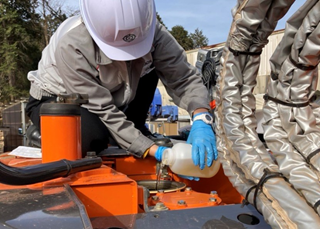
油圧ショベルを動かす血液のような役割を果たす作動油は、油圧ショベルの長時間の稼働に伴い、異物混入、熱による成分変化、酸化などで劣化するため、定期的に作動油を抜き取り新しい作動油に交換する必要がある。同グループはこれまで、作動油の長寿命化をめざし、添加剤の投入などによる研究開発に取り組んできたが、今回、専用装置を使用して不純物や汚染物質を取り除く浄油方法と添加剤の投入を組み合わせることで、作動油を交換することなく、動粘度や酸化の度合いなど日立建機が定める品質基準まで再生する技術を開発した。また、再生した作動油を用いた油圧ショベルが正常に稼働することも確認している。この技術により、作動油の交換作業の負荷も軽減され、効率的な機械の再生が可能になった。
なお、13tクラスの中型油圧ショベルには125リットルの作動油が使用されており、この作動油の生産には、一般的にその数十~100倍に相当する原油が必要とされる。したがって、13tクラスの中型油圧ショベルに使用される作動油の生産には、約1万リットルの原油が消費されると推定される。使用済みの作動油を再生することで、原材料である原油の消費を低減することができる。
2025年1月分工作機械受注総額は1161.5億円
日本工作機械工業会がこのほどまとめた2025年1月分の受注実績は以下の通り。
2025年1月分工作機械受注総額は、1,161.5億円(前月比△18.8% 前年同月比+4.7%)となった。受注総額は、内外需共2割弱の前月比減少で2カ月ぶりの1200億円割れ。前年同月とほぼ同水準で総じて横ばい圏内の動き。
内需は320.0億円(前月比△19.9% 前年同月比+4.6%)で、年末年始の営業日減や補助金待ち等の影響もあって、2カ月ぶりの350億円割れ。主要業種を中心に勢いは依然弱く、底這い状態。
外需は841.5億円(前月比△18.4% 前年同月比+4.7%)で、2カ月ぶりの850億円割れ。前月の反動減もあるが、欧州は弱含み。一方、アジアは中国やインドを中心に堅調持続。
1月の受注はほぼ前年並みの受注も受注業種や国・地域に違いが見られ、まだら模様の状況。今後の動向を注視。
1月分内需
320.0億円(前月比△19.9% 前年同月比+4.6%)。
・2カ月ぶりの350億円割れ。
・前月比3カ月ぶり減少。前年同月比3カ月連続増加。
・営業日減や補助金待ち等の影響もあって、前月比減少も総じて横ばい圏内の動き。
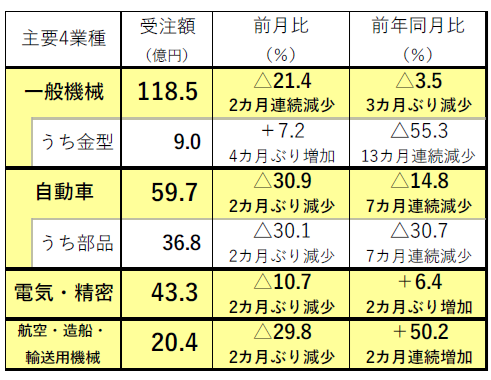
(出所:日本工作機械工業会)
1月分外需
841.5億円(前月比△18.4% 前年同月比+4.7%)
・2カ月ぶり850億円割れ。
・前月比2カ月ぶり減少。前年同月比4カ月連続増加。
・季節要因で前月の反動減が見られたが、状況に大きな変化は見られず。
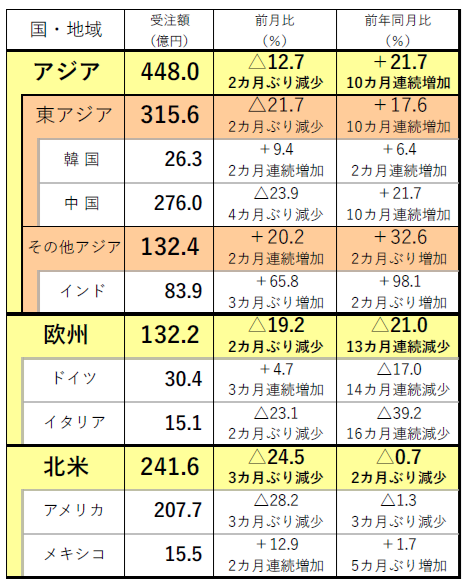
(出所:日本工作機械工業会)
日本機械工具工業会 2025年1月分 会員統計生産額まとまる
日本機械工具工業会がこのほどまとめた2025年1月分の機械工具生産額は次のとおり。〈( )内は対前年比〉。■生産額 切削工具 347.4億円(106%)、耐摩耗工具 29.9億円(102%)、総合計 385.8億円(106%)。■ドリル生産額 特殊鋼工具 11.9億円(90%)、超硬工具 35.9億円(103%)、ダイヤ・CBN 0.8億円(96%)、総合計 48.7億円(100%)。■エンドミル生産額 特殊鋼工具 4.6億円(125%)、超硬工具 33.7億円(111%)、ダイヤ・CBN 1.2億円(120%)、総合計 39.6億円(113%)。■カッタ生産額 特殊鋼工具 1.4億円(182%)、超硬工具 5.2億円(112%)、ダイヤ・CBN 0.5億円(131%)、総合計 7.1億円(123%)。■ギヤカッタ生産額 総合計 5.5億円(82%)。■ブローチ生産額 総合計 7.2億円(103%)。■ねじ加工工具生産額 特殊鋼工具 30.6億円(100%)、超硬工具 3.1億円(102%)、総合計 33.7億円(100%)。■バイト生産額 特殊鋼工具 0.1億円(83%)、超硬工具 7.6億円(93%)、総合計 7.7億円(93%)。■リーマ生産額 特殊鋼工具 1億円(105%)、超硬工具 1.9億円(103%)、総合計 3億円(104%)。■鋸刃カッタ生産額 特殊鋼工具 1.3億円(101%)、超硬工具 0.4億円(108%)、総合計 1.7億円(103%)。■インサート生産額 超硬工具 144.7億円(110%)、ダイヤ・CBN 20.2億円(105%)、総合計 164.9億円(110%)。■ボディ関係生産額 総合計 15.2億円(105%)。■超硬合金生産額 切削用 117.7億円(106%)、耐摩耐触用 14.9億円(112%)、総合計 134.4億円(107%)。