無造作淑女
DMG森精機の「IGA INNOVATION DAYS2015」を一足早く見学
DMG森精機さんが、本日から4日間、同社伊賀事業所で「IGA INNOVATION DAYS2015」を開催するにあたり、昨日はプレスデーが開催されました。わたしも早朝3時に起きて、カメラを引っさげ伊賀に行って参りました。
↓関連記事はコチラ↓
http://seizougenba.com/node/6149
フロアスペースを拡張して全面リニューアルし、世界最大級の工作機械の展示場として生まれ変わったというだけあって、とても広々した中で、ゆっくりマシンを見学することができました。しかも豊富な見所を、産業別に分けていたこともあって、さらに分かりやすい展示となっていましたよ。
入口には、プレミアムパートナーシップを提携しているポルシェが鎮座しています。
そういえば昔、ポルシェのことを「ポルポル」って呼んでいたことを思い出しました。
さすがに最近はそんな呼び方はしませんね(笑)
痺れるくらいイカしています
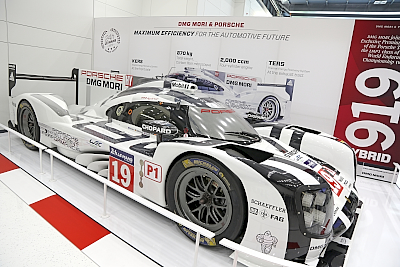
国内外から集まった報道関係者に森社長が説明をしてくれました。
ECOLINEシリーズはデザインを一新しています
ド迫力のBIGCELOS。実際に体験できます
今回、画期的だな、と思ったのは、50,000個以上の工具が保有できるツーリングルームが出来ていたことでした。顧客の材料や形状、設備等に合わせて、どんな加工条件が最適なのか――を模索する場所でもありました。昨日は顧客のテストカット用のツールも並んでいましたよ。まさに痒い所に手が届くような提案力だ、と感じました。
このレポートは後日、製造現場ドットコムのニュースに掲載いたしますので、お楽しみに!
MF-Tokyo アマダとマザックの見所
最近、ものすごい取材が混んじゃって、昨日の15日(水)から18日(土)までビッグサイトて開催しているMF-Tokyoが時間の関係上、ゆっくり観られないのが残念でしたが、ちょっとだけ足を運んできました。で、取り急ぎ、アマダさんとマザックさんのブースへGO。
なかなか面白い取組をしていたので、見学する方は参考にしてくださいね☆
アマダ社製のマシンを置いている他社ブースとも繋がっていた!
アマダさんのブースの中で「おっ!」と思ったのは、「プレス工場の見える化」を推進し、無線LANで繋がっている様子をブース内で見せていたこと。APINESサーバー(webサーバー)で同社ブース内の展示マシンのほか、今回は展示会場内にも他2社が同社のマシンを展示しておりましたが、それらを含む稼働状況などを見ることができました。タブレットやスマートフォンでも稼動情報や保全情報なども見ることができるんですよ。
マザックさんはサンプルワークの組立てを体験できるコーナーが人気!
マザックさんは、ブース内にて3DFABRI GEAR220Ⅱで加工した角パイプの組立を体験することができます。このマシンは国内外問わず好評のようです。興味のある方は高生産性・高精度の加工を体感できるチャンスです☆
他にもOPTIPLEX 3015 FIBERⅡがデザインを変えて新登場! マザックさんのデザインといえば、工業デザイナーで有名な奥山清行氏が担当しており、センスの良さはピカイチ! 目立ちます! マシンを工場内に置くだけでモチベーションが上がりそう!
2社ともまだまだ見せ場がありました。この続きはまた後日、製造現場ドットコムのニュースコーナーで掲載する予定です。お楽しみに!
さてさて、わたしの雨女っぷりはものすごいものがありますが、今日はどうしても関西入りしなければ、明日の仕事に間に合いませんので、なんとしても関西入りを果たします。
それでは、台風が上陸する予定らしいので、皆様もくれぐれも気をつけて下さいね。
ではよい1日を☆
【お知らせ】アマダ、アマダマシンツールがMF-Tokyo2015に出展
出展機:SDE-8018(SF)
アマダとアマダマシンツールが7月15 日(水)から7月18 日(土)まで東京ビッグサイトで開催されるMF-Tokyo 2015(プレス・板金・フォーミング展)に出展します。
MF-Tokyo 2015 は、日本鍛圧機械工業会および日刊工業新聞社が主催する塑性加工技術の専門展示会ですが、今回、アマダグループでは、「プロセス・イノベーション」~プレス量産加工ソリューション~をテーマに、アマダマシンツールからはサーボプレス2 機種とMF 技術大賞受賞製品を展示し、サーボプレスによる加工工程改革を提案してくれます!
また、アマダは板金加工技術サンプルを展示、さらに最新ファイバーレーザテクノロジーを加工サンプルなども紹介!
さて、今回の見所は、「デジタル電動サーボプレスSDE シリーズ」。
これは、日本鍛圧機械工業会のエコマシン認証を受けた省エネマシン。低速高エネルギーを確保できる専用サーボモーターを搭載し、パルスモーションなど多彩なモーションコントロールを持たせたことで、高精度加工、工程短縮、複合加工や難加工材の成形など高付加価値成形が可能。
モーション作成ソフトSMAPS(スマップス)にてプログラムの外段取り化に対応しているほか、荷重波形解析ソフトWANS(ワンズ)は、荷重・トルク・エネルギーといったプレス3能力のデータ収集解析が行え、品質の高い加工が再現できるんですって。
今回出展する「SDE-2025(SF)」では、独自のパルスモーションによる段付きギア加工の新工法を、また「SDE-8018(SF)」では、サーボダイクッションを用いた実演加工を行うとのこと。
さらに、プレスマシンの稼働状況や保全情報の見える化を実現したネットワークソフトAPINES(アピネス)も同時出展するんですって。
もうひとつ、見所のMF 技術大賞受賞製品の展示では、MF 技術大賞の創設以来、3回連続で顧客と共同受賞した製品「高精度ナックルリンクプレスによる高精度サイクロイドギアのプレス加工」、「サーボプレスの可変速度制御と電解水による3次元反射鏡加工」、「サーボプレスとインデックス装置によるキャリアカバー加工」を展示。板金加工技術サンプルの展示では、中厚板の工法転換による工数削減事例やステンレス製筐体の工程改革事例、VA/VE 提案事例と最新板金加工技術も紹介してくれます。また、最新ファイバーレーザテクノロジーも分かりやすく加工サンプルなどで見せてくれるとのこと。
なお、最新の板金マシンの実機は、アマダ・ソリューションセンター(神奈川県伊勢原市)で拝見できますよ。
同社では、「アマダグループのブースでは、プレス加工、板金加工の世界最高水準の加工技術をご覧いただき、お客さまの課題を解決するトータルソリューションをご提案いたします」としています。
お時間のある方はぜひ、足を運んでみて下さいね☆
【動画】ANGERのマシン
今回、アンガー・マシニング・ジャパンさんを取材してマシンの説明を受け、衝撃が走ったわけね。なんでしょう、この動き!
というわけで、どんな動きをするのか気になるアナタのために―――。
↓これをご覧下さい↓
今後の展開が楽しみなマシンです☆
業界最大規模のプライベートイベント『AMADA INNOVATION FAIR2015』が盛況のうち終了!
アマダさんがグループ各社と共同し、5月16日(土)から6月27日(土)までの毎週金・土曜日の13日間、神奈川県伊勢原市にある本社アマダ・ソリューションセンターで、プライベートイベント『AMADA INNOVATION FAIR2015(通称AIF2015)』を開催し、期間中、国内外から約5000人の来場者が足を運びました。大盛況でした。わたしが取材に行った日もたくさんの人で溢れていましたよ。
今回のイベントで注目したのは同社が推奨する「V-FACTORY~先進デジタル工場~」。
ここに生産現場の未来をみることができました。
このニュースはレポートとして近日中にお届けいたしますので、楽しみにしていてくださいね☆
驚愕の事実。本日をもって1年の半分が終了(’Α`;)
なんということでしょう。
本日をもって1年の半分が終了いたします。
それではよい〆日をお過ごし下さい―――といいつつ円高で半期締めとは・・・・・・製造業界はなんだかモヤッとしますなあ。
黒田精工が反響を呼んでるとのこと!
たったいま小耳に挟んだニュースなんですが、黒田精工さんがボールねじを使用する際にセットで使用する「直動ガイド」が来月販売するにあたり、一足早く東京ビッグサイトで開催されている機械要素技術展でご案内しているらしく早くも反響を呼んでるらしいわよ!
同社の得意としている中小径ボールねじの主要サイズをカバー可能なレール幅9番~25番までの5サイズをシリーズ化するんですって。
利便性もアップするとのことなので、興味のある方は機械要素技術展でぜひご覧になってくださいね☆
どこにも属さないわたし
どなたかがTwitterでつぶやいていた内容ですが、わたしも内閣官房のいうところの「5つの女性のシチュエーション」に、どこにも属さない人種だ。そのうち、わたしみたいなモンは、「人種」というカテゴリーからも外されちゃうかもしれん(笑)
もうさ、こんなに多様な世の中において、女性を表現するときに5つのカテゴリーしかないっていう定義がねぇ、発想が貧困すぎやしないか。ちなみに「女性の5つのシチュエーション」をいうと・・・。
①子育て前、産前産後
②子育て中、子どもが乳幼児
③子育て中、子どもが就学中
④ボスママ・先輩ママ
⑤介護・困難な状態
このように画一的に物事を決める風土があるから、属さない人間ははみ出しモノ扱いを受ける。(この風土は女性問題に限ったことではない)。自分の思い描いた「将来」を実現させるには、いろんなものを犠牲にせざるを得なかったけれど、現在、まだまだ向上心とあらゆる欲望はメラメラと燃えている。
つねに怠け心をひた隠し、どんなにくじけそうになっても、向上心をもって社会に対応できるよう努力はしてきたつもりだ。この「女性の5つのシチュエーション」を読む限り、その努力を「認めない」といっているに等しく感じて非常に残念な気持ちになった。
ちょっとひどくないかしら?
プロフィール
業界新聞社の取締役編集長を経て、インダストリー・ジャパンを設立。製造現場は日本の底力!をスローガンに製造業専門ニュースサイト「製造現場ドットコム」を運営している産業ジャーナリスト兼フリーライターです。霞ヶ関から錦糸町まで守備範囲が広いのが特長。現場取材は数知れず。些細なことや泥臭いことに真実が隠れているのを知り、今では何より本当のことを言うのが大好き。いつも働く女性と頑張るオヤジたちの味方よ。
ブログでは取材のこぼれ話やお知らせのほか、日常のことを綴っています。
機械振興会館 記者クラブ加盟
最近のブログ投稿
- 牧野フライス精機がInstagram公式アカウントを開設☆
- Xが突然使用不可! 現在、問い合わせ中です
- 【ニッチな皆様にお知らせ】オーエスジーダイヤモンドツールがキャンペーン中! 人気のステッカーやポーチが当たるゾ!
- 【取材こぼれ話】焼結前の超硬丸棒を折ってみた
- 【見逃し配信あり!】三井精機工業が「知られざるガリバー」(テレビ東京系列)に登場しました☆
- 猫好きにはたまらない名曲が誕生! メキシコJPOPチャート1位! ~君んちのニャンコと~
- 【告知】「INTERMOLD2025/金型展2025」で座談会
- 【お知らせ】日工会会員企業のテクトレージが提供している「キカイカタログ」
- 日本工作機械輸入協会 ボーリング大会で親睦を深めました☆
- 機械振興会館記者クラブ「共同取材」