ニュース
セスクワが「WorkNC V22 Ver.アップセミナー」開催
セスクワでは、年内リリースへ向けて進めている、WorkNCの新バージョン『WorkNC V22バージョンアップセミナー』を開催する。東京会場開催をかわきりに、全11会場にて開催を予定している。なお、東京会場では、セミナー後に懇親会の開催も予定している。参加希望者はWEB申込みページより直接お申込むか、電話またはEメールで連絡すること。詳細はコチラをクリック↓http://www.sescoi.co.jp/corporate/news/seminar-info/2013-14/ ●開催日程・会場▼2013年 12月18日(水) 東京(丸の内) トラストシティカンファレンス・丸の内 ▼2014年 1月22日(水) 広島(広島) RCC文化センター 1月23日(木) 大阪(梅田) 梅田センタービル 1月24日(金) 愛知(名古屋) 名古屋国際会議場 1月29日(水) 福島(郡山) 郡山商工会議所 1月30日(木) 埼玉(大宮) 大宮ソニックシティ 1月31日(金) 群馬(太田) 東毛産業技術センター 2月6日(木) 富山(富山) 富山総合情報センター 2月7日(金) 新潟(燕三条) 燕三条地場産センター 2月13日(木) 静岡(新富士) ふじさんめっせ 2月14日(金) 静岡(浜松) アクトシティ浜松 【内容】 ・新バージョン「WorkNC V22」 -WorkNC V22全体概要説明 -2.5軸/3軸の新規追加変更点の説明 -新マシンシミュレーション(マシンコンテキスト)説明 -固定サイクルの機能強化点の説明 -新標準5軸加工ツールパス説明 ・データ・デザイン社(弊社東海地区代理店)セミナー ※大阪会場を除く10会場
ゼネテックが産業用ロボットオフラインティーチングシステム「Robotmaster」でダイヘン社製ロボットのサポートを開始
ゼネテック(社長=上野憲二氏)が、このほど3次元CAD/CAMシステム「Mastecam」上で動作する産業用ロボットオフラインティーチングシステム「Robotmaster」においてダイヘン社ロボットのサポートを開始した。
「Roobtmaster」とはMastercamの多彩なツールパス作成機能を利用し、各種産業用ロボットの動作プログラムを作成するMastercamベースの次世代型オフラインティーチングシステム。初心者でも扱える直感的な操作性により、ロボットの動作プログラムの出力はもちろんのこと、ティーチングペンダントによるオンラインティーチングでは困難なワークや周辺構造物との干渉やリミットオーバーの検出・修正もすべてRobotmaster上で簡単に行うことができる。さらにこの製品はCAD/CAMをベースとしたオフラインティーチングシステムのため、一度作成した動作プログラムの臨機応変な変更や再利用も用意に行うことができ、断続的な工程改善に取り組めるといった効果も期待できる。
10月分工作機械受注総額は1022.1億円 日工会
日本工作機械工業会がまとめた10月分の受注実績は以下の通り。2013年月10月分工作機械受注総額は、1022.1億円(前月比+1.5%・前年同月比+8.4%)となった。受注総額は2カ月連続の1000億円超。前月比は3カ月連続の増加、前年同月比は18カ月ぶりの増加で、回復が継続。内需は国内の成長戦略などもあって回復が見込まれるが、外需は横ばい圏内。海外経済の動向等を注視。【10月分内需】386.5億円(前月比△8.5% 前年同月比+40.5%)。■内需総額・前月比6カ月ぶり減少、前年同月比4カ月連続増加。・期末効果の反動もあり2カ月ぶりの400億円割れだが、9月に次ぐ本年2番目の受注額。・回復のすそ野が広がりつつある中、着実な回復の動きが継続。① 一般機械 146.5億円(前月比△20.2% 前年同月比+43.0%) うち金型 29.0億円(前月比+15.1% 前年同月比+94.5%)② 自動車 124.9億円(前月比+5.9% 前年同月比+37.4%) うち部品 97.2億円(前月比+15.3% 前年同月比+54.9%)③ 電気・精密 31.7億円(前月比△2.7% 前年同月比+8.9%)④ 航空機・造船・搬送用機械 19.6億円(前月比△17.0% 前年同月比+10.5%) 【10月分外需】635.6億円(前月比+8.8% 前年同月比△4.8%)。■外需総額・前月比5カ月ぶり増加で、3カ月ぶりの600億円超。・前年同月比は13カ月連続減少だったが、減少幅は5カ月ぶりに一桁台へ縮小。・主要3極は全て前月比増加。欧州はリーマンショック移行の最高額を記録。① アジア:259.2億円(前月比+10.3% 前年同月比△29.6%)・東アジア:166.3億円(前月比+9.9% 前年同月比△44.0%)〈中国〉:123.3億円(前月比+7.5% 前年同月比△46.5%)・その他アジア:92.9億円(前月比+11.0% 前年同月比+30.7%)〈タ イ〉:48.7億円(前月比+37.7% 前年同月比+101.9%)〈インド〉:10.6億円(前月比△60.7% 前年同月比+6.6%)② 欧州:150.8億円(前月比+12.0% 前年同月比+75.4%)〈ドイツ〉:49.8億円(前月比+37.9% 前年同月比+104.9%)③ 北米:211.0億円(前月比+5.8% 前年同月比+3.2%)〈アメリカ〉:177.9億円(前月比△2.3% 前年同月比+5.6%)
9月分超硬工具主要統計
超硬工具協会がまとめた9月分超硬工具主要統計は以下の通り。【超硬合金重量】457トン(前年比98.7)。【超硬工具生産額】切削工具183億1300万円(前年比101.6)、耐摩工具29億9900万円(同102.1)、鉱山土木工具6億1400万円(同94.9)、その他工具4億3900万円(同87.6)、焼結体・工具18億4800万円(同109.7)、合計242億1300万円(同101.8)。【輸出入】輸出76億600万円(前年比109.6)、輸入48億7200万円(同121.6)。【超硬工具出荷額】切削工具192億300万円(前年比114.2)、耐摩工具30億1100万円(同102.0)、鉱山土木工具6億8000万円(同97.3)、その他工具4億700万円(同112.1)、焼結体・工具20億9200万円(同123.9)、合計253億9300万円(同112.7)。【刃先交換チップ】生産2582万9000個(前年比95.2)、出荷2629万4000個(同110.1)。
平成25年度超硬工具協会賞を発表! 超硬工具協会
超硬工具協会(理事長=増田照彦氏)はこのほど、平成25年度超硬工具協会賞の受賞者を発表した。同賞は同協会創立30周年を記念して設けられた表彰制度に基づき、毎年実施されているもので、今回は通算36回目にあたる。
今年度の受賞者は業界功労賞2名、技術功績賞19件、作業・事務・生産技術等の改善賞6件。
表彰式は来年1月9日(木)、東京丸の内の銀行倶楽部で開催する同協会の新年賀詞交歓会で行われる予定。
業界功労賞(2件)
○生悦住 望 氏(ダイジェット工業株式会社)
昭和9(1934)年7月16日生まれ
■功績の概要
氏は、当会が昭和43年創立20周年を記念して挙行された海外視察団に参加されたことを皮切りに平成25年6月常任理事を退任されるまで45年の歳月を当会とともに歩まれた。昭和58年5月の役員改選で懇親担当常任理事に就任、その後、副理事長を通算5期10年、常任理事を同10期20年、協会の主要幹部として当会を主導牽引された。その間役職は懇親担当2期3年、関連団体担当4期8年、協会賞担当2期3年、関西地区担当8期16年と30年間で4つの担当を歴任された。
最初の懇親担当常任理事就任より、事業の発展はそれぞれの会社が努力することは当然だが、まして業界が協調して全体のレベルアップを計ることが重要であり、当業界が共存共栄の実をあげ発展していくためには会員意識を強固に相互の意思疎通こそ肝要と当会の基本理念を会員会合はもとより、対外的にも関連団体担当常任理事時代には、機械工具団体懇話会をはじめ関連業界代表会合等でその輪を広められた。また、通算16年間、関西地区担当理事として、年8回の地区懇会合を主導、同2回の親睦ゴルフ会、ソフトボール大会及び囲碁大会と親睦行事もすべて参加されるなど、当会の全員参加と協調融和の基本理念の具体化に著しく貢献された。
〇吉田省三 氏(日本タングステン株式会社)
昭和18年4月20日生まれ
■功績の概要
氏は、平成15年常任理事就任と同時に資材担当理事並びに平成13年に設立した初代環境担当理事に就任。特に、2期目の資材・環境担当副理事長時代の平成17年には年初から急激に高騰をみたタングステンの価格動向、及びその環境問題に関して、氏が理事を務めるタングステン・モリブデン工業会とともに情報収集と問題解決に奔走された。また、関連団体に先駆け、PRTR法(化学物質管理促進法)、超硬合金、サーメット、セラミックの3種類のMSDS(化学物質等安全データシート)の業界標準のひな型を策定し社会、時代の要請に応えるとともに会員企業に多大な便宜を与えるなど環境委員会の方向性と礎を築かれた。
また、地球温暖化への対応はもとより、欧州のRoHS司令等国際的な物質規制を踏まえた会員企業の環境対応製品を積極的に評価認定する環境調和製品認定制度の実施に向け、3年間14回に及ぶ議論を推進された。また、19,20年度には協会賞選考委員長として応募件数の増加策を推進され、特に作業・事務・生産技術等の改善賞の選考評価、特にノウハウの開示問題などに腐心され、改善賞の選考の難しさに一石を投じられた。
技術功労賞(19件)
①技術の特徴 ②新規性/独創性 ③協会に対する啓発度(社名五十音順・氏名敬称略)
高機能ショルダーカッタ「MFWN型」の開発 京セラ 機械工具事業本部
滋賀野洲工場 古賀健一郎/柴田雅寛/山道一輝
① MFWN型は、様々な加工に対応できる高機能ショルダーカッタである。ショルダーカッタに求められる性能は、1つのカッタで肩加工、面加工、溝加工、バーチカル加工と様々な加工に対応できる「多 様性」である。同時に、1つのカッタで荒加工から仕上げ加工まで対応できることが求められており、優れた耐欠損性、低抵抗、良好な面品位を兼ね備えたカッタが求められている。MFWN型は、これら課題を解決するために開発された製品である。
② 本製品は、ネガタイプチップの特性を活かすため、主切刃の構成を側面視で、コーナRから若干傾斜させた直線切刃と、さらに大きく傾斜した凹曲線切刃の組合せとし、さらにそれを、コーナRの両側に対称に配置している。その結果、シンプルな構成ながら、90°カッタの高機能性に加え、低抵抗と高信頼性および、ワイパー効果による優れた仕上げ面を実現している。
③ 1つのカッタで様々な加工に対応できるため、工具本数の削減、非稼動時間の削減に貢献することができた。また、ダイナミックスラント設計による、低抵抗化と、刃先先端のストレート切刃による優れた耐欠損性により、ユーザー様の生産性向上に貢献した。
また、90度タイプカッターとして、勝手無し両面6コーナチップにより、コスト削減に貢献することができた。(環境調和製品No: 2012-007)
極小内径加工用工具「EZバー」の開発 京セラ 機械工具事業本部
鹿児島川内工場 津田祐一/小林洋司/白神晴崇
① 本開発は従来の極小内径加工用工具において問題であったチップ交換時の段取り時間の削減と、精密加工における加工寸法バラツキの抑制を目的とした。
本開発品は、従来の棒状チップの後端部に独自の傾斜面を設けていること、また、スリーブに複数の位置決めピン挿入部を設けていることが特徴である。
② 棒状チップの後端部に独自の傾斜面を設け、その傾斜部が、位置決めピンと接触することにより、シャンクを下側に押し付ける力が発生する。さらにシャンク固定用ネジの締結力も、同方向のシャンク下側に作用させることにより、刃先の高さ方向と、長手方向の刃先位置が、高精度で割り出しできるようになった
また、位置決めピンを差し替え可能にすることにより、1つのチップで複数の突き出し寸法に対応できるようになった。チップ後端部傾斜面と位置決めピンによる加工中のチップの回り止め効果により、拘束力が向上し、安定加工、加工寸法バラツキの抑制を実現した。
③ EZバーの開発により、簡単位置決め・拘束と、高精度安定加工が可能となった。これにより、段取り時間の削減、寸法不良の削減につながり、ユーザー様の生産性向上に貢献した。
また、1つのチップで複数の突き出し寸法に対応できるため、ユーザー様においてチップの在庫管理の簡素化に貢献した。(環境調和製品No.2012-015)
軟質材用超硬合金PDMの開発 サンアロイ工業
技術部 岩崎政弘/西牧宏/中塚明日美
① 本製品は、アルミ、銅等の軟質材料やステンレス等の加工において、耐焼き付き用途の改善を目的とし、低摩擦化を実現した超硬合金である。即ち、鍛造や打ち抜き加工時に生ずる摩擦熱を抑制させることで、超硬合金の結合金属とアルミや銅との焼き付きが改善され、耐摩耗性に優れた材料開発が実現できた。また、超硬金型に作用する加工負荷が軽減することで、耐摩耗性と二律背反の関係にある耐チッピング性にも優れており、各種用途で工具寿命の改善に効果が得られている。
② これまで、超硬合金に二硫化モリブデン等を添加することで摩擦を低減した開発事例はあったが、添加材の影響により機械特性が低下し、鍛造、打抜用途の工具として使用することは困難であった。本製品は、添加材から製造工程等の各種改善を図ることで、超硬合金の機械特性を損なうことなく低摩擦化を実現したことに新規性がある。
③ 本製品により、鍛造および打ち抜き加工用途の超硬金型寿命を改善するとともに、コーティング処理の困難な金型の焼き付きを改善することで、金型のコスト低減に繋がり、ユーザーの生産性向上に貢献できた。
スミダイヤバインダレスエンドミルの開発 住友電工ハードメタル
超高圧マテリアル開発部先進工具開発グループ主幹 島田浩之/超高圧マテリアル開発部先進工具開発グループ 矢野和也/住友電気工業アドバンストマテリアル研究所 ダイヤ応用グループ長 角谷均
① 電子機器部品用等の金型では超硬合金のように高硬度で、かつ高精度なものが求められるようになっている。しかし同加工に必要な耐欠損性、耐摩耗性、刃立ち性を十分に兼ね備えた工具材料は未だ無い。当社ではこのようなニーズに応えるために、ナノ多結晶ダイヤモンド工具「スミダイヤバインダレスエンドミル」を開発した。
② ナノ多結晶ダイヤモンドは、粒径が数十ナノメートルの微細なダイヤ粒子が高温・高圧下で結合材なしで強固に直接接合した世界初の材料である。これにより、従来ダイヤモンドよりも高硬度で、かつ単結晶のような劈開性を示さないため、高い耐摩耗性、耐欠損性を示す。また刃立性に優れており、良好な加工面粗さが得られる。
③ ナノ多結晶ダイヤモンドを用いたスミダイヤバインダレス工具により、超硬合金のような高硬度材で仕上げ面粗さRa10nm以下の鏡面加工が可能である。また単結晶ダイヤモンド工具等と比較して大幅な長寿命化が可能である。従来加工方法である放電加工+ミガキ工程に比べても形状精度を格段に向上させることができる。
正面フライス工具 スミデュアルミルDGC型の開発 住友電工ハードメタル
デザイン開発部ミリング工具開発グループ長 前田敦彦/デザイン開発部ミリング工具開発グループ 馬場達夫/デザイン開発部ミリング工具開発グループ 長見佳成
① 本製品は両面使いのネガチップを採用した正面フライスカッタであり、刃先強度を確保しながら、切刃形状の最適化により低抵抗の切削加工が可能である。また、8コーナ用と16コーナ用の異なる形状のチップを同一ボディに取り付けることができる。更に、ワーク端面の強固なバリ発生を抑制する専用チップも開発した。
② フライス加工では特にカッタ出口側に出るバリが大きくなりやすい。本製品ではフライス加工でのバリ生成理論に基づいて対策を検討し、主切れ刃とさらい刃の繋ぎ目にチャンファー部を設け、カッタ出口で発生するバリがワークから分断されるようにした。これによりワークに残るバリが大幅に抑制可能となった。
③ 本製品のチップは無研磨チップで高精度を達成しており、高品質な製品を安価に提供できる。また新チップ材質の採用による長寿命化も特徴としている。加えてバリ抑制チップにより後工程の負荷低減も可能であり、トータルでユーザーの加工コスト低減に大きく貢献している。 (環境調和製品2012年度認定 2012-019)
鋼旋削用コーテッドサーメット T1500Zの開発 住友電工ハードメタル
合金開発部合金開発グループ主査 小池さち子/合金開発部合金開発グループ主席 広瀬和弘/合金開発部グループ長 福井治世
① 自動車分野等における加工の高能率・高精度化に伴い、仕上げ加工では高負荷条件下での加工面の品質維持による長寿命化が求められている。これに対応するため、優れた耐溶着性と耐摩耗性を有する業界初の超潤滑PVDコーティング『ブリリアントコート』と、同コートを適用したコーテッドサーメット T1500Zを開発した。
② ブリリアントコートは鋼との親和性が低い新コーティング材質の適用により被削材の溶着を大幅に低減し、組織の微細化により強度を高めることでチッピングの抑制に成功した。この結果、T1500Zは加工の初期からノンコートサーメットに匹敵する優れた加工面品位が得られ、かつ安定した品位を長時間維持することができる。
③ T1500Zは、従来ノンコートサーメットしか使用できなかった高品位な仕上げ面が要求される用途にも適用可能であり、従来比1.5倍の長寿命化が可能である。また各種鋼部品加工の一発仕上げを実現するなど、コストと品質の両面で多くの顧客に貢献している。(環境調和製品2013年度認定 2013-001)
『耐熱合金用ワンカットラジアスエンドミル』の開発 ダイジェット工業
切削工具技術部技術課課長代理 長田昌文/生技部三重工具生技課STグループ主任 梶章宏
① 本開発は航空機業界を主体とする耐熱合金加工において、びびりの改善を狙った不等分割不等リードラジアスエンドミルである。本製品はびびり抑制を目的として、外周切刃を不等分割不等リードにし、尚且つコーナR部も不等リードギャッシュとすることにより、コーナR部で加工する際でもびびりを低減できるように改良した点に特徴がある。加えて外周切刃すくい角およびコーナRをポジとすることで切れ味がよく溶着を低減することができる。
② 多数のメーカーから不等分割不等リードエンドミルが発売されているが、コーナR部は不等分割のびびり抑制効果のみであった。これをコーナR部にも不等リードを採用し、その値を最適化することにより、さらにびびり抑制効果を持たせた。ブレード、リブなどのコーナR部を多用する加工において効果が大きい。コーナRを不等リードとしてもコーナR精度を±0.02と高精度を維持している。
③ 従来からある不等リードによるびびり抑制技術をコーナR部にも適用することで幅広い加工において優れた切削性を示す。航空機部品加工等において加工面の品質向上、工具の長寿命化に貢献した。(環境調和製品認定NO.2013-004)
ステンレス旋削用CVD工具「T6100シリーズ」の開発 タンガロイ
材料開発部主任 佐藤博之/福島直幸
① 難削材のステンレスを加工した場合、被削材の溶着から工具すくい面の被膜剥離・破壊が生じ損傷が進行する。安定した寿命で加工するために、この被膜破壊・剥離を抑制する技術を確立した。具体的には元素拡散によって、母材/被膜間の密着性を改良(スクラッチ試験で従来被膜より130%性能up)した。
② ステンレス切削における寿命ばらつきが、工具すくい面側の損傷に因ること、これは溶着起因による被膜の剥離・破壊が進行することで生じることを明らかにした。このすくい面の損傷抑制には被膜/母材界面の密着性(元素拡散の均一性と量が多いことが特徴)を改善することで、切削中のすくい面剥離量を改善した。
③ ステンレス加工においても高能率(高速)加工の要求は多く、このT6100シリーズは高速加工用で安定・長寿命な加工を実現する。特にT6120はオーステナイト系ステンレスを切削速度200m/min以上で加工しても安定した寿命を示した。ユーザの部品加工時間を短縮し、生産性の向上に大きく貢献している。
8コーナ高送りカッタ DoFeedQuadの開発 タンガロイ
切削工具開発部工具開発課 吉田悟/今田静恵/生産技術部TAC製品技術部 坂内由昌
① 「DoFeedQuad」は、超高能率で優れた経済性を発揮する次世代高送りカッタである。これまで以上の高能率化には、高負荷時の刃先の挙動を抑制すること、低抵抗で強靭な切れ刃であることが求められ、経済性の観点では、コーナ数が多く、シンプルな設計が望ましい。「DoFeedQuad」は、これらの課題を解決した製品である。
② キーテクノロジーである「新ダブルダブテールクランプ」は、インサートを強固に固定する全く新しい構成のクランプ機構で、ねじサイズやインサートサイズを最小化しつつ、切削時のインサート変位量を50%以上低減、これまで不可能であったap=2mm、fz=2.0mm/tの高能率安定加工を実現した。
③「新ダブルダブテールクランプ」を採用した「DoFeedQuad」は、平面加工の加工能率を飛躍的に向上することができる。多コーナで小型のインサートは工具費低減に直接的に貢献できると共に、加工単位当たりのレアメタル使用量が最小となり、環境性能にも優れる。(環境調和製品認定2013-003)
内径加工用DoMiniTurn/Bore Lineの開発 タンガロイ
切削工具開発部工具開発課 山口岳志/小池渉/名古屋工場製造2課 木村有伸
① 『DoMiniTurn/Bore Line』は、ポジとネガの逃げ面を持つ独自のインサート形状により、従来片面ポジタイプインサートが使用されている小径内径加工領域において、両面化によるコーナ数の倍増で経済性を高め、かつ、ラジアルレーキの低減により、大きな切りくずポケットと低抵抗化を実現し、ポジインサートと同等の切削性能を可能とした。
② ポジの逃げ面により、ポジインサートと同等のラジアルレーキを実現したことにより、低抵抗化及び大きな切りくずポケットを設けることが可能となる。また、ネガの逃げ面により、ダブテール構造を用いた強固なクランプを実現し、耐びびり性および切りくず排出性を向上している。
③ 『DoMiniTurn/Bore Line』は両面化による使用可能コーナ数の倍増と、「ダブテールクランプ」による強固なクランプにより、お客様の生産コストの低減に貢献している。 使用可能コーナ数に対して、レアメタル使用量も下がり、環境負荷を低減し社会に貢献している。(環境調和製品認定2012-016)
高経済性6コーナドリル TungSix-Drillの開発 タンガロイ
切削工具開発部工具開発課 佐治龍一/川崎創造/いわき工場TAC工具製造課 神永 篤
① インサート交換式ドリルを使用する際の利点は、被削材に合わせたインサートを選択できること、再研削が不要で容易に使用できることなどである。本開発では、これらの利点に加え、従来の4コーナ使用の製品に対する経済的な利点を伸ばすことを狙い、世界初の6コーナ使用可能なインサート交換式ドリルを開発した。
② インサートの片面には外周刃を3コーナ、もう片面には中心刃を3コーナ配置し、逃げ面形状を工夫することで、コーナ数を従来比1.5倍としながらも、刃先強度向上と、切削抵抗低減に成功した。専用設計された高速対応新材種AH9030との組合せで、高能率化も同時に達成した。
③ 『TungSix-Drill』は、使用可能なコーナ数を従来の4コーナから6コーナに増やしつつ、相反する低抵抗化を実現することで、インサート交換式ドリルの高経済性の利点を伸ばし、お客様の生産コストの低減に貢献している。(環境調和製品認定2012-020)
鋼加工用コーティング材種「DM4」の開発 日本特殊陶業 小牧工場
テクニカルセラミックス関連事業本部機械工具事業部技術部 波多野祐規/豊田亮二/吉川文博
① 被削材の難削化により従来材種では「高速加工」や「長寿命化」への対応が困難になりつつある。特に溝入れや突っ切り加工では、「耐酸化性」「耐摩耗性」「耐溶着性」「耐密着性」が要求されこれらを同時に満たすことは困難であった。本開発では結晶格子の歪抑制による膜内及び膜界面の残留応力の緩和技術、及び固体潤滑技術で、「耐酸化性」「耐摩耗性」だけでなく「耐溶着性」「耐密着性」の向上を目的に開発を行った。
② 膜の高硬度化に伴い密着性が低下するトレードオフの課題を打破する為、3つの新技術を各層に盛り込み、「耐酸化性」「耐摩耗性」と「耐溶着性」「耐密着性」の向上を両立させた。
・表面層:固体潤滑性に優れ、摩擦係数を低減したTiN系耐溶着膜
・中間層:下地層との密着性を高め、表面層側を高硬度化したTiCN特殊傾斜膜
・下地層:結晶構造を制御し圧縮応力を低減。基材との密着性を高めたTiAlN系特殊硬質膜
③ 鋼系の溝入れ、突っ切り加工等において、安定した長寿命化が可能となりユーザーより要望される高能率加工と工具費削減に大いに貢献することができた。また耐溶着性の向上により高精度、美麗な加工面を得ることができ、品位向上も同時に果たすことができ、ユーザーから喜びの声が多数寄せられている。
WC-FeAl系超硬合金の開発 ノトアロイ
技術課係長 澗張光広/技術課 向出保仁
① 熱間鍛造金型用材料として、超硬合金はCoの軟化のため使用することが難しく、さらなる難加工材料への対応やニアネットシェイプに対応するためには既存の材料では限界である。そこでCoの代替として、硬さが高く、耐酸化性に優れるFeAl金属間化合物を結合相に用いた、WC-FeAl系超硬合金を開発した。
② WC-FeAl系超硬合金は産業技術総合研究所にて基本特許として開発された技術であり、弊社にて性能向上のための製造プロセス及び大型成形体焼結技術の開発を行った。強度は抗折力で2.9GPa(従来比70%up)を達成し、寸法ではφ140×50mm(従来比約8倍)の均一な焼結体を得た。
③ Coが特定化学物質に指定された今、Coの代替は急務である。WC-FeAl系超硬合金を用いることで、Coレス化が図れ、環境に優しい製品が提供できる。使用用途として、温・熱間鍛造金型や粉末プレス型がある。温・熱間鍛造金型では寿命が2~5倍になることが期待され、粉末プレス型では高圧力での使用が可能となった。
多機能正面フライスの開発 日立ツール 成田工場
開発センター 日畑忠広/村 尚則/村田智洋
① 面削加工は最も一般的な加工であり、使用する機械、ワーク、工具形状も多岐にわたる。従来は工具管理工数の増加を避けて汎用的な工具を選択する場合が多く、加工能率を犠牲にしていた。本製品は従来製品では二者択一であった汎用性と加工能率を両立できるように改良した点に特徴がある。
② 従来、コーナ数が異なるインサートが同じボディに取付く工具はあったが、加工改善のアプローチは同じであった。本開発品は1種のインサートと切込み角が異なる2種のボディで、高送りと高切込みという全く異なるアプローチでの加工を可能にした。これにより、インサート管理を煩雑にする事無く、加工環境に合せた能率改善を可能にした。
③ 本インサートは、高切込みボディを用いて仕上げ加工も行うことが可能で、その際に使用する切れ刃は高送りボディで用いる切れ刃と独立した設計となっている。これにより、2種類のボディを併用することで1つのインサートを最大で16コーナ使用できる環境にやさしい製品とした。
高硬度鋼用高能率多刃ボールエンドミルの開発 日立ツール 野洲工場
商品開発センター 堺真二郎/商品開発センター 居原田有輝/製造センター生産技術グループ 佐藤亮介
① 本製品は、今後更に需要の増加が見込まれる高硬度鋼を高能率に直彫り加工することを狙ったものである。加工能率向上を実現するための多刃化において生じるボールエンドミル特有の”先端部の技術的課題”を解決した点、および最新のCAD/CAMに搭載されるツールパスを有効に活用できる形状に設計した点に特徴がある。
② 従来よりボールエンドミル先端部は切削速度がゼロになるため切削性が低下し、また多刃にすることで切り屑詰まりが生じるという課題があった。本工具においては、先端部の切削速度ゼロ点を切削点から回避し、かつ切り屑排出向上のため独自の先端形状を有することで上記課題を解決し、高硬度鋼を高能率加工できる多刃ボールエンドミルを実現した。
③ 高硬度鋼を高能率で直彫り加工できることで、鋼材の熱処理工程に要する時間を削減し金型製造期間を大幅に短縮することが可能となる。また、最新のCAD/CAMに搭載されるツールパスを最大限に活用できるため、従来では成し得なかった新たな加工提案で市場へ貢献可能である。同時に加工機等の消費電力を削減可能とし環境負荷低減にも貢献するものである。
フジロイ摩擦攪拌加工用ツールの開発 冨士ダイス
生産開発本部研究開発部主査 川上 優/生産開発本部研究開発部長 北村幸三
① 摩擦攪拌接合(FSW=Friction Stir Welding)で用いられる摩擦攪拌加工用ツールは、アルミニウムまたはアルミニウム合金については、SKD製が長寿命で問題なく使用されているが、鉄または鉄合金特にステレンスについては、SKD製では、直ぐ摩耗するためより長寿命の材料が求められている。
② 同社は、ステレンス用の摩擦攪拌加工技術の開発を、地方独立行政法人大阪府産総研、大阪府立大学およびアイセル株式会社と共に行い、摩擦攪拌加工用ツールに超硬合金を適用するには、硬さ、破壊靱性値、高温硬さおよびWC粒度を適切に規定することを見い出し、適する超硬合金をフジロイ摩擦攪拌加工用ツールとして完成・開発に成功した。
③ 摩擦攪拌加工用ツールは、鉄または鉄合金特にステレンスについては、比較的低価格で長寿命の材料が開発されてなかったが、本開発で超硬合金の中の特定の特性の材種が適することを明確にした。本分野はこれから本格化する分野であり、期待されている。
Rドリルの開発 マコトロイ工業
津工場技術部技術課課長 東脇啓文/営業部営業部長 橋本英二
① 本製品は、航空機等で使用されている炭素繊維強化プラスチック(CFRP)の穴明け時に発生しやすいデラミネーション(層間剥離)の抑制、高能率、長寿命を狙ったものである。ダイヤモンドコーティングにより耐摩耗性に優れると共に、切刃エッジ部の摩耗に伴う切削性能の低下が抑えられ、より多くの加工にわたり切削性能が維持できる点に特徴がある。
② 従来の切削工具では切刃部のすくい面及び、逃げ面全体にダイヤモンドコーティングが施され、CFRPへの穿孔を行うと切刃エッジ部の摩耗が進行するに従って、切刃エッジ部がR形状に摩耗し、大きくなり、切削性能の低下によりデラミネーションを発生させ穿孔寿命が短い。ドリル先端切刃R形状、セルフリグラインド機構の採用によって、切削性能の低下を抑制することで、デラミネーションの抑制、高能率、長寿命を実現した。
③ 従来工具と比べて穴品質を維持し、使用工具本数の低減、加工効率の向上により航空機業界などの加工、設備投資に貢献。又、資源の有効利用に効果があり、電力の削減により環境にやさしい製品を提供。
鋼旋削加工用CVD材種MC6025の開発 三菱マテリアル 筑波製作所
材料開発部CVDグループ 素花 章/生産技術部生産技術グループ 平方史生
① 従来、鋼部品の加工においては切刃領域に生じる疲労亀裂を起点としてチッピング損傷が発生しやすいという課題があった。本製品の開発においては疲労亀裂の発生箇所および発生形態に着目し、超硬合金母材の改良およびCVD被膜の結晶方位制御により、疲労亀裂起因によるチッピングを防止するとともに、高耐摩耗コーティングの適用により、従来製品と比べて安定した長寿命化を実現した。
② 加工後切刃の調査より、切刃稜線部に生じる疲労亀裂が母材の一定深さ以上に進展することがチッピング発生の主要因であると特定し、その進展を防ぐために切刃稜線付近の母材結合相濃度の増加を試みた。新原料を含めた成分組成と焼結プロセスの最適化により、当該領域の結合相濃度を従来の約2倍に高めた母材の製造を達成し、これにより耐チッピング性の大幅改善を実現した。さらに、Al2O3層の特定方位の配向度と耐チッピング性に相関関係があることを確認し、コーティングプロセスの最適化により最適配向度への安定制御技術を確立し、さらなる耐チッピング性の向上を実現した。
③ 従来製品では突発的なチッピング発生の懸念から工具交換の定数を低く設定することが多かったが、本製品では切れ刃を本来の工具寿命まで使い切ることが可能となった。これによりユーザーにおける単位加工数量に必要とされるインサート個数が減少するため、ユーザーにとっての工具コストの低減、および超硬工具製造における希少資源使用量の削減という観点で貢献度が大きいと考える。
スマートミラクルエンドミルの開発 三菱マテリアル株式会社 明石製作所
開発部 深田耕司/開発部 橋本達生/ソリッド工具センター 大田康史
① 本製品は「Ti合金やステンレス鋼などの難削材の高能率加工」を目的として開発したエンドミルである。前述の難削材は、「熱伝導性が低く、加工硬化しやすい」という材料特性から、これまで高能率に加工することができなかった。
今回、新たに開発した「スマートミラクルコーティング」に平滑化表面処理技術を適用することで、切削抵抗や切りくずの溶着を抑え、高能率かつ長寿命な加工を実現した。
② 従来の表面平滑化技術では、切れ刃が丸くなり母材が露出する問題があった。新開発の「ゼロミュー・サーフェース処理」で、平滑表面と超硬エンドミルに必要なシャープエッジの両立を実現させた。さらに、新開発のアーク放電制御技術による皮膜組織の最適化を図った「スマートミラクルコーティング」で、特に難削材における耐摩耗性能を向上させた。
③ 前述の新開発技術の採用で、難削材を従来比2~3倍もの高能率に加工でき、かつ長寿命化を実現。航空機部品などの生産性向上やリードタイム短縮に大きく貢献している。また、様々な加工に幅広く対応できるよう、3枚刃スクエア、4枚刃ラジアスなど6シリーズをラインアップし、ドリリング用特殊形状やクーラント穴付も揃え、適用範囲を拡大させた。
作業、事務、生産技術等の改善賞 (6件)
(社名五十音順・使命敬称略)
WC粉末出荷用ドラム缶のリユース化 アライドタングステン
製造部生産管理グル-プ 中沢謙太
【概略】
WC粉末を出荷する際に使用するドラム缶は、ユーザーで粉末使用後に破棄されていることが多い。そこで下記1~3を目的とし、ユーザー数社とドラム缶リユースの運用を開始した。
1. ドラム缶の廃棄(リサイクル)に掛かる環境負荷の軽減。
2. 製品輸送時の戻り便を活用し、効率良く ドラム缶を循環させる。
3. 環境配慮面でユーザー、当社の双方にメリット大。
【効果】
ドラム缶のリユース化は、0%⇒60%に向上。
1. リユース化により、2012年度には13.5トンの鋼材廃棄量を削減することが出来た。
2. ドラム缶の新規購入回数減少で、運送に伴うCO2排出量を年間3トン削減。
3. ドラム缶返却時にパレットも同時返却頂けるようになり、ユーザーとの資源循環型物流体制の構築に繋がった。
展示工具運搬システムの構築 ダイジェット工業
営業企画部営業企画課長代理 木村聡
【背景、問題点】
展示会にて工具を展示する際は、工具をケースから取り出し、展示台に個々にセットしており長時間作業を要していた。展示会終了後の撤収も同様に工具の片付けに長時間かかっていた。特にJIMTOFなどの大規模な展示会では、展示工具の種類が多く煩雑で、最終日の翌日まで作業するケースがあった。
【内容】
・かかる問題を解決するために、工具、展示台を専用の運搬ケースから取り出すだけで展示が可能となるシステムを構築し、工具展示作業の時間短縮を図った。
・システムは展示台を工夫し、展示工具がセットされた状態で個々の専用プラスチックケースに入れ、その上にクッション材を置き、蓋をするだけのシンプルな構造とした。
・クッション材料、形状は、運搬時に工具が動き損傷しないこと、ケース、展示台、クッション材は作業が誰にでも円滑に作業が出来るように識別等を工夫した。
【効果】
・1アイテム当りの展示・撤収作業時間…7分→10秒に短縮(6.83分の削減)
・削減時間(2012年実績)
大規模展示会・100アイテム展示… 年2回
小規模展示会・ 15アイテム展示…年13回
講習会・5アイテム展示 …年37回
6.83分×(2×100+13×15+37×5)×2回(展示・撤収)=7,923分 132時間の短縮。
焼結炉・CVD炉の自動停止および連絡手段の確保 タンガロイ
総務部人事グループ主務 鈴木隆一/いわき工場技術課主務 二宮貴洋/生産技術部TAC技術主務 赤羽 弘
【特徴】
従来からガス配管の漏れや、設備本体の圧力異常、UPSや自家発電機の接続で瞬停や停電時の冷却水確保等で非常時の危険回避策を運用してきた。しかし東日本大震災が発生した場合に、想定していた二次的なガス漏れ、停電等の影響で停止する設備はそれらを理由に停止したが、設備本体に異常が発生せず運転が継続し、場合によっては発火する危険状態が見られた。そこで感震器の設置および従来からの異常時対策との連動を行い、再発防止を行った。また通信手段の確保として無線機を設置した。
【内容】
1.感震器の設置
焼結室:4個、CVD室3個
2.地震発生時の自動停止:各部屋とも1個以上の感震器で250gal(震度5)以上を検出した場合。
焼結室:設備停止
CVD室:設備停止/ガス供給装置停止
【効果】
二次災害の可能性を大幅に低減
人、設備、そして建屋への二次災害の可能性を大幅に低減。
※シミュレーションテスト
CVD室にてシミュレーションテストの結果、3秒以内に停止が完了。
無線装置による通信が可能な事も確認済み。
海外向け梱包業務の効率化 富士精工
物流管理部物流管理課 中根直也
【改善前の問題点】
・各輸出先により、梱包、発送業務がばらばらで女性担当者が製品管理室に出向き、発送品を移動指示していた。
女性担当者: 毎日の指示作業→工数大 重量物の移動→危険作業
物流管理課担当者: 梱包、発送作業→発送日に残業対応
【改善点】
1.各輸出先の共通作業、個別作業を層別した。
2.マトリックスに従い、入庫伝票に、梱包可否が自動表示されるようにした。
3.入庫伝票表示に従い、品物の置き場と、次工程の梱包、発送内容を、明確にし、物流管理課内だけでの作業を可能にした。(男性作業へ移行)
【効果】
・女性担当者の業務時間短縮に寄与できた。
・女性担当者が、品物の移動をしなくても良くなった。→安全の確保
・物流管理課の工数は増えたが、物流管理課主導の梱包作業になった為、梱包作業の分散、平準化他の物流管理課の業務との兼ね合いも可能になった。→定時間内での作業
*1,640分/月の工数低減を達成。
特殊軸の生産性向上 富士精工
鹿児島工場 安村 知/熊谷浩
【背景】
ライン対象製品の受注減少の為、課員数削減の中 新規品(特殊軸)を含む納期対応が急務の状況下であり、大幅な時間低減活動が必要であった。特に特殊軸は短納期であり、加工本数も100本~150本/月の生産が必至の状況である。
【改善点】
【対象設備(インテ200)と(ロボドリル)】
工程集約の実施(5工程⇒2工程)
・タング加工をロボドリルへ移行(多数個取り治具製作)
・インテ200自動加工化(フィードパイプ製作)
【効果】
改善前 :5工程 改善後 :2工程
(387分/月)の低減を実現し課内業務効率化に貢献
複合旋盤での連続加工可の為、1169分以上の夜間加工が可能となる。
産業廃棄物のゼロエミッションの達成 三菱マテリアル 岐阜製作所
安全環境管理室 平塚明彦/斉藤直樹
【概要】
環境への負荷低減を図る廃棄物対策として、産業廃棄物リサイクル推進を実施しゼロエミッションを達成した。
【背景】
産業廃棄物を適正に処理することは、環境の保全を図るうえで最も基本的な要件のひとつである。廃棄物の排出を抑制し、次に廃棄物になったものについては、再使用、再生利用、熱回収により、できる限りリサイクルを行い、これにより最終埋立処分量の削減を図ることは、環境への負荷の低減の取組みに欠くことのできない課題である。
【内容】
事業活動により発生する産業廃棄物のうち、既存の対応ではリサイクルが困難なため最終埋立処分を行っていた汚泥類、ガラス・コンクリートくずは、2008年度では全産業廃棄物の4%を占めていたが、これら産業廃棄物の分別方法を徹底して調査見直しを行いリサイクルの取組みを進めたことにより、2012年度には0.5%未満となりゼロエミッションを達成した。
【効果】
産業廃棄物リサイクル率は96%程度で定着していたが、2008年度よりゼロエミッションをあらためて目標に取組み、2012年度に達成することができた。環境を配慮した事業場としてゼロエミッションは、対外アピールは大きいものがある。なお、産業廃棄物処理は環境マネジメントシステムと産廃業者との契約にもとづいて実施しているため効果の持続改善が保たれる。
平成25年度OKK会総会を開く
10月22日、名古屋市内のキャッスルプラザで「平成25年度OKK会総会」が開催された。
OKK会を代表して、
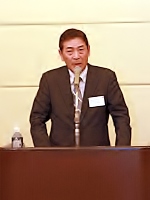
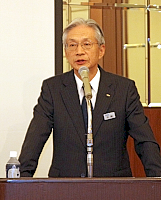
この中で井関社長は業績について、「2013年3月期は、昨年秋以降の世界経済の低迷を受け、売上げ高についてはやや前年を下回ったが利益については営業利益、経常利益、最終利益とも前年を上回ることができた。これも皆様のお力添えの賜だと思っている。今期、4月-9月の業績については、昨年暮れから中国の尖閣問題、世界経済全体の低迷、あるいは国内設備投資の低迷を受け、特に第一四半期に当初予定していた売上げ、利益とも計画を大きく下回ることになり、第二四半期においては相当盛り返したが結果として上期については当初の計画に至らなかった。この10月から残り6カ月弱、グループを上げて上期の不振を取り戻すべく、一丸となって取り組んでいる」と述べ、本年4月から中期計画として“NEXT STAGE 100”をスタートした意気込みを説明した。
このNEXT STEGE 100は、創業100周年を迎える2015年度までの3カ年、次世代を展望し、OKKの全ての事業基盤の強化・充実を図るもので、主力工場であるM工場の建て替えと設備の更新、タイOKKの工場拡張により生産機種を増加させ、生産能力の増強と品質の向上を図る。価格競争力と収益力の強化を目指して、製造原価の徹底した低減のため、生産効率の向上と、海外調達の拡大と部品共通化により一層のコストダウンを図り、また、営業基盤の強化についても、国内・北米でのソリューションビジネスの拡充やプレサービス、アフターサービス両面の体制を強め、付加価値の向上を狙う。
OKK技術開発方針を取締役上関執行役員 宮島義嗣 技術本部長が、重切削加工市場におけるOKKブランド力の強化をあげ、ボリュームゾーンを狙った量産機種の競争力アップに注力すると説明した。
軍事評論家でNPO法人 国際変動研究所 理事長 小川和久氏が「激動する北東アジア情勢と日本の安全保障」をテーマに講演した後、場所を移して懇親パーティが開かれた。
ユキワ精工がオールステンレスドリルチャックを発売
ユキワ精工(社長=酒巻和男氏)は、『錆に強く、しかもノングリス』のオールステンレスドリルチャックをこのほど新発売した。
ドリルチャックは、チャックハンドル(チャックキー)を使ってドリル、リーマなどの切削工具を簡単かつ安全に締め付ける3つツメ式のチャック。ユキワ精工のドリルチャックは、JIS B4634工作機械用ドリルチャック規格を上回る基準で製作しており、高精度なプロ用ボール盤、旋盤などで高精度な加工が可能。同社は1951年に日本でドリルチャックの製造を開始し、永年に亘る技術研究を進め、その高い精度、高品質、抜群の耐久力は広く世界に認められており、ドリルチャック世界3大メーカに数えられている。
特長は以下のとおり。
●オールステンレス
外観部品から内部の焼入れ部品まで、全てステンレスを使用している。従来のドリルチャックに比べ、錆びにくく、錆を嫌う環境でも安心して使用できる。
●ノングリス
他社のステンレスドリルチャックは把握力を確保するために、グリスを使用しているが、同製品は、ユキワ精工独自の永年に渡るドリルチャック製造のノウハウを生かし、ノングリスでも、高い把握力を有している。ノングリスなので、グリス漏れを嫌う医療現場や、食品製造現場でも使用できる。
●高品質
同社では日本で唯一JIS日本工業規格工作機械用ドリルチャック規格の認証を取得しており、この製品はJIS規格対象外だが芯振れ精度、把握力の基本性能において、JIS認証ドリルチャックと同等の性能を有している。
DMG森精機が天津工場グランドオープン!
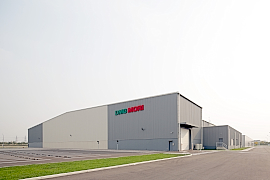
グランドオープンにあたり、現地時間10月18日(金)に中国工作機械工業会 王 黎明(Wang Liming)副会長、天津経済技術開発区(TEDA)许 红星(XU Hongxing)主任、Danfoss (Tianjin) Limited, Tianjin 钟 思钊(Zhong Sizhao)取締役をはじめとし、当社取締役社長の森雅彦、DMG MORI SEIKI Aktiengesellschaft CEO Dr. R üdiger Kapitza によってテープカットが行われた。
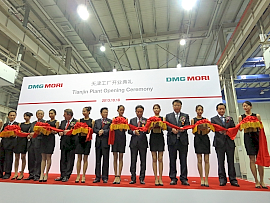
天津工場は、2012年に稼動を開始した北米工場に次ぐ海外製造拠点となる。中国の顧客に納める横形マシニングセンタを中心に製造活動を行うほか、鋳物の製造拠点としても日本・米国の工場へ供給。
この天津工場は、欧州・北米・日本・中国というDMG MORIで展開している世界4極体制を強化するものであり、この世界4極体制でロジスティクスコストの低減と納期短縮を図るとしている。
●天津工場の概要
所在地 :中華人民共和国天津市天津経済技術開発区西区
敷地面積:約90,000 ㎡
建物面積:約22,000㎡ (第一期)
操業開始:2013年9月
総投資額:約40 億円 (第一期)
生産品目:NHC4000、NHC5000、鋳物の加工
生産能力:100 台/月 (第一期)
従業員 :200 名 (第一期)
ナチ不二越が超速スポット溶接用ロボット「SRAシリーズ」にケーブル内蔵型を追加
ナチ不二越は、自動車の車体溶接工程の生産性向上に向けた高速化ニーズに対応するため、超速スポット溶接用ロボット「SRAシリーズ」を2011年11月から販売し、好評を博してきたが、今般、新たに中空アーム仕様のケーブル内蔵型4機種をラインナップに追加、カスタマーの多様なニーズに対応していく。
自動車の生産ラインでは、品質向上に加えて、サイクルタイム短縮や、少人・省スペース化、さらにはライン立ち上げ期間の短縮など、コスト低減、生産性向上のニーズが一段と高まっている。超速スポット溶接用ロボット「SRAシリーズ」の新しいラインナップとして、市場投入した中空アーム仕様の「SRA-H」は、アプリケーション用艤装ケーブルを内蔵することで、ロボットの設置自由度を向上させるとともに、ロボットのセットアップを容易にして生産ラインの立ち上げ期間を短縮する。
特長は以下のとおり。
(1) 設置自由度の向上
上部アームと手首の中空化により、手首先端に取り付けるスポット溶接ガンなどへのケーブルを内蔵。従来困難だった狭いスペースへの設置が可能となる。
(2) 信頼性の向上
ケーブルの動きを安定させ、溶接時のスパッタや周辺装置との干渉によるケーブルのダメージを回避することで、信頼性を向上する。
(3) ライン立ち上げ期間の短縮
ケーブルの干渉を考慮する必要がなくなることで、ロボットの動作シミュレーションや、設置後に行なう作業プログラムの実機確認作業を大幅に短縮、生産ラインの垂直立ち上げに貢献する。
(4) 適用ハンドの拡大
手首トルクの向上により、当社従来機に比べ約1.5倍の負荷能力を実現、大型溶接ガンにも対応。
DMG森精機が天津工場生産、横形マシニングセンタ“NHCシリーズ”の販売を開始!
DMG森精機は、2013年9月から稼働した中国、天津工場にて生産する高精度・高速横形マシニングセンタNHCシリーズNHC4000およびNHC5000の販売をこのほど中国にて開始した。
NHCシリーズは、高剛性と高速加工を実現し、弊社天津工場にて初めて生産する横形マシニングセンタ。コラムはX軸ガイド面を段違いに配置した構造を採用し、主軸にはクラス最大となるφ80㎜の大径ベアリングを採用することで重切削に必要な高い剛性を実現した。
剛性を高めながらも移動体を軽量化することで、優れた加速度を実現している。外国為替及び外国貿易法などで定める直線軸の位置決め精度の規制に該当しない範囲で、最高クラスの精度を達成していることも魅力である。また、自動化システムにも柔軟に対応し、ユーザーの加工に合わせてパレットプールシステムやワーク搬送ロボットなどと組み合わせることで生産性向上を実現する。
加えて、最適な仕様をパッケージとして2タイプがある。
特長は以下のとおり。
①高剛性
肉厚な高剛性ベッドにX、Z両軸のリニアガイド案内面を配置し、主軸軸受内径をφ80 mmに大径化した。さらに従来機に対してZ軸ストロークを30 mm延長することで主軸からパレット中心への接近性が向上したことにより短い工具を使用することが可能となり高剛性な加工を実現する。
②高速
早送り速度は全軸60 m/minとすることで、高速な送りを実現している。またオプションのパレット任意割出し仕様にはDDM(ダイレクト・ドライブ方式モータ)を採用している。ギヤを経由せずに直接モータの駆動力を伝達するため、より高速な割出しが可能となり非切削時間を短縮して生産性を向上する。
③高精度
主軸は、エアや冷却油の配管、ボルトの取り付け位置を主軸中心に対して点対称に配置することで、熱変位を抑止している。繰り返し位置決め精度は各軸で3.9 μm以下を達成しており、工具最大長さをパレットサイズより長くすることでテーブルを反転せずにボーリング加工ができ、ボーリング加工の精度向上と切削時間の短縮を実現する。
④信頼性向上
長期間にわたり高い信頼性を保つための工夫も凝らしており、主軸は高圧クーラントの多用を考慮してラビリンス構造を強化し、主軸軸受内にクーラントが浸入し難い構造としている。ATC(自動工具交換装置)用のアームは新機構の採用で長く重い工具でもしっかり把持し、確実な工具交換を可能とする。
④省エネルギー
環境への負荷低減とランニングコスト削減のため、機械停止時には主軸、サーボモータなどの主要な動力をしゃ断し、機械稼働時には減速時のエネルギーを電源として利用する効率的なドライブユニットを採用することにより、省エネルギーに貢献。機内照明にはLED式を採用し消費電力を削減しながら長寿命を実現している。油圧ユニットにはアキュムレータを搭載しており、油圧保持のための電力が不要である。
⑤MAPPSⅣ+ESPRIT®
操作パネルには高性能オペレーティングシステム「MAPPS Ⅳ」を搭載している。自由にカスタマイズできるメイン画面や見やすいボタン配置など使いやすさを追求した操作盤である。対話型自動プログラミング機能により、プログラミング作業を大幅に簡略化して、容易に加工プログラムを作成可能。加えて、オプションのCAMソフトウェア「ESPRIT®」では、機械とネットワーク接続されたパソコンにて複雑形状の加工プログラムを作成可能である。
⑥パッケージ
NHCシリーズは、ユーザーの加工に最適な仕様をパッケージとして用意している。パッケージの導入により、スピーディーかつ効率的にユーザーがオプションを選択することが可能であり、ユーザーの加工内容に合わせ、基本に即したベーシックパッケージと、より複雑で高精度な加工に対応したアドバンスドパッケージの2タイプがある。
ベーシックパッケージ内容>
・工具収納本数40本(センタスルー)
・シグナルタワー3段(赤、黄、緑)LEDタイプ
・スルースピンドルクーラント装置(クーラントタンク上設置型)センタスルー>(1.5 MPa)
・クーラントフロースイッチ(スルースピンドルクーラント用)
・クーラントガン(段取りステーション側)
・手動パルスハンドル別置き
・機内計測装置(主軸)オプチカル式タッチセンサ
・パレットエッジロケータ(2個)
⑦多彩な周辺機器(DMSQP)
スルースピンドルクーラント装置、ミストコレクタ、パレットプールなど11項目の周辺機器やシステムは、品質・性能・保守性に優れた製品をDMG森精機が厳選し、DMSQP(DMG森精機認定周辺機器)として認定していることにより、ユーザーは機械と周辺機器をDMG森精機で一括して手配することができる。生産性を向上させる幅広い周辺機器の中からユーザーの加工に最適な周辺機器を選択できる。
⑨安全性
ISO規格、IEC規格など国際標準の安全規格に対応している。