ニュース
タンガロイがTurnLine溝入れ・突切り加工用工具『TungCut』拡充アイテム発売
タンガロイ(社長=木下聡氏)は、このほど溝入れ・突切り加工用工具“TungCut”(タングカット)拡充アイテムの発売を開始した。
この商品は、2 コーナ溝入れ・突切り加工用工具TungCut は、工具寿命や加工寸法の安定に効果がある専用クランプシステムを採用し、様々なニーズに対応する豊富な品揃えにより、経済的で使い易さを追求した溝入れ工具シリーズである。
今回、横送り加工が可能な多機能インサートDTX に6 ㎜ 幅を設定、同時に3 種のホルダも拡充し、さらなるシリーズ強化を行う。
■ 主な特長
● DTX インサートに新たな6 mm 幅を設定し、多機能加工のより広いニーズに応える。
● 1本のホルダで外径、端面溝入れに対応可能。工具集約が可能であり、最大溝深さは4.8 mm まで対応可能。
● 丸シャンクを採用することにより、穴の奥に位置する内径端面溝入れに対応することが可能。
● 外径溝入れ・突切り用CTER/L タイプに、これまでとは適用する溝深さが異なるホルダを設定。加工する溝深さに対して、より適正なホルダの選択が可能となった。
■ 主な形番と標準価格
●インサート: DTX6-080 AH725 2,840 円(税込み:3,067 円)/DTX6-080 GH130 2,840 円(税込み:3,067 円)
●ホルダ: CTEFR2525-4T04 16,800 円(税込み:18,144 円)/CTIFR25-4T05-D270 41,300 円(税込み:44,604 円)/CTER2525-6T20 16,800 円(税込み:18,144 円)
アイテム数: インサート 2 形番
ホルダ 28 形番
セコ・ツールズがSteadyline™(ステディライン)防振システムにボーリングバーを拡張
製造業界全体で突出し部の長い工具がますます広く普及しているのを受け、 セコ・ツールズは特許取得済み製品ライン Steadyline(ステディライン)防振ツールに、ボーリングヘッド を追加した。
高い剛性と安定性を備えた Steadyline システムは、ホルダーボディ内の「動的受動的システム」によって不要な振動を効果的に低減する。このシステムでは、ダンピングマスが最初の曲げ振動に対して逆に振動する。したがって、この製品は一般的な突き出し量の長い加工を従来ツールの 2 倍の速度で処理でき、主軸圧力の軽減、材料除去率の向上、滑らかな部品表面仕上げ、ツールの長寿命が実現する。
Steadyline は、6xD、8xD、10xD のバーサイズと、Seco-Capto™(セコキャプト) C4、C5、C6 および HSK-T をはじめとする幅広いタイプから選ぶことができる。このシステムには、粗加工が ø36~69mm、仕上げ加工が ø34~69mm の GL 接続を採用した、コンパクトなボーリングヘッドも用意している。さらに、バーとヘッドにはクーラント供給口があり、切り屑排出性が改善されている。
従来の一般的なシステムでは、ボーリングヘッドの交換に複数の締め付けねじや機器を使用するが、 Steadyline バーのきわめて精度の高い GL 接続には、ヘッドを締める/緩めるのにスパナレンチ 1 本以外必要ない。
この接続は、内蔵クランプリング 1 個でしっかりと、すばやくロックでき、ボーリングヘッドを引き込んで安全で安定したテーパ面の接触を実現する。ボーリングバーを一度取り付ければ、システムをリセットしなくても、ヘッドを取り付け/取り外し可能である。
Vero SoftwareグループAPAC地域のディレクタ―に長谷川英紀氏が就任
Vero Software(イギリスチェルトナム・CEO Steve Sivitter)は、2015年1月1日よりVero Softwareジャパングループ(ヴェロ・ジャパン(株)/(株)セスクワ/エッジキャム(株))の代表取締役である長谷川英紀氏が、APAC(Asia Pacific/アジア太平洋地区:中国・インドを除く)エリアにおけるVISI、WorkNC、Edgecam、Smirt製品の直販・代理店販売のアジア太平洋地区ディレクターに就任したと発表した。長谷川氏は、自動車部品メーカー、CAD/CAM/CAE/PLM等のソフトウェア会社、Siemens PLM、前職Autodeskを経て、幅広い経験を積んだ後、昨年1月よりVero Softwareグループの営業部門のゼネラルマネージャーとして就任、同年4月より(株)セスクワ・エッジキャム(株)の代表取締役に、同年11月よりヴェロ・ジャパン(株)の代表取締役に就任し、Vero Softwareジャパングループの代表取締役として活動してきた。アジア太平洋地区ディレクターに就任した長谷川氏は、「昨年はVISI、WorkNC、Edgecamのチームを東京の一拠点に集めVero Softwareグループとして活動を開始し、7月にはHexagonのグループになるなど変化の多い年でした。今年はじっくりと腰を据え、Veroブランドの下、VISI、WorkNC、Edgecamのビジネスを強化し、さらにはHexagonのソリューションも含め、互いに補完しあえるところは補完するなどシナジー効果を今年も最大限活用していきます。また、多くの日本企業様がアジア進出しているように、弊社でもまずはアジアへ進出する企業様を支援するために管轄をアジアまで拡大しました」とコメントしている。
「今年は困難を克服する年」日本金型工業会東部支部が賀詞交歓会を開く
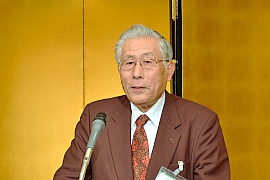
加藤支部長はあいさつの中で、「一部のユーザーに国内回帰の動きがみられる。新興国に比べて日本の金型は総合的にみてもメンテナンスや寿命の面で他国よりも優位性があり、国際競争力が上がっている。今年は困難を克服し、良い結果が得られるよう取り組んでいきたい」と述べた。
続いて、同工業会の牧野俊清会長が、「今年開催されるインターモールドには会員72社が出展する。日本の金型を世界に発信していくことは素晴らしいことだ」とあいさつした。
来賓を代表して、遠山毅 経済産業省製造産業局素形材産業室長があいさつし、牧野二郎 牧野フライス社長の発声で乾杯をした。
日立建機が「ZW80 ZW80-5B 」ホイールロダを発売 ~排出ガス規制のオフロード法2014年基準に適合~
日立建機(社長=辻本雄一氏)は、新型ホイールローダZW-5シリーズとして、「ZW80-5B」
(標準バケット容量0.9m3、運転質量4,895kg)を2月20日から発売すると発表した。
この製品は、特定特殊自動車(オフロード法)排出ガス2014年基準に適合したホイールローダで、現行モデルの良さを踏襲しながらも、経済性や作業性能、オペレータの快適性など、ホイールローダに求められるあらゆる点を改良し、ユーザーニーズに応えている。
販売目標は、国内向けに合計で年間650台を見込んでいる。
主な特長は以下のとおり。
1.時代にマッチした環境性能
・オフロード法2014年基準(特定特殊自動車排出ガス2014年基準)に適合している。
・排出ガスの後処理装置は「酸化触媒」のみで、PM(粒子状物質)を捕集するセラミックフィルタが不要なクリーンエンジンを搭載している。
・国土交通省低騒音型建設機械指定機である。
2.作業性の向上
・高出力エンジン採用で余裕のある作業性を実現した。
・大きなダンピングクリアランスとリーチ、小さな旋回半径でさまざまな作業現場に対応している。
3.快適な運転空間と操作性
・各種車両状態を表示するモノクロ液晶モニタをセンターパネルに内蔵した。
・サスペンションシートを標準装備し、快適な運転操作性を実現した。
・乗降口の左右にグラブハンドルと大型ステップを装備し、優れた乗降性を実現した。
4.メンテナンスの負担を低減
・モニタに、次回オイルおよびフィルタの交換までの時間を表示する。
・PM(粒子状物質)を捕集するセラミックフィルタがないため、一定時間ごとのフィルタ清掃・交換が不要である。
・フルオープンボンネット、ステップ付カウンタウエイトの採用で優れた整備性を実現した。
コマツが建設現場ICTソリューション「スマートコンストラクション」を開始
コマツ(社長=大橋徹二氏)は、このほど建設現場に変革をもたらすダントツソリューション「スマートコンストラクション」を開始した。
同社は、中期経営計画「Together We Innovate GEMBA Worldwide」で「イノベーションによる成長戦略」を掲げ、2013年からICTブルドーザ「D61PXi」やICT油圧ショベル「PC200i」などのICT建機の市場導入を進めてきた。
これらの開発に加え、建設現場が抱える様々な課題を解決し、「未来の現場」を実現させていくためのソリューションを開発、提供していくサービス新事業「スマートコンストラクション」を開始し、これからの中核事業として育成することにしたとしている。
「スマートコンストラクション」は、建設現場にあるあらゆる情報をICTで繋ぎ、安全で生産性の高い現場を実現するとともに、蓄積されたデータを社会インフラの整備や災害復旧にも役立てていく。新たにスマートコンストラクション推進本部を設立し、少子高齢化が進む日本からコマツレンタルを通じてこの新たなソリューションを提供していく。
スマートコンストラクションのサービス内容とそれを指させる技術
新たに開発したクラウドプラットフォーム「KomConnect(コムコネクト)」に以下の6つのプロセスに関わるあらゆる情報を入力し建設現場の全てをICTで繋げ、生産性を大幅に向上させ安全でスマートな「未来の現場」を実現する。
①現況の高精度測量
無人ヘリや3Dレーザースキャナー、建設機械の運転席に搭載されたステレオカメラなどを活用することで、短時間で現況を正確に把握し、現場の高精度な3次元データを生成する。
②施工完成図面の3次元化
顧客から2次元の施工完成図面を預かる3次元データに変換。3次元データの現況と施工完成形の差を視覚化することで、顧客は施工する前に、施工する範囲、形、運土量などを正確に把握することが出来る。
③変動要因の調査・解析
工事を進める上で大きな変動要因となりうる土質や地下の埋設物について、事前に調査し解析する。
④施工計画の作成
顧客がコムコネクトに施工条件を入力すると、「施工計画シミュレーション機能」が条件ごとに異なる施工パターンを提案する。また、施工開始後はリアルタイムの施工状況が施工計画シミュレーションに自動的に反映されるため、顧客は常に最適な施工計画を立案出来る。
⑤高度に知能化された施工
プロセス②で作成した3次元データは、コムコネクトを通じてICT建機に送られる。ICT建機は作業機を自動で制御するため、経験を問わず誰もが熟練作業者のような精度で作業を行うことが可能である。
⑥完工後の施工データ活用
ICT建機で施工した情報はコムコネクトに蓄積される。また、蓄積されたデータは、施工後の整備・修繕や自然災害などを受けた地域の復旧作業にも役立てることが可能である。
「さらなる高い数字を目指すよう努力していく」日本工作機器工業会が賀詞交歓会を開く
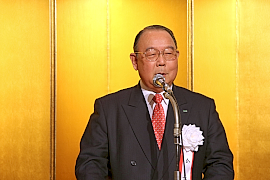
記念講演会は、川合勝義 VRテクノセンター航空宇宙生産技術中核人材教育プロジェクトコーディネーターを講師に迎え、「航空機業界の最新動向、サプライヤーに求められる要件について」をテーマに開催され、続いて賀詞交歓会が開かれた。
賀詞交歓会であいさつに立った寺町会長は、「今年の様々な賀詞交歓会はどこも大盛況であり、日本の元気が出てきた証拠であると感じている。2020年の東京オリンピック誘致が決まったことも先々の明るさを持っている。経産省を中心として日本の経済再生のためのものづくり減税も、投資減税に引き続き開発や地方創生等様々な諸策が出てきていることはわれわれにとって明るいことだと思っている。われわれはそれをうまく活用していけるかどうかが問われ、投げられたボールをきちんと受け止めて発展させることが重要であろう。年度の見通について2013年度に対して2014年度は20%ほどの増を予想している。残念なのは2015年度について関連する関係業界が微増としており、低い予想になっていることだが、さらに高い数字を目指すようわれわれ自身も努力していきたい」とあいさつをした。
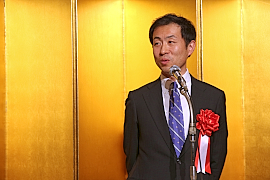
北川祐治副会長(北川鉄工所社長)が乾杯の発声を行った。
「今年は経済を好循環の節目となる大切な1年」日本フルードパワー工業会が賀詞交歓会を開く
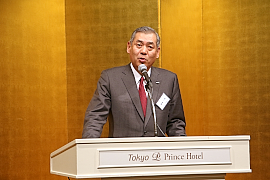
梶本会長は「昨年のわが国の経済環境は一昨年に始まったデフレ脱却を目指した超緩和金融政策を柱としたアベノミクス政策により景気は穏やかに回復基調に推移をした。しかしながら昨年4月に実施された8%への消費税引き上げによる個人消費の落ち込みは想像以上に大きく四半期続けてのマイナス成長となった。その結果政府が最低限必要と考えていた消費税10%への引き上げは1年半先送りされた。この間、昨年10月に日本銀行による第二弾の金融緩和策から為替は円高に株価は株高にそれぞれ大きく動いた。こうした状況から輸送機械業界をはじめとする多くの大手企業の本年3月期決算は過去最高の業績が期待されている。一方、円安により原材料など輸入価格が上昇したことにより、中小企業や家計には負担増の影響があり未だ消費行動が慎重になっているのも見逃せない。こういったことからも今年は経済を好循環され消費者マインドを改善させるために節目となる大切な1年になる。法人税引き下げや投資を促進させるための税制の改革、女性活躍を柱とした雇用政策、地域経済活性化による地方創生などの施策を早期に実現させることが不可欠であろう。また、賃金上昇による経済の好循環化により早期のデフレからの脱却を成し遂げ、元気な日本が再興されることを期待している。しかしながら原油価格の暴落などによる資源国の低迷もここにきて顕在化している。BRICSによる新興国の動きなど世界経済動向も注意深く見守っていきたいと思っている」とあいさつをした。
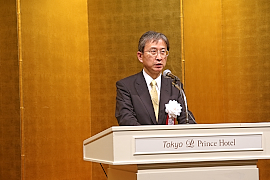
「過去最高を達成」日本工作機械輸入協会が賀詞交歓会を開く
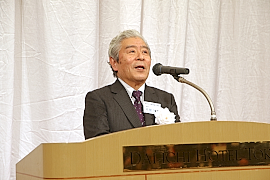
新年のあいさつに立った千葉会長は、「昨年1年間の通関実績は12月を含め780億円に達した。過去20年間で一番大きな数字になった。今年の見通しはというと、日工会の賀詞交歓会で花木会長は今年の見通しを1兆5,500億円とおっしゃっていたが、日工会の数字が好調のときは、われわれの数字も良いという実績がある。われわれ輸入協会としても悪い要因はないのではないか。今年1年は去年より増して多忙な年になると予想している」と述べ、今年ミラノで開催されるEMO MIRANO2015について視察団を結成し、現地の工作機械メーカーを見学するとして、会員企業に参加を呼びかけた。
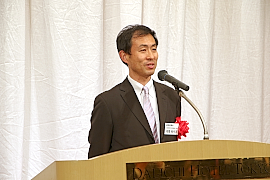
乾杯のあいさつ及び発声は、Aristide Martellini イタリア大使館貿易促進部在日代表の代読で小谷辰夫 同シニアトレードアナリストが行った。
【技術記事】機械的な工作機械活用アプローチについて
加工の生産性と収益性を最大限に高めるには、金属切削工程全体を最適化することが大切である。工程最適化の基礎となるのは、切削工具パラメータを賢く適用して、工作機械の性能を最大限に活用することである。工作機械を高い効果で活用するには、主に 2 つの要素がある。1 つ目は、金 属切削に機械を利用できる時間を最大限に延ばすこと、2 つ目は、その加工時間を最大限活用して、最大の 生産性、確実性、収益性を得ることである。
(著者:セコ・ツールズ全社技術教育マネージャ Patrick de Vos)
加工時間の最大化
工作機械を最大限に活用するには、まず金属切削の加工時間を最大限に確保する必要がある。機械が恒久的に工場に据え付けられているとしても、年間フルに活用されているとは限らない。1 週間に 5 日間 1 シフトで稼働する場合、休日やその他の非稼動時間を勘案すると、年間の稼働時間は約 1,300 ~ 1,400 時間になる。しかし、この時間がすべて金属切削加工に当てられるわけではなく、プログラミングやセットアップにかかる時間もこれに含まれる。
非稼働時間を最短に抑えるため、メーカーではオフラインプログラミングやモジュラー式セットアップ方式などの戦略を採用している。工具ケースや自動工具交換装置は工具取扱時間の短縮につながるが、このほかに時間のかかる手間が発生する。
ロボットやパレット交換装置は、被削材の取り付けや完成品の取り外しにかかる時間を短縮するのに役立つ。プログラミング、セットアップ、工具の取り扱いおよび作業において削られた時間はすべて加工時間に回せる。
高い効率で時間配分
金属切削時間を最大化する戦略を導入後、次にメーカーが直面するのは、効率よく時間配分して、可能なかぎり低コストで加工数を上げるという課題である。そのカギとなるのは、工作機械の性能を最大限に活用しながら、切刃を被削材に接触させることである。工作機械の限界を認識することも重要な要素である。
最適な時間配分を計画するにあたり、加工工程には変更できない要素があることを理解しておこう。加工部品の用途により被削材が決まり、被削材の加工性に応じて、初期の切削パラメータが決まる。たとえば、チタン合金は熱伝導が低いため、切削速度と送り速度を低速にし、熱集積を抑えなければならない。通常、機械の入れ替えはすぐに実現可能な選択肢ではないため、工作機械の性能が重要になってくる。メーカーでは、生産コストの見積り時に、以上の要素を十分に認識しているが、工作機械の特性を正しく評価せず、維持できないような切削条件を適用すると、見積りと実際のコストに大きな差が発生することになる。
初期の切削パラメータを決定するにあたり、どの加工にも共通の要件がある。切り込み深さと送り速度は、工具の破損を防ぎ、良好な切り屑形成と熱生成を抑えるよう選択する必要がある。切削速度が高すぎると工具の摩耗が早まり、低すぎると工具の生産性が落ちることになる。
一般に、高速の切削ではワークを短時間で加工できるが、しかしながら加工時間が短縮される一方で、工具寿命も短くなり、工具コストが上昇する結果となる。一回の加工に要する工具数が増え、摩耗した切刃の交換も必要となる。工具交換によるダウンタイムが発生するため、全体の加工コストが増加するため、高速で加工してコストをかけるか、低速で加工してコストを節約するか、このバランスをとることが必要である。
生産性と加工工程の安定性を一貫して維持できるポイントは、工具が効率よく機能せず生産性が損なわれるくらいまでパラメータを下げることによってコストを下げるか、短時間で工具が摩耗または破損するくらいまでパラメータを上げることによって生産性を上げるか、この 2 つのアプローチの中間にある。
さらに、切削条件の選択では、切削工具の特性だけでなく、多くの場合、工作機械の性能も考慮する必要がある。工作機械によって、電力、トルク、rpm および安定性の限界が異なります。最も明確な限界は電力である。
電力定格だけで、ある特定用途における機械の性能が決まるわけではない。60 kW の工作機械は、 要件に見合う以上の電力を提供するように思われるが、たとえば、長さ 12 m、直径 3 m の鍛造ロールを製造する場合などは、60 kW では不十分である。ある特定のワークを切削するのに必要な電力は、被削材、サイズ、切込み深さ、送り速度、切削速度により変わる。切削速度が高いほど切削抵抗が大きくなるため、電力需要が上がります。そのため、高速な切削速度では機械の電力定格を超える電力が要求されることがある。
また、極端な切削パラメータを選択すると、工作機械のその他の性能限界を超える影響が発生することがある。必要以上に大きい切り込み深さを選択すると、機械の構造的な剛性を超える抵抗が発生し、振動により加工品の品質が損なわれるおそれがある。同様に、送り速度が高すぎると切り屑の量が増え、切削工程を妨害したり、切り屑排出システムに詰まりが発生したりするおそれがある。
工作機械をその性能限界内で最大限に活用するには、切削パラメータの開発で賢く、バランスのとれたアプローチが必要になる。一般に、切削速度を落とすと、これに比例して送り速度と切り込み深さが上昇する。可能なかぎり最大の切り込み深さを採用すると(機械の安定性への影響を考慮しながら)、切削送りの回数が減り、これに伴い、加工時間が短縮される。通常、切込み深さは工具寿命にほとんど影響しないが、切削速度は工具寿命に大きく影響する。送り速度も最大にすべきだが、極端な送り速度により、ワークの仕上げ面品質が損なわれることがある。
メーカーは、送り速度と切り込み深さの信頼性の高い組み合わせを見つけたら、切削速度によって加工の最終補正をすることができる。目指すところは、高い生産性で材料除去率と加工安定性を両立する切削条件の採用である。機械の性能と切削パラメータを最適に組み合わせることにより、工具コストと加工の信頼性/生産性をバランスよく達成できる。
今後の戦略
工作機械の性能が加工工程の限界を決定することは確かだが、機械の入れ替えは簡単、迅速、安価なソリューションではない。切削工具に適用するパラメータを変更して、既存の機械の性能を最大限に発揮させるほうがすぐに簡単にできる。新しい工作機械への投資が実現可能だとしても、装置の耐用年数が比較的長い点をよく考慮すべきであろう。現在の需要に合った、またはそれを上回る性能の工作機械を購入したとしても、5 年、10 年と経過する間に、被削材、サイズ、分量が大きく変わる可能性もあり、その時点で同じ問題に直面するだろう。こうした変化に対応するには、切削条件を賢く変更することが不可欠である。
工作機械の金属切削時間を最大限に延長する方法を特定した後、ワークと加工に最適の工具、母材、コーティングおよび切刃形状を選択するのが望ましい手順である。次に、工具がうまく作動する最小の切削速度を適用する。その後、最大の送り速度と切り込み深さを適用し、工作機械の電力と安定性の特性も確認しておく。加工パラメータと機械の性能の最適な組み合わせを算出する数式が開発されている。可能であれば、現場で実際に試験を実施し、計算結果と整合するとよいだろう。数式は現実を確認するものでしかない。おそらく 90%以上の場合には、切削速度を抑えながら最大の送り速度と切り込み深さを適用するというアプローチが簡単な上、現実的で、切削速度を補正ツールとして使用すると最も高い効果が得られる。これが、使っている工作機械の性能を最大限に活用しながら、信頼性と生産性の高い加工を実現するのに最適なアプローチである。